Admin مدير المنتدى


عدد المساهمات : 18996 التقييم : 35494 تاريخ التسجيل : 01/07/2009 الدولة : مصر العمل : مدير منتدى هندسة الإنتاج والتصميم الميكانيكى
 | موضوع: كتاب Extrusion - The Definitive Processing Guide and Handbook السبت 30 سبتمبر 2023, 1:58 am | |
| 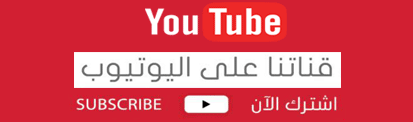
أخواني في الله أحضرت لكم كتاب Extrusion - The Definitive Processing Guide and Handbook by Harold F. Giles, Jr. John R. Wagner, Jr. Crescent Associates, Inc. Rochester, New York Eldridge M. Mount, III EMMOUNT Technologies Fairport, New York
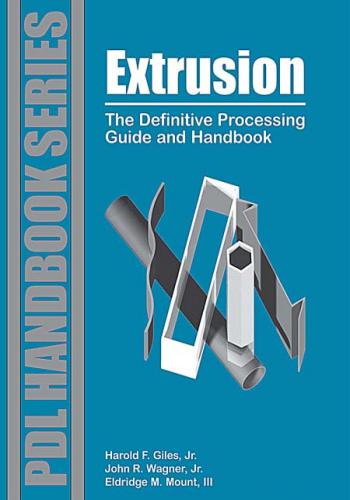 و المحتوى كما يلي :
Table of Contents Part 1: Single Screw Extrusion 1 Extrusion Process . 1 1.1 Raw Material Supply . 1 1.2 Raw Material Blending and Mixing . 2 1.3 Drying 4 1.4 Feeding Polymer to the Extruder . 4 1.5 Extrusion 5 1.5.1 Shaping and Drawing . 5 1.5.2 Solidification and Cooling . 6 1.5.3 Puller 7 1.6 Secondary Operations 7 1.7 Inspection, Packaging, and Shipping 7 Review Questions .8 2 Extruder Safety . 9 2.1 Hazards Associated with an Extruder 9 2.1.1 Hazards Associated with Takeoff Equipment 10 2.1.2 Personal Protective Equipment . 10 2.1.3 Lock-Out, Tag, and Clear Procedure . 10 2.2 Proper Training 11 2.3 Inspection and Housekeeping . 11 2.4 Material Safety 11 Review Questions 11 3 Single Screw Extruder: Equipment 13 Introduction . 13 3.1 Equipment 13 3.2 Drive 14 3.3 Feed . 16 3.4 Screw, Barrel, and Heaters . 16 3.5 Die and Adapter . 20 3.6 Controls 22 3.6.1 Temperature Zone Control . 23 3.6.2 Melt Temperature 26 3.6.3 Pressure Measurement 27 3.6.4 On-Line Measurements 29 3.6.5 Control Summary . 31 3.7 Extruder Devolatilization 31 3.8 Vertical Extruders 32 References 32 Review Questions 324 Plastic Behavior in the Extruder 35 4.1 Feed Zone 35 4.2 Polymer Melting or Plastication . 39 4.3 Melt Conveying 41 4.4 Mixing . 42 4.5 Extruder Throughput Calculations . 45 4.6 Devolatilization 47 4.7 Die 47 References 51 Review Questions 51 5 Screw Design . 53 5.1 Barrier Screw . 55 5.2 Mixing Screw . 57 5.3 Screw Wear . 59 5.3.1 Worn Screws . 61 5.4 Screw Compression Ratios . 61 5.5 Screw Performance . 61 5.6 Summary . 62 References and Photo Credits . 62 Review Questions 63 6 Processing Conditions . 65 6.1 Extruder Temperature Profiles 65 6.2 Extruder or Production Run Setup . 67 6.3 Start-up 68 6.4 Steady-state Operation 68 6.5 Shutdown and Product Changes . 69 References 72 Review Questions 72 7 Scale Up 75 References 77 Review Questions 77 8 Shear Rates, Pressure Drops, and Other Extruder Calculations 79 8.1 Shear Rates . 79 8.2 Extruder Screw Calculations 80 8.3 Calculations of Output in Different Sections of the Extruder 81 References 81 Review Questions 81 VIIIPart 2: Twin Screw Extrusion 9 Twin Screw Extrusion Process 83 9.1 Raw Material Supply 83 9.2 Raw Material Blending and Mixing . 84 9.3 Drying . 85 9.4 Feeding Polymer to the Extruder 86 9.5 Extrusion . 