Admin مدير المنتدى


عدد المساهمات : 18992 التقييم : 35482 تاريخ التسجيل : 01/07/2009 الدولة : مصر العمل : مدير منتدى هندسة الإنتاج والتصميم الميكانيكى
 | موضوع: كتاب High Integrity Die Casting Processes الأحد 01 يناير 2023, 10:00 am | |
| 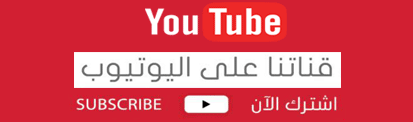
أخواني في الله أحضرت لكم كتاب High Integrity Die Casting Processes Edward J. Vinarcik
 و المحتوى كما يلي :
Contents Preface xv Figures and Tables xvii INTRODUCTION 1 1 Introduction to High Integrity Die Casting Processes 3 1.1 Origins of High Pressure Die Casting 3 1.2 Conventional High Pressure Die Casting 5 1.3 Problems with Conventional Die Casting 7 1.4 Strategies to Improve Die Casting Capabilities 10 1.5 High Integrity Die Casting Processes 10 References 11 2 Molten Metal Flow in High Integrity Die Casting Processes 13 2.1 Introduction 13 2.2 Flow within a Fluid 13 2.3 Flow at the Metal Fill Front 15 2.4 Metal Flow in Vacuum Die Casting 19 2.5 Metal Flow in Squeeze Casting 21 2.6 Metal Flow in Semi-Solid Metalworking 22viii CONTENTS 2.7 Predicting Metal Flow in High Integrity Die Casting Processes 24 References 24 HIGH INTEGRITY DIE CASTING PROCESSES 27 3 Vacuum Die Casting 29 3.1 Vacuum Die Casting Defined 29 3.2 Managing Gases in the Die 29 3.3 Managing Shrinkage in the Die 34 3.4 Elements of Vacuum Die Casting Manufacturing Equipment 35 3.5 Applying Vacuum Die Casting 40 References 42 Case Studies: Vacuum Die Casting 42 Introduction 42 B Post 43 Transmission Cover 44 Engine Component Mounting Bracket 45 Marine Engine Lower Mounting Bracket 46 Reference 49 4 Squeeze Casting 51 4.1 Squeeze Casting Defined 51 4.2 Managing Gases in the Die 53 4.3 Managing Shrinkage in the Die 54 4.4 Elements of Squeeze Casting Manufacturing Equipment 56 4.5 Applying Squeeze Casting 57 References 58 Case Studies: Squeeze Casting 58CONTENTS ix Introduction 58 Steering Knuckle 60 Valve Housing 61 Steering Column Housing 62 High Performance Engine Block 63 References 65 5 Semi-Solid Metalworking 67 5.1 Semi-Solid Metalworking Defined 67 5.2 Managing Gases in the Die 70 5.3 Managing Shrinkage in the Die 70 5.4 Microstructures in Semi-Solid Metalworking 71 5.5 Semi-Solid Metalworking Equipment 72 5.5.1 Billet-Type Indirect Semi-Solid Metalworking 73 5.5.2 Thixomolding Direct Semi-Solid Metalworking 79 5.6 Applying Semi-Solid Metalworking 82 References 83 Case Studies: Aluminum Semi-Solid Metalworking 84 Introduction 84 Fuel Rails 84 Control Arm 88 Swivel Bracket 89 Idler Housing 90 References 91 Case Studies: Magnesium Semi-Solid Metalworking 91 Introduction 91 Automotive Seat Frame 93 Wireless Telephone Face Plates 95x CONTENTS Video Projector Case 96 Camera Housing 97 Laptop Computer Case 97 Power Hand Tool Housing 98 References 100 6 Thermal Balancing and Powder Die Lubricant Processes 101 6.1 Thermal Cycling Inherent to High Integrity Die Casting Processes 101 6.2 Heat Checking and Soldering 102 6.3 Containing the Effects of Heat Checking and Soldering 103 6.4 Repercussion of Heat Checking and Soldering Containment Actions 105 6.5 Thermal Management of High Integrity Die Casting Process Tooling 105 6.6 Minimization of Thermal Cycling Effects with Powder Lubricants 106 6.7 Applying Thermal Management Methods in Real World Applications 108 References 109 DESIGN CONSIDERATIONS FOR HIGH INTEGRITY DIE CASTINGS 111 7 Design for Manufacturability of High Integrity Die Castings 113 7.1 Introduction to Design for Manufacturability 113 7.2 High Integrity Die Casting Design for Manufacturability Guidelines 113 7.3 Automotive Fuel Rail Case Study Review 114CONTENTS xi 7.3.1 Fuel Rail Functional Requirements 115 7.3.2 Case Study Analysis Method 115 7.3.3 Review of the Z-1 Fuel Rail Design 116 7.3.4 Review of the Z-2 Fuel Rail Design 118 7.3.5 Further Design for Manufacturability Improvements 121 7.4 Conclusions of the Case Study 122 References 123 8 Component Integration Using High Integrity Die Casting Processes 125 8.1 Introduction to Component Integration 125 8.2 Hidden Costs in Every Component 125 8.3 Analyzing Integration Potential 127 8.4 Component Integration Using High Integrity Die Casting Processes 127 8.5 Component Integration Case Study 129 References 130 9 Value Added Simulations of High Integrity Die Casting Processes 131 9.1 Introduction to Applied Computer Simulations 131 9.2 Computer Simulations of High Integrity Die Casting Processes 134 9.3 Applying Simulations Effectively 136 9.3.1 Resources 138 9.3.2 Planning 139 9.3.3 Coupling Product and Process Simulations 140 9.4 Commitment 140 9.5 A Case for Sharing Simulation Data across Organizations 140 References 141xii CONTENTS CONTROLLING QUALITY IN HIGH INTEGRITY DIE CASTING PROCESSES 143 10 Applying Statistical Process Control to High Integrity Die Casting Processes 145 10.1 Introduction to Statistical Process Control 145 10.2 SPC Characteristic Types 148 10.3 SPC Applied to Dynamic Process Characteristics 149 10.4 Die Surface Temperature Case Study 151 10.5 Applying SPC to High Integrity Die Casting Processes 154 References 155 11 Defects in High Pressure Casting Processes 157 11.1 Introduction 157 11.2 Conventional Die Casting Defects 157 11.2.1 Surface Defects 158 11.2.2 Internal Defects 159 11.2.3 Dimensional Defects 161 11.3 Defects Occurring during Secondary Processing 161 11.4 Defects Unique to Squeeze Casting and Semi-Solid Metalworking 162 11.4.1 Contaminant Veins 163 11.4.2 Phase Separation 165 11.5 Predicting Defects 167 References 168 VISIONS OF THE FUTURE 169 12 Future Developments in High Integrity Die Casting 171 12.1 Continual Development 171 12.2 New High Integrity Die Casting Process Variants 171 12.3 Refinements of Magnesium Alloys 172CONTENTS xiii 12.4 Emerging Alloys for Use with High Integrity Die Casting Processes 173 12.5 Metal Matrix Composites for Use with High Integrity Die Casting Processes 173 12.6 Reducing Tooling Lead Times 175 12.7 Lost-Core Technologies 176 12.8 Controlled Porosity 177 12.9 Innovations Continue 178 References 178 STUDY QUESTIONS 181 Appendix A Common Nomenclature Related to High Integrity Die Casting Processes 201 Appendix B Recommended Reading 207 B.1 Books 207 B.2 Papers 208 B.3 Periodicals 209 Appendix C Material Properties of Aluminum 211 References 211 Appendix D Die Cast Magnesium Material Properties 215 Reference 218 Index 219 INDEX Actuated shut-off valves, see Vacuum shut-off valves Aluminum alloy freezing ranges, 67–68 Aluminum alloys, 5, 22–23, 30, 45–46, 52, 60–63, 67, 71, 82, 84, 86–91, 102, 115–116, 159, 171–175 Atomized flow, see Liquid metal flow Bell laboratories, 147 Blistering, 10, 32, 34, 42–43, 47, 57, 61, 82, 162 Brass alloys, 5 Casting dies gating, 11, 19, 21, 51, 53–56, 70, 75–76, 117, 119, 141, 164–167 runner systems, 6, 11, 29–30, 36–37, 56, 58, 74, 76–77, 80, 104, 107, 141, 159, 162, 165, 167 Centerline porosity, 160 Chill-block shut-off valve, see Vacuum shut-off valves Chilled vents, see Vacuum shut-off valves Clausing, Don, 132 Cold shuts, 158 Common-cause variation, 146– 149, 153 Component integration, see Integration Composites, see Metal matrix composites Computer modeling, see Simulations Contaminant veins, 24, 32, 105, 163–165 Contamination, 160 Control factor flexibility curve, 132 Controlled porosity, 177–178 Corrugated chill block, see Vacuum shut-off valves Cracks, 8, 102, 158, 162 Defects dimensional, 161 internal, 159–161 prediction of, 167–168 from secondary processing, 161–162 surface, 158–159 unique to semi-solid metalworking, 162–167 unique to squeeze casting, 162– 165 Design for assembly, 127220 INDEX Design for manufacturability case study, 114–122 defined, 113 rules for high integrity die casting processes, 114 Die casting casