Admin مدير المنتدى


عدد المساهمات : 18996 التقييم : 35494 تاريخ التسجيل : 01/07/2009 الدولة : مصر العمل : مدير منتدى هندسة الإنتاج والتصميم الميكانيكى
 | موضوع: كتاب Professional Sheet Metal Fabrication (Motorbooks Workshop) الثلاثاء 12 يوليو 2022, 2:02 am | |
| 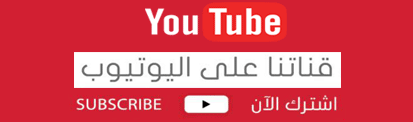
أخواني في الله أحضرت لكم كتاب Professional Sheet Metal Fabrication (Motorbooks Workshop) Cutting, shaping, and joining metal for any project Fabrication from simple patch panels to complex body parts Detailed instruction for welding, grinding, hammering, and shaping processes
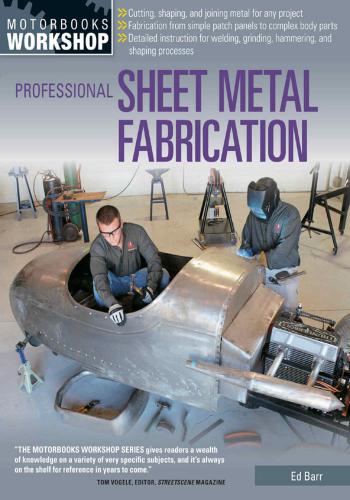 و المحتوى كما يلي :
Contents Introduction CHAPTER 1: Getting Started CHAPTER 2: Special Techniques for Welding Sheet Metal 24 CHAPTER 3: Brazing, Soldering, and Riveting CHAPTER 4: Cutting Sheet Metal with the Oxyacetylene Torch and Plasma Cutter 79 CHAPTER 5: Beginning Sheet Metal Shaping CHAPTER 6: The Small Gas Tank Project CHAPTER 7: Advanced Sheet Metal Shaping CHAPTER 8: Building a Fender from Concept to Completion . 187 CHAPTER 9: Making It Beautiful: Straightening, Grinding, and Surface Finishing 211 CHAPTER 10: Building a Custom Pedal Car CHAPTER 11: Floorpans, Rocker Panels, and Rear Quarter Panels 255 CHAPTER 12: Repairing Doors CHAPTER 13: Repairing Fenders, Hoods, and Trunk Lids . 280 Resources & Bibliography Index Index abrasive blasting, removing paint by, 213–214 acetylene, rate of flow, 80 acetylene cylinders about, 24–25 capacity, 80 fittings for regulator and hose, 28–30 moving and storing, 25–26, 28 obtaining/refilling, 25, 27–28 opening, 26–27 safety precautions, 25–27 shutting down, 34 acid core solder, 65–66 Aircraft Sheet Metal (Bonacci), 78 alignment, maintaining, 41–42 aluminum annealing, 98 brazing compared to torch welding, 62 buffing, 239 removing paint from, 213 shaping using stumps, 115, 116–120 thumbnail shrinking, 189–190 TIG welding, 48, 56, 58–60, 253 torch welding, 43–46 unreceptive to welding, 60 See also fender construction project Aluminum Association website, 43 aluminum oxide, for blasting corroded steel, 214 Amco 22 aluminum welding flux, 43 annealing, 10, 98 antique fender modification project, 219–223 argon for MIG welding, 48 for TIG welding, 55 Austin-Healey boot lid repair, 297 auto-darkening welding helmets, 47 Automotive Body Solder (Cowan), 72, 73 back purging, 60 backfires, 35 backhand welding, 37 Barton, Timothy Paul, 161 batteries, 5 bead rollers, 18 beading preparation of surface, 139 process, 140–145 with reciprocating machines, 166–169 bending, 95, 115, 135–136 Beverly shears, 15–16 blasting, removing paint by, 213–214 body hammers defined, 10 types, 11 body solder adhesion of lead to sheet metal, 67 advantages and disadvantages of, 67 defined, 10 lead sleds, 72–73 metal percentages in, 66–67 process, 67–71 safety, 67, 68, 72 Bonacci, Nick, 78 bonnet repairs, 298–300 boot lid repair, 297 boots, 5 brass, 65, 239 brazing advantages and disadvantages of, 62 process, 63–65 rods, 62–63 Bridigum, Todd, 24 bucks defined, 10 making wood, using Styrofoam models, 183–186 buffing and polishing, 238–241, 242 bull’s-eye picks, 10, 13–15 bumping hammers, 10, 11 Butler, Fay, 94–95, 161, 166 butt joints making on aluminum by TIG welding, 59 making on steel by TIG welding, 58 making with MIG welders, 52 making with oxyacetylene torches, 40–42 small floor repairs, 255–256 carbon dioxide, for MIG welding, 48 carbon steel, torch cutting, 80–81 carburizing flames, 31, 33 cast-iron and torch cutting an, 81 Caswell Plating, 239, 241 chemical dip stripping, 212 chemical paint strippers, 213 Chevy fender repair project, 286–288 chrome plating, 242, 243 clecos, defined, 10 clothing, safety. See protective clothing cold-shrink, defined, 10 cold-working, defined, 10 combination hammers, 11 compasses, using, 147–148 compound curves, making using English wheels, 128–131 conditioning treatments, 214, 215 copper buffing, 239 safety precautions, 73 silver solder and, 65 copying shapes, 146–149 corking tools, 10, 13 corrosion dissimilar metals and, 76 priming to avoid, 212, 213, 215, 292 Cowan, T. N., 72, 73 crimping. See tucking crisp lines, making using English wheels, 136–139 crowns, making using English wheels, 128–131 curves, making reverse, 169–173 custom pedal car project background of, 244–245 exhaust system fabrication, 248–252 grille fabrication, 252–253 steering wheel fabrication, 253–254 track nose fabrication, 245–248 wheel arch fabrication, 252 cut lines, 274 definitions of terms, 10 dents, tools for small, 15 designs, cutting tips, 83 detail work, making crisp lines using English wheels, 136–139 dies, choosing, 162 dinging hammers, 10, 11 documentation, importance of, 8–9 dolly blocks, 10, 11–12 doors gap repairs, 278–279 skin replacement project, 270–278 straightening project, 229–234 drag, described, 85 Drake power hammer, 161–162, 169 driving tools, 10, 13 Durbin, Bill, 214 dzus fasteners, 10, 78, 247 Eastwood Tinning Butter, 66, 67, 68–69 Eastwood tools, using, 16–18 elastic limit, described, 10, 161 electrical connections, solder for, 67 electroplating, 241–243 English wheels about, 10, 19 making bends using, 135–136 making compound curves using, 128–131 making crisp lines using, 136–139 tips for using, 132–134 envelope (of flame), 31 ER specification, explained, 48 eyewear, safety, 5, 34 face shields, 34 Fairmount tools, 10 feather (of flame), 31 fender construction project final adjustments, 203, 206–207 first steps, 188–190 options, 187–188 planishing, 203, 208–210 step-by-step first section construction, 190–201 welding, 201–206 fenders Chevy repair project, 286–288 dent repair project, 219–223 Ford repair project, 284–285 making shapes like, 169–173 Model A repair project, 289–293 Mustang repair projects, 281–284, 285 patch panels, 280 files, 16 filing, described, 220 filler rods for aluminum, 43–44, 46 for stainless steel, 60 for steel, 38–40 TIG welding and, 56–57, 58 flame colors (oxyacetylene welding), meanings of, 31–32 flange welds, 38 flexible patterns, 148 floorpan repairs, 255–257 floorpans large repairs, 256–257 small repairs, 255–256 flux for brazing, 63 for lead solders, 65303 for TIG welding of stainless steel, 60–61 for torch-welding of aluminum, 43, 45 flux-core wire arc welders, upgrading for MIG welding, 49 Ford fender repair project, 284–285 Ford grille shell project, 173–180 Ford Model A rear quarter panel repair project, 263–266 form/forming, defined, 95 Fournier Enterprises, 44 Franklin hood (1928) project, 294–296 gas welding. See oxyacetylene welding Glover, John, 19, 289 gloves, 5, 34 gouging described, 88 nozzle shield usage, 89 process, 91–92, 93 grains of metal, action of, 216, 218 grille shell project, 173–180 grinding welds, 237–238 GTAW (gas tungsten arc welding). See TIG welding hammerforms described, 10, 111, 112 fabricating wheel arches, 252 using, 111–114 hammers, 10–12, 97, 99 See also specific types of hammers hand-operated shrinkers/stretchers (Eastwood tools), 16–18 heat-shrinking described, 10, 102 example, 107–108 steel, 223–227 helium for TIG welding, 55 holes, filling, 54 hood repairs, 293–296, 298–300 How to Restore Metal Auto Body Trim (Lilly), 239 How to Weld (Bridigum), 24 hydrogen for welding aluminum, 43 hydrostatic test dates, 25 Hypertherm 45 (for plasma cutting), 89–90 jack stands, 7 kerf, described, 81 The Key to Metal Bumping (Sargent), 216 Knight, Scott, 235 labeling, importance of, 8–9 lead body solder adhesion of lead to sheet metal, 67 advantages and disadvantages of, 67 lead sleds, 72–73 metal percentages in, 66–67 process, 67–71 safety, 67, 68, 72 lead-free solder, 73–74 lead sleds, 72–73 leaf spring mounts, 7 Lilly, Jeff, 239 linear stretching dies/hammers, 10, 97 mallets, 15 Mar-Hyde Tal-Strip II, 213 Martin tools, 10 metal inert gas welding. See MIG welding metal memory, 214, 216 Metalshaping: The Lost Sheet Metal Machines (Barton), 161 MIG welding advantages and disadvantages of, 47 butt joints, 52 cut line, 274 equipment, 47, 48–50, 54 gases for, 48 grinding beads, 238 machine set-up, 50, 51 patching tips, 291, 293 process, 47–48 running beads, 50, 52–54 safety, 47 wire selection, 48 mini-power hammers, 161–162 Model A fender repair project, 289–293 MSC Industrial Supply, 295 Mustang fender repair projects, 281–284, 285 Mustang wheel arch repair project, 267–269 neutral flames, 31, 33 nickel plating, 242, 243 non-ferrous metals, torch cutting, 81 nozzle shields, 89 on and off dolly, defined, 10 oxidation, removing, 212–214, 215 oxidizing flames, 31, 33 oxyacetylene cutting torches. See torches (oxyacetylene cutting) oxyacetylene welding aluminum, 43–46 butt joints, 40–42 clothing for, 34 equipment set-up, 28–30 with filler rods, 38–40 hydrostatic testing of tanks, 25 lighting and adjusting torch, 30–33 manipulating torch, 35–37 metal for practicing, 34 running beads, 35, 37 shutting down torch, 34 supplies, 24–28 torch safety, 24, 34–35 work area, 34 See also acetylene cylinders; oxygen cylinders oxygen cylinders about, 24–25 fittings for regulator and hose, 28–30 moving and storing, 25–26 obtaining/refilling, 25 opening, 26 safety precautions, 25–27 shutting down, 34 paint, removing old, 212–214, 215 parts, keeping track of, 8–9 pasty ranges, described, 67 patches, making, 197–198 pedal car project. See custom pedal car project picking, described, 220 piercing, 91, 92 planish/planishing hammers, 168 described, 10 making reverse curves with, 169–173 planning, 6–7 plasma cutters cutting ability of basic, 79 parts of, 88–89 piercing vs. cutting capacity, 91 plasma cutting advantages of, 87–88 air pressure requirements, 89, 90 process, 87, 90–91 safety, 88 using Hypertherm 45, 89–90 plastic blasting media, 214 Plumb tools, 10 pneumatic combination hole punch and flanging tools (Eastwood tools), 16–18 polishing and buffing, 238–241, 242 pop rivets, 75 power hammers, 161–162 The Practical Sheet Metal Worker (Glover), 289 priming, to avoid corrosion, 212, 213, 215, 292 profile gauges, using, 146–147 projects antique fender modification, 219–223 Chevy fender, 286–288 door straightening, 229–234 fender dent, 219–223 fender shapes, 169–173 Ford fender, 284–285 Ford grille shell, 173–180 Ford Model A rear quarter panel, 263–266 Franklin hood (1928), 294–296 Model A fender, 289–293 Mustang fender, 281–284, 285 Mustang wheel arch, 267–269 shape copying, 121–128, 146–149 shot bags, 20–23 skin replacement, 270–278 small gas tank, 150–159 See custom pedal car project; fender construction project protective clothing, 5 for lead soldering, 67, 68 for MIG welding, 47 for torch cutting, 84 for torch welding, 34, 35 Proto tools, 10 prying tools, 13–15 puckers. See tucking puddles, creating, 34–35, 36 with filler rods, 40 pure movement, described, 161 quarter panel repairs access problems, 261–262 Ford Model A rear, 263–266 Mustang wheel arch, 267–269 planning, 260–261, 262 using ready-made panels, 259–260 reducing flames, 31, 33 resistance welders, 227–228 respirators, 67, 72 riveting making corrections, 78 process, 76–78 rivet selection, 75–76 rocker panel repairs, 257–259 rotisseries, 7 safety buffing, 240 clothing, 5 lead soldering, 67, 68, 72 MIG welding, 47 oxyacetylene torch cutting, 83, 84 oxygen and acetylene cylinders, 25–27304 INDEX plasma cutting, 88 sanding, 212 torch welding, 24 torch welding aluminum, 44 torch welding steel, 34–35 tungsten electrodes, 56 working with copper, 73 sand bags, 121 sanding, dangers of, 212 Sargent, Frank T., 216 Schelin, Wray, 235 shape/shaping copying, 121–128, 146–149 defined, 94–95 thickness and surface area relationship, 94–97 shears, 15–16 sheet metal brakes, 15–16 shoes, 5 short-circuit transfer gas metal arc welding. See MIG welding shot bags making, 20–23 using for shaping, 120–128 shrink, defined, 10 shrinking by cold tucking, 100–107 counteracting, 289 by heat tucking, 102–104, 106, 107–108 straightening and, 217–219 with thumbnail dies, 162–165 torch-shrinking steel, 223–227 using planishing hammers, 169–173 using resistance welders, 227–228 using shrinking discs, 235–237 using simple mechanical shrinkers, 109–111 using stud guns, 227, 228–229 using stumps, 115–116 shrinking discs, 235–237 shrinking hammers, 11 silver soldering, 65–66 slappers (slapping spoons), 10, 13 slip rolls, 19–20 small gas tank project, 150–159 smoothing, 115 Solar flux, 60–61 soldering lead-free, 73–74 silver, 65–66 soft, 65–66 See also lead body solder solid rivets, 75 spoons, 10, 12–13 stainless steel buffing, 239 TIG welding, 60–61 torch cutting and, 81 stakes, defined, 10 steel aluminum oxide for blasting corroded, 214 shrinking, 103–104, 106, 107–108 TIG welding, 48 torch cutting, 80–81 torch shrinking, 223–227 torch-welding butt joints, 40–42 with filler rods, 38–40 flange welds without filler rods, 38 manipulating torches, 35–37 practicing, 34 safety when, 34–35 straight lines, cutting tips, 83 straightening metal memory and, 214, 216–217 shrinking and, 217–219 stretching and, 217–219 torch shrinking steel, 223–227 work-hardening and, 214, 216 stretching defined, 10 straightening and, 217–219 using English wheels, 128–131 using mini-power hammers, 166 using planishing hammers, 169–173 using shot bags, 120–128 using shrinking hammers, 11 using simple mechanical stretchers, 109–111 using stumps, 115, 116–120 stretching metal, 97–99 stud guns, 227, 228–229 stumps described, 114–115 shrinking using, 115–116 stretching using, 115, 116–120 Styrofaom models, using, 183–186 surface finishing buffing and polishing, 238–241 grinding welds, 237–238 t-stakes, defined, 10 tare weight, 27 task lists, 6 templates location and relationship marking, 263 making, 146 terms, 10 thoriated tungsten, 56–57 thumbnail dies defined, 10 shrinking with, 162–165, 169, 189–190 TIG welding advantages and disadvantages of, 55 aluminum, 43, 46, 58–60, 253 cut line, 274 gases used, 55 grinding beads, 238 patching tips, 289, 291 process, 55–56, 57–58 stainless steel, 60–61 tungsten electrodes, 56–57 tin in solder, 66–67 Tinning Butter, 66, 67, 68–69, 72 tips (cutting) fuel usage of, 80 importance of size, 80, 85, 86 operation of, 81, 83, 85, 86 swapping welding and, 80 TM Technologies, 44 tools bead rollers, 18 corking, 10, 13 dolly blocks, 10, 11–12 driving, 10, 13 English wheels, 19 files, 16 hammers, 10–12, 97, 99 keeping track of, 8–9 for making wrinkles, 100 mallets, 15 prying, 13–15 purchasing, 160 quality, 10 shears, 15–16 sheet metal brakes, 15–16 slip rolls, 19–20 spoons and slappers, 10, 12–13 for structural repairs, 7 Vise-Grips, 15, 38, 40, 76–77 welding rods, 38–40 See also entries beginning with torches torch pops, 35 torch-shrinking steel, 223–227 torches (oxyacetylene cutting) cutting ability of basic, 79 process, 81–83, 84–87 safety, 83, 84 torches (oxyacetylene welding) filler rods and, 38–40 flange welds, 38 grinding beads, 238 grips, 34, 36 lighting and adjusting, 30–33 making butt joints using, 40–42 manipulating, 35–37 patching tips, 289 shrinking steel, 223–227 shutting down, 34 torches (TIG welding), 55, 58–59 trunk lid repair, 297 tucking process of cold, 101–107 process of hot, 102, 106, 107–108 tools, 10, 100 tungsten electrodes, 56–57 The Universal Sheet Metal Machine (Butler), 166 Victory White Metals, 67 Vise-Grips, 15 flange welds using, 38 making butting joints using, 40 using in riveting, 76–77 voltage, effect of changing, for MIG welders, 50, 53 weld grinding, 237–238 Weld Thru, 292 welding. See specific types of welding welding rods, 38–40 wheel arch, creating shape, 268 wheeling direction of, 263 pressure while, 271 process, 128–131 tips, 132–134 wire buck building, 180–183 wire edges, making, 142–145 wood bucks, based on Styrofaom models, 183–186 work-hardening, 10, 214, 216 wrinkles, tools for making, 100
كلمة سر فك الضغط : books-world.net The Unzip Password : books-world.net أتمنى أن تستفيدوا من محتوى الموضوع وأن ينال إعجابكم رابط من موقع عالم الكتب لتنزيل كتاب Professional Sheet Metal Fabrication (Motorbooks Workshop) رابط مباشر لتنزيل كتاب Professional Sheet Metal Fabrication (Motorbooks Workshop) 
|
|