86 9.5.1 Shaping and Drawing 87 9.5.2 Solidification and Cooling 87 9.5.3 Puller . 88 9.6 Secondary Operations . 88 9.7 Inspection, Packaging, and Shipping . 89 Review Questions 89 10 Extruder Safety . 91 10.1 Hazards Associated with an Extruder . 91 10.1.1 Hazards Associated with Takeoff Equipment 92 10.2 Personal Protective Equipment 92 10.3 Lock-Out, Tag, and Clear Procedure . 92 10.4 Proper Training 93 10.5 Inspection and Housekeeping . 93 10.6 Material Safety 93 Review Questions 93 11 Twin Screw Extruder Equipment 95 11.1 Drive . 102 11.2 Feed 103 11.3 Screw and Barrel Heating and Cooling 105 11.4 Die and Adapter 109 11.5 Controls . 110 11.5.1 Temperature Zone Control 111 11.5.2 Pressure Measurement . 112 11.5.3 In-Line Measurements . 112 11.5.4 Control Summary 112 References and Photo Credits 112 Review Questions .113 12 Plastic Behavior in Twin Screw Extruders 115 12.1 Feed 115 12.2 Plasticating and Melting 117 12.3 Melt Conveying . 119 12.4 Mixing 119 12.5 Downstream Feeding . 121 12.6 Devolatilization . 123 12.7 Pumping 124 12.8 Die . 124 IX12.9 Melt Pressure Profile 129 12.10 Residence Time . 129 References and Photo Credits 130 Review Questions .131 13 Screw Design 133 13.1 Conveying . 133 13.2 Mixing Elements 134 13.3 Screw Design Applications 136 Reference . 139 Review Questions .140 14 Processing Conditions .141 14.1 Extruder Temperature Profile 141 14.2 Screw Speed . 142 14.3 Process Variables 143 14.4 Extruder or Production Run Setup 143 14.5 Start-Up . 144 14.6 Steady-State Operation . 145 14.7 Shutdown and Product Changes . 145 14.7.1 Disassembling Screw Elements 146 14.7.2 Scenario #1 . 147 14.7.3 Scenario #2 . 147 14.7.4 Scenario #3 . 147 14.7.5 Scenario #4 . 148 14.7.6 Scenario #5 . 148 14.7.7 Scenario #6 . 148 14.7.8 Scenario #7 . 149 14.7.9 Scenario #8 . 149 Review Questions .150 15 Applications .151 15.1 Compounding 151 15.2 Reactive Extrusion and Devolatilization 152 15.3 Profile and Other Twin Screw Extrusion Applications . 153 References and Photo Credits 155 Review Questions .155 16 Scale-Up .157 Review Questions .159 17 Shear Rate, Pressure Drop, and Other Extruder Calculations 161 17.1 Shear Rates 161 17.2 Extruder Calculations 162 17.3 Other Calculations 163 References . 163 Review Questions .163 XPart 3: Polymeric Materials 18 Polymer Overview and Definitions 165 18.1 Overview 165 18.2 Thermoplastic versus Thermoset . 167 18.3 Polymer Formation 168 18.4 Molecular Weight . 170 18.5 Copolymers 174 18.6 Polymer Structures 174 Review Questions .176 19 Polymer Structure 179 19.1 Amorphous Polymers 179 19.2 Semicrystalline Polymers . 181 19.3 Comparison of Semicrystalline and Amorphous Polymers . 182 19.4 Crystallinity Measurement 184 19.5 Polyethylene Crystallinity . 184 19.6 Polypropylene Crystallinity 184 19.7 Polystyrene Crystallinity 184 Review Questions .185 20 Polymer Rheology 187 20.1 Definitions 188 20.2 Measurement . 188 20.3 Viscosity in Extrusion 191 References . 193 Review Questions .193 21 Testing Properties 195 21.1 Density and Specific Gravity 196 21.2 Melt Flow Index 197 21.3 Tensile 197 21.4 Flexural Test . 199 21.5 Compressive Strength 199 21.6 Heat Deflection Temperature 199 21.7 Long-Term Heat Aging . 200 21.8 Thermal Properties 200 21.9 Time-Temperature Relationship 201 21.10 Izod Impact 201 21.11 Charpy 202 21.12 Comparative Thermoplastic Properties . 203 21.13 Polymer Additives . 203 21.14 Drying 203 Review Questions .204 XI22 Processing Recommendations for Various Resin Systems 207 22.1 Acrylonitrile Butadiene Styrene 207 22.1.1 Extrusion Temperature Profile 208 22.2 Polyamide . 208 22.2.1 Drying . 209 22.2.2 Extrusion Conditions 210 22.2.3 Amorphous Polyamide 211 22.3 Polyethylene . 211 22.3.1 Extrusion Conditions 211 22.4 Polymethyl Methacrylate (Acrylic) . 212 22.4.1 Extrusion Conditions 213 22.5 Polypropylene 213 22.5.1 Extrusion Conditions 213 22.6 Polycarbonate 214 22.6.1 Extrusion Conditions 214 22.7 Polystyrene 215 22.7.1 Extrusion Conditions 215 22.8 Polyvinyl Chloride 216 22.8.1 Extrusion Conditions 216 22.9 Polyester 217 22.9.1 Extrusion Conditions 218 References . 218 Review Questions .219 Part 4: Troubleshooting the Extrusion Process 23 Problem Solving 221 Review Questions .225 24 Five Step Problem Solving Process 227 24.1 Problem Definition 227 24.2 Fix the Problem 228 24.3 Identify the Root Cause 228 24.4 Take Corrective Action 230 24.5 Process Monitoring . 230 Reference . 230 Review Questions .230 25 Design of Experiments 231 25.1 DOE Process 231 25.1.1 Defining the Problem . 231 25.1.2 Plan the Experiment 232 25.1.3 Data Collection 233 25.1.4 Data Analysis 234 25.1.5 Report Conclusions . 234 25.2 Experimental Design 234 XII25.3 Experiments . 238 25.3.1 Factorial Design 238 25.3.2 Response Surface . 240 25.3.3 Mixture Experiments 242 References and Software Providers . 244 Review Questions .244 26 Quality . 247 26.1 Statistical Process Control 248 26.2 Process Capability 249 References . 250 Review Questions .250 27 Troubleshooting Mechanical Extrusion Problems 251 27.1 Problem 1—Extruder Screw Doesn’t Turn 251 27.2 Problem 2—DC Motor Will Not Start . 252 27.3 Problem 3—Drive Train Problems 252 27.4 Problem 4—Rupture Disk Failure in Barrel . 252 27.5 Problem 5—Barrel/Screw Wear 253 27.6 Problem 6—Screw Turns and No Material Exits the Die . 255 27.7 Problem 7—Extruder Shuts Itself Off . 255 27.8 Problem 8—Melt Flows Out the Barrel Vent 256 27.9 Problem 9—Leaking Polymer at Breaker Plate or Die . 257 27.10 Problem 10—Extruder Throughput Rate Is Lower than Anticipated 258 27.11 Problem 11—Temperature Overrides Setpoint . 259 27.12 Problem 12—Extruder Surging Caused by the Equipment . 260 27.13 Problem 13—Poor or Insufficient Polymer Mixing . 261 27.14 Problem 14—Throughput Variation Over Time 262 References . 262 Review Questions .263 28 Troubleshooting Extrusion Product Problems . 265 28.1 Problem 1—Product Surging 265 28.2 Problem 2—Variation in the Product Over Time 266 28.3 Problem 3—Random Product Variation 267 28.4 Problem 4—Streaks in the Product Caused by Poor Mixing 268 28.5 Problem 5—Variation in Product Strength 268 28.6 Problem 6—Product Degradation . 270 28.7 Problem 7—Dull Streaks . 270 28.8 Problem 8—Machine Direction Die Lines 272 28.9 Problem 9—Color Contamination 272 28.10 Problem 10—Holes in Extrudate . 273 28.11 Problem 11—Gels . 274 28.12 Problem 12—Gauge Variations . 275 28.13 Problem 13—Weld Lines . 276 28.14 Problem 14—Weak Film or Coating 276 28.15 Problem 15—Warpage . 277 XIII28.16 Problem 16—Sink . 278 Review Questions .279 29 Troubleshooting Sheet Extrusion 281 29.1 Mechanical Problems and Solutions . 281 29.1.1 Problem 1—Die Lip Damage Causing Defects in the Machine Direction . 281 29.1.2 Problem 2—Chill Roll Adjustment or Condition 282 29.1.3 Problem 3—Product Variations Caused by the Puller Rolls or Winder . 284 29.1.4 Problem 4—Static Charge Build-up on Sheet . 284 29.1.5 Problem 5—Other Equipment Problems . 284 29.2 Product Problems and Solutions 285 29.2.1 Problem 1—Sheet Product Contamination . 285 29.2.2 Problem 2—Poor and/or Nonuniform Gloss 286 29.2.3 Problem 3—Inferior Transparency . 287 29.2.4 Problem 4—Color Shift or Wrong Color 287 29.2.5 Problem 5—Sheet Is Brittle 288 29.2.6 Problem 6—Surface Voids, Indentations, and Imperfections . 288 29.2.7 Problem 7—High or Inconsistent Molecular Orientation 289 29.2.8 Problem 8—Warped Sheet . 291 29.2.9 Problem 9—Thickness Variations 292 29.2.10 Problem 10—Lines and Roughness on Sheet . 292 Review Questions .294 30 Troubleshooting Cast Film . 295 30.1 Problem 1—Molten Web Tears Easily When Exiting the Die . 295 30.2 Problem 2—Film Thickness Variation . 296 30.3 Problem 3—Lines, Streaks, and Foreign Contamination . 296 30.4 Problem 4—Extrudate Width Is Too Narrow 298 30.5 Problem 5—Wrinkles Are Formed in the Film 298 30.6 Problem 6—Roughness on Film Due to Melt Fracture 298 Review Questions .300 31 Troubleshooting Blown Film . 301 31.1 Problem 1—Bubble Instability . 301 31.2 Problem 2—Gauge Variation Around the Circumference 302 31.3 Problem 3—Wrinkles 303 31.4 Problem 4—Lines, Streaks, or Film Contamination . 304 31.5 Problem 5—Rough Film Due to Melt Fracture 304 Photo Credits 305 Review Questions .306 32 Troubleshooting Profile and Pipe . 307 32.1 Problem 1—Excessive Wall Thickness or Thinness . 307 32.2 Problem 2—Wavy Surface Inside Pipe or Tubing 308 32.3 Problem 3—Weld or Knit Line Weakness 309 32.4 Problem 4—Nonuniform Resin Velocity from a Profile Die 309 Review Questions .310 XIVPart 5: Auxiliary Equipment 33 Feed Systems 311 33.1 Feed System . 311 33.2 Blending Systems for Single Screw Extrusion . 314 33.3 Feeders . 321 33.3.1 Volumetric Feeder 322 33.3.2 Gravimetric Feeders . 325 33.3.3 Liquid Feeders . 328 References and Photo Credits 329 Review Questions .329 34 Drying 331 34.1 Drying Definitions and Factors Affecting Drying 333 34.2 Types of Drying Equipment . 334 34.2.1 Oven Drying System 335 34.2.2 Hopper Dryers and Central Drying Systems 336 34.3 Purchasing a Dryer 338 References . 339 Review Questions .339 35 Screen Changers . 341 35.1 Breaker Plate with Screens 342 35.2 Manual Screen Changer 343 35.3 Hydraulic Screen Changer 343 35.4 Double Bolt Screen Changer 344 35.5 Ribbon-Type Screens 346 35.6 Rotary Disk Screen Changer 346 References and Photo Credits . 347 Review Questions .348 36 Gear Pumps . 349 36.1 Gear Pump System 350 36.2 Drive and Control System . 352 36.3 Potential Gear Pump Problems . 354 36.4 Applications . 354 References and Photo Credits 356 Review Questions .356 37 Granulators . 357 Review Questions .360 38 Chillers and Heaters 361 38.1 Chillers . 361 38.2 Heaters . 363 Reference . 364 Review Questions .364 XV39 Screw Cleaning and Purge Compounds 365 39.1 Purge . 365 39.2 Mechanical Cleaning 369 References and Suppliers . 371 Review Questions .372 Part 6: Coextrusion 40 Coextrusion Applications 373 40.1 Film . 373 40.2 Sheet . 385 40.3 Pipe, Tubing, and Profile . 385 40.4 Wire Coating 388 40.5 Large-Part Blow Molding 388 References and Suppliers . 388 Review Questions .389 41 Feedblocks and Dies 391 41.1 Feedblocks . 391 41.2 Multimanifold Dies . 393 41.3 Feedblock Combined with a Manifold Die 398 41.4 Computer-Aided Design . 398 References and Suppliers . 399 Review Questions .399 42 Polymer Selection for Coextrusion 401 42.1 Melt Viscosity Matching 401 42.2 Interfacial Instability . 403 References . 409 Review Questions .409 43 Troubleshooting Coextrusion . 411 43.1 Problem 1—Nonuniform Cross or Transverse Direction (CD or TD) Layer Thickness . 411 43.2 Problem 2—Nonuniform Machine Direction (MD) Layer Thickness . 412 43.3 Problem 3—Interfacial Instability 412 43.4 Problem 4—Repetitive Layer Thickness Variations . 414 43.5 Problem 5—Layer Rearrangement . 415 43.6 Problem 6—Layers Aren’t the Correct Thickness 416 43.7 Problem 7—Poor Adhesion Between Layers in Structure 416 43.8 Problem 8—Structural Integrity Problems from Recycle 418 43.9 Problem 9—Haze Level Is Higher than Anticipated 419 43.10 Problem 10—Product Discoloration . 419 43.11 Problem 11—Gel or Lump Formation . 420 43.12 Problem 12—Warpage . 420 43.13 Problem 13—Regrind Utilization . 422 Review Questions .423 XVIPart 7: Extrusion Applications 44 Compounding . 425 44.1 Pelletizing Process 425 44.2 Operation 432 References and Suppliers . 433 Review Questions .433 45 Sheet and Cast Film 435 45.1 Sheet . 435 45.1.1 Die 435 45.1.2 Three-Roll Stack . 440 45.1.3 Puller Rolls . 442 45.1.4 Windup or Stacker 442 45.1.5 Thickness Measurement . 443 45.1.6 Operation 445 45.2 Cast Film 446 45.2.1 Die 447 45.2.2 Rolls . 447 45.2.3 Film Treatment . 449 45.2.4 Slitter 450 45.2.5 Gauging 450 45.2.6 Winders 450 45.2.7 Operation . 451 References And Suppliers . 451 Review Questions .452 46 Blown Film 453 46.1 Die . 454 46.2 Cooling . 456 46.3 Blown Film Tower . 457 46.4 Winders . 458 46.5 Gauging . 459 46.7 Operation . 459 References and Photo Credits 462 Review Questions .463 47 Extrusion Coating and Lamination 465 Review Questions .468 48 Wire and Cable Coating . 469 48.1 Pretreatment . 471 48.2 Die . 471 48.3 Downstream Equipment 472 48.4 Polymers 473 References . 474 Review Questions .474 XVII49 Profile Extrusion . 475 49.1 Die . 476 49.2 Calibration and Cooling Tank 479 49.3 Puller . 482 49.4 Cutters 483 49.5 Thermoplastic Materials . 484 References and Photo Credits 484 Review Questions .484 50 Pipe and Tubing Extrusion . 487 50.1 Die . 488 50.2 Cooling and Sizing 489 50.3 Puller . 494 50.4 Packaging . 495 50.5 Scale-Up 495 References and Photo Credits 495 Review Questions .495 51 Monofilament . 497 51.1 Die . 498 51.2 Quench Tank . 499 51.3 Drawing Unit with Ovens . 500 51.4 On-Line Gauging . 501 51.5 Creel . 501 51.6 Testing 501 Supplier . 502 Review Questions .502 52 Extrusion Blow Molding . 505 52.1 Parison Delivery System 506 52.2 Tooling . 507 52.3 Materials 511 52.4 Equipment Selection . 511 References . 512 Review Questions .512 53 Foam Extrusion 513 53.1 Blowing Agents . 514 53.2 Downstream Equipment 516 53.3 Microcellular Foam . 516 References and Suppliers . 516 Review Questions .517 54 Solid Stock Shapes . 519 Review Questions .521 55 Reprocessing 523 Supplier . 524 Review Questions .524 Glossary . 525 Index 539 IndexE elasticity 188, 198, 382, 408, 413, 419 embossing 448 EPDM 168, 378, 482 ethylene propylene polymers 168 ethylene vinyl alcohol 169, 373, 376 extensional viscosity 408, 409, 415 extruder drive 103, 108, 255, 256, 353 extrusion blow molding 176, 188, 211, 212, 368, 388, 505, 506, 507, 509, 511, 512 extrusion coating 382, 425, 451, 465, 466, 467, 468 F f ines 118, 337, 338, 357, 366, 428, 429 fishbone diagram 228, 229, 230 flame retardance 195, 214, 242, 247 flame retardants 1, 43, 59, 83, 95, 121, 151, 203, 261, 288, 311, 328, 524 flange 369, 501 flash 201, 506, 509, 523 flight depth 20, 55, 99, 210, 214, 215 flight pitch 118 flood feeding 4, 37, 39, 68, 321 foam extrusion 215, 513, 516, 517 foaming agents 515 Food and Drug Administration 195, 368 G gauge variation 282, 297, 302, 303, 355, 446, 447 gauging 7, 89, 447, 450, 459, 466, 501, 502 Gaylord 2, 84, 359 gel permeation chromatography 171, 173 glass transition 6, 49, 87, 126, 152, 179, 181, 185, 200, 201, 290, 338, 370, 426, 468 granulators 311, 357, 358, 359, 360, 523 granules 312, 324, 523 gravimetric feed 3, 85 H haul-off 457, 475, 482, 483, 496, 519 haze 419, 424, 448, 449, 453 heat deflection temperature 195, 199, 207 heat of fusion 80, 81, 162, 163, 183, 426 heat stabilizers 3, 85, 203, 433, 524 heater bands 9, 17, 21, 22, 39, 67, 109, 110, 233, 310, 328 heating zones 110, 436 helical gears 351 helix angle 18, 19, 20, 45, 46, 54, 55, 58, 76, 81 homopolymer 405 hydraulic screen changer 21, 343, 344 hydraulic slide plate 341 I inspection 7, 11, 89, 93, 196, 228, 337, 429 Izod Impact 201, 202 K K elvin 29, 192, 404, 405 L L/D ratio 14, 18, 50, 127, 214 laminar 39, 56, 57, 188, 373, 391, 401, 436 laminates 383 lamination 66, 174, 425, 435, 465, 466, 467, 468 lay-flat width 453, 460, 461 leakage flow 22, 42, 45, 97, 124 liner 17, 19, 107, 158, 210, 465 load cell 189, 318, 319, 321, 327 long-term heat aging 2, 84, 200, 201, 433 loss modulus 189 loss-in-weight 2, 3, 68, 84, 85, 103, 130, 144, 311, 319, 321, 325, 326 M masterbatch 3, 8, 85, 89, 312 mechanical cleaning 369, 370, 371 melt blockage 16 melt channel 26, 58, 124, 392, 472, 478, 488, 489 melt flow rate 197, 419 melt index 197, 211 melt instability 50, 127, 403, 443 melt plug 38, 52, 65, 69, 255 microcellular foam 513, 514, 516, 517 mixture experiments 234, 235, 236, 242, 245 540moisture-sensitive 4, 22, 86, 204, 210, 217, 219, 289, 311, 334 multimanifold dies 391, 393, 398, 399 N non-Newtonian 40, 46, 165, 187, 190, 193, 436 nonpolar 70, 148, 174, 295, 332, 374, 375, 449, 450, 466 Noryl 4, 61, 67, 85, 142, 152, 167, 195, 479 O orange peel 466 overall length 135 oxidation 27, 380 P P areto diagram 229, 230 permeability 20, 379, 382, 383 pilot 221 pinholes 381, 383, 460, 466, 473 plasticating 5, 13, 35, 39, 62, 109, 117, 119 plate-out 49, 127, 203, 271, 283, 285 Plexiglass 195 PMMA 46, 61, 67, 142, 167, 180, 195, 201, 219, 368, 369 pocket 14, 19, 20, 116, 332, 465 polyacrylonitrile 169 polybutylene 169 polybutylene terephthalate 4, 6, 85, 167, 217, 222, 332, 386, 473, 514 polychlorotrifluoroethylene 169 polydispersity 173, 177 polydispersity index 173, 177 polyetherether ketone 195 polyetherimide 167, 180, 195, 204, 332, 366 polyethylene terephthalate 4, 53, 85, 167, 217, 332, 373, 514 polyhexafluoropropylene 169 polymer additives 203, 205 polymer structures 169, 174 polymerization 30, 152, 153, 168, 169, 170, 173, 175, 176, 177, 347 polymethylmethacrylate 167 polymethylmethracrylate 195 polymethymethacrylate 169 polyoxymethylene 93, 195 polyphenylene oxide/polystyrene blend 167, 195 polyphenylene sulfide 167, 195, 386, 497 polyphthalamide 195 polysulfone 4, 67, 85, 142, 167, 180, 195, 204, 332, 365 polytetrafluoroethylene (Teflon) 169 polyurethanes 152, 168 polyvinylacetate 169 polyvinylchloride 169, 333, 473 polyvinyldiene fluoride 169 polyvinylidenechloride 169, 379 POM 195 power law model 46 PPO/PS 195, 365 PPS 167, 195, 204, 365, 367, 368, 386 practical residence time 98 pressure measurement 27, 28, 112 process capability 62, 249, 250 product changes 69, 145, 146, 223, 266, 311, 313, 320, 368, 448 profile and pipe 124, 307, 309 PSF 195 PSO 167, 195 PTA 195 puller rolls 284, 285, 294, 295, 435, 440, 442, 443, 445, 446, 453, 468 purge compounds 365, 366, 367, 368, 369, 371 pyrometer 271 Q quench tank 499, 500, 502 R recycled plastics 36 relaxation 5, 6, 48, 87, 126, 277, 477 relief 104, 122, 363 reprocessing 167, 311, 334, 425, 523, 524 residence time distribution 43, 98, 100, 101, 113, 129, 130, 153 rheometer 30, 189, 190 ribbon blender 3, 84, 314, 315, 316, 523 ribbon-type screen 341, 346, 348 Rockwell hardness 352, 438, 479 rotary disk screen changer 346, 347 INDEX 541S screw axis 58 screw cleaning 60, 311, 365, 367, 369, 371 screw performance 55, 62 sealing ring 257 shank 20, 32, 55 shaping and drawing 5, 87 sharkskin 49, 50, 52, 127, 128, 298 shear flow 40, 188, 190 shear strain 40, 44, 76, 188 shear thinning 40, 46, 165, 188, 191 sheet extrusion 96, 155, 215, 281, 283, 285, 287, 289, 291, 293, 347, 435, 452 sheeting 124, 154, 383, 425 shipping 1, 7, 35, 83, 89, 227, 373 shutdown 11, 65, 69, 93, 102, 141, 145, 223, 224, 228, 297, 338, 354, 395, 418 silo 2, 83 sink 274, 278, 279, 471, 477, 478, 484, 513 sleeve 352, 354, 469, 480 slitter 446, 450, 457 soak 13, 68, 144, 183, 251, 367, 440 solid shapes 519 solidification 6, 7, 87, 88, 121, 277, 290, 494, 507, 519 solidification and cooling 6, 87 solids conveying zone 116 SPE 62, 72, 112, 130, 244, 339, 356, 389 specific gravity 196, 197, 204, 207, 209, 229 spectroscopy 30, 32, 112, 184 spur gears 351 square pitch 19, 52, 54, 76, 134, 214 stacker 284, 435, 442, 443 standard deviation 61, 202, 233, 235, 236, 247, 249, 250, 321 starve feeding 4, 16, 36, 37, 86, 317, 322, 354 statistical process control (SPC) 7, 89, 224, 429 steady-state 65, 68, 141, 142, 145, 441, 460 steady-state operation 65, 68, 141, 145, 460 storage modulus 189 styrene acrylonitrile copolymer (SAN) 195 styrene butadiene copolymer (SB) 195 T thermal properties 200, 205 thermoform 385 thermoplastic polyesters 195, 514 thermoset 167, 168, 175, 176, 474 thickness gauges 31, 443, 444, 450 thickness measurement 443 three-lobe 98, 99, 113, 119, 131, 135, 157 throughput calculations 45 time-temperature relationship 201, 204 tooling 182, 478, 481, 482, 505, 507, 508 transparent 15, 180, 181, 182, 183, 211, 212, 215, 287, 301, 368, 444, 456, 459 tumble blenders 3, 84, 315 twin cone blender 314, 316 two-lobe 98, 99, 101, 113, 119, 135, 157, 163 two-stage screw 3, 20, 31, 33, 47, 212, 215, 227, 230, 256, 333, 513, 515 U ultraviolet 203, 269, 444 ultraviolet stabilizers 203 underwater pelletizing 361, 430, 431, 432, 434 UV resistance 195, 212 V v ent stack 75, 106, 107 vented extruder 4, 31, 47, 86, 213, 273, 333 vertical blender 314, 316 vertical extruders 32 viscoelasticity 154, 409 W warped sheet 291 windup 22, 23, 110, 111, 284, 295, 301, 306, 435, 442, 446, 448, 451, 453, 457, 466, 471 wire and cable 211, 354, 397, 469, 470, 471, 472, 473, 474, 523 wrinkles 298, 299, 303, 304, 465 Z zero defects 25
كلمة سر فك الضغط : books-world.net The Unzip Password : books-world.net أتمنى أن تستفيدوا من محتوى الموضوع وأن ينال إعجابكم رابط من موقع عالم الكتب لتنزيل كتاب Extrusion - The Definitive Processing Guide and Handbook رابط مباشر لتنزيل كتاب Extrusion - The Definitive Processing Guide and Handbook 
|
|