Admin مدير المنتدى


عدد المساهمات : 18994 التقييم : 35488 تاريخ التسجيل : 01/07/2009 الدولة : مصر العمل : مدير منتدى هندسة الإنتاج والتصميم الميكانيكى
 | موضوع: كتاب ASM Metals Handbook Vol 04 Heat Treating السبت 30 مارس 2013, 12:51 pm | |
| 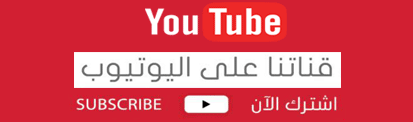
أخوانى فى الله أحضرت لكم كتاب
ASM Metals Handbook Vol 04 Heat Treating
ويتناول الموضوعات الأتية :
In compiling this new volume on heat treating, the challenge was to produce a book that contained subject matter strongly oriented toward industrial practice but that did not omit discussions of the underlying metallurgical fundamentals. With previously published ASM Handbooks devoted to heat treating, the omission of material on fundamentals was justified by either space limitations and/or the availability of other ASM books that described the physical metallurgy associated with thermal treatments. For example, when the 8th Edition was published in 1964, only 306 pages were related to heat treating (this Volume was divided between heat-treating technology and surface cleaning and finishing). As such, readers were referred to the classic book Principles of Heat Treatment by M.A. Grossmann and E.C. Bain, which was also published in 1964 by ASM. A similar situation arose in 1981 when the expanded 9th Edition Heat Treating Handbook was published. In the year prior to this publication, a completely revised version of the Grossmann/Bain book was prepared by G. Krauss and subsequently published by ASM. The 1980s proved to be a dynamic period for heat-treating technology--a decade that witnessed the introduction of new alloys and processes as well as new "tools" for understanding the response of heat-treated materials. For example, new alloys under active development or brought to market during the 1980s that were not described in previous heat-treating Handbooks included duplex stainless steels, microalloyed (HSLA) steels, low-cobalt maraging steels, austempered ductile iron, directionally solidified and single-crystal superalloys, and aluminum-lithium alloys. Changes in processing include improvements in continuous annealing, induction heating, and surface hardening operations using lasers or electron beams, the commercial viability of plasma-assisted case-hardening processes, and advances in thermomechanical processing. But by far the most dramatic changes in heat-treat technology that have marked the past decade have been those involving newly developed tools for improving process characterization and process control. These include improved instrumentation for controlling furnace temperature, furnace atmosphere, and surface carbon content, the practical application of statistical process control (SPC), and the use of computer modelling for both the prediction of hardness profiles after quenching and the quantitative modelling of properties after tempering or case hardening. It is this latter category of computer modelling that necessitates the inclusion of material on the basic principles or fundamentals of heat treating. For example, there are several articles in this Volume that deal with computer-assisted prediction of steel hardening and hardenability as a function of heat treatment parameters. In this regard, the primary measures of steel hardening are the end-quench hardenability curves (Jominy curves), isothermal transformation (IT) curves, and continuous cooling transformation (CCT) curves. In order to understand how computer programs can be used to calculate such diagrams, some brief background information is provided in several key articles to emphasize how these diagrams make possible the selection of steel and the design of proper heat treatments. Principal Sections Volume 4 has been organized into eight major sections: · Heat Treating of Steel · Surface Hardening of Steel · Heat-Treating Equipment · Process and Quality Control Considerations · Heat Treating of Cast Irons · Heat Treating of Tool Steels · Heat Treating of Stainless Steels and Heat-Resistant Alloys · Heat Treating of Nonferrous Alloys A total of 71 articles are contained in these sections. Of these, 16 are new, 17 were completely rewritten, with the remaining articles revised and/or expanded. In addition, several important appendices supplement the Volume. These include a glossary of terms, a temper color chart for steels, and tabulated austenitizing temperatures for steels. A review of the content of the major sections is given below; highlighted are differences between the present volume and its 9th Edition predecessor. Table 1 summarizes the content of the principal sections. Table 1 Summary of contents of Volume 4, Heat Treating, of the ASM Handbook Section title Number of articles Pages Figures(a) Tables(b) References Heat Treating of Steel 16 253 355 123 430 Surface Hardening of Steel 18 203 305 69 324 Heat-Treating Equipment 6 62 83 17 43 Process and Quality Control Considerations 9 135 130 43 190 Heat Treating of Cast Irons 5 42 67 19 27 Heat Treating of Tool Steels 4 56 48 34 20 Heat Treating of Stainless Steels and Heat-Resistant Alloys 3 51 41 53 23 Heat Treating of Nonferrous Alloys 10 124 147 77 72 Total 71 926 1176 435 1129 (a) Total number of figure captions; most figures include more than one illustration. (b) Does not include in-text tables or tables that are part of figures Heat Treating of Steel. This section begins with two entirely new articles that introduce the reader to the physical metallurgy of heat-treated steels and newly developed methodologies for quantitatively predicting transformation hardening in steels. These companion papers set the stage for a series of articles that describe specific types of heat treatments. Of particular note is the definitive treatise on "Quenching of Steel" by Bates, Totten, and Brennan. Featuring some 95 figures and 23 tables, this 55 page article has been substantially revised and expanded from previous Editions. Other highlights include new articles on continuous annealing, cryogenic treatment of steel, and thermomechanical processing of microalloyed steel. The section concludes with completely rewritten articles on heat-treat procedures for ultrahigh strength steels, maraging steels, and powder metallurgy ferrous alloys. Surface Hardening of Steel. As explained in the introductory article to this section, emphasis has been placed on thermally driven, diffusion processes that induce solid-state transformation hardening. These processes include flame hardening, high-energy processes that utilize laser beams or electron beams, and conventional surface treatments such as carburizing, nitriding, and carbonitriding. It is important to note the significant processing characteristics between the aforementioned processes and surface modification techniques 'such as ion implantation, PVD/CVD coatings, and surface melting/surface alloying processes that will be described in future volumes of this Handbook series. For example ion nitriding, which is described in this section, and nitrogen ion implantation are two distinctly different techniques for producing a case hardened surface layer. The implementation of each process, the characteristics of the case layers produced, the metallurgical strengthening mechanisms generated, and the economics and end use of each, are quite different. Ion nitriding is a thermally driven, equilibrium, diffusion process that produces a relatively deep (100 to 400 m), hardened, case layer. Nitrogen ion implantation is a non-thermal, non-equilibrium, physically driven, ballistic alloying process, which produces a relatively shallow (1 μm), extremely hard case layer. Ion nitriding is implemented at high temperatures in a glow discharge atmosphere, while nitrogen ion implantation is carried out at room temperature, at high vacuum, in a dedicated atomic particle accelerator. Case layer strengthening in ion nitrided surfaces is due primarily to formation of transition metal nitride precipitates, while strengthening in nitrogen ion implanted surfaces is due primarily to dislocation pinning. A summary of processing comparisons is given in Table 2. Table 2 Process characteristics comparison Process temperature Process Type Process time, h °C °F Process pressure, torr Case depth(a), μm Hardness(a), HRC Ion nitriding Thermal diffusion 10-30 500- 1100 900- 2000 0.2-5.0 400 62-67 Nitrogen ion Physical 1-6 <150 <300 10-6 1 80-90 (a) Value for steel Key additions to this section include articles that describe increasingly used processes such as plasma-assisted case hardening methods, boriding, and the Toyota diffusion process. Of critical importance to this section is the article "Microstructures and Properties of Carburized Steels" by G. Krauss which examines the correlation between processing, structure, and resulting fatigue, fracture, and wear properties of case-hardened steels. Heat-Treating Equipment. Types of heat-treating furnaces, the materials used to construct furnaces, and the advantages and limitations associated with each are described next. More emphasis has been placed on furnace energy efficiency and proper design than in previous Editions. Process and quality control considerations are more important than ever to heat treaters. Reliable sensors, computerized control equipment, and process control of heating and cooling and furnace atmospheres are described in detail in this section. Supplementing this material are new articles on the recognition and prevention of defects in heattreated parts and the use of computer programs for designing heat-treat operations and predicting the properties of heattreated steels. Because the heat-treating industry is being challenged to introduce statistical concepts in order to minimize variability and ensure consistent quality of heat-treated parts, an important article on "Statistical Process Control of Heat-Treating Operations" is also included. Emphasis is on the practical application of SPC concepts in order to demonstrate to heat treaters how to identify critical process parameters that influence product quality and how to establish methods to monitor and evaluate such parameters. Heat treating of cast irons is described in five articles. The "Introduction to Heat Treating of Cast Irons" was completely rewritten for this Volume. The remaining four articles contain new information on austempering of ductile iron and procedures for heat treating highly alloyed abrasion-resistant, corrosion-resistant, and heat-resistant cast irons. Heat Treating of Tool Steels. Because tool steels must be processed to develop specific combinations of wear resistance, resistance to deformation or fracture under high loads, and resistance to softening under elevated temperatures, proper heat treating is critical. This section describes the procedures and equipment necessary to meet these criteria. Heat Treating of Stainless Steels and Heat-Resistant Alloys. Procedures and process control for heat treating the principal types of stainless steels and superalloys are discussed in this section. The article on "Heat Treating of Superalloys" was completely rewritten for this Volume and includes information on both wrought and cast alloys, many of which are used in the aerospace industry. The article on refractory metals and alloys is completely new to the Handbook series. Heat Treating of Nonferrous Alloys. The principles which govern heat treatment of nonferrous alloys are first described in this final section of the Handbook. Differences between ferrous and nonferrous processing are highlighted. Nine articles follow on heat treating of specific classes of nonferrous alloys.
أتمنى أن تستفيدوا منه وأن ينال إعجابكم
رابط تنزيل كتاب ASM Metals Handbook Vol 04 Heat Treating

|
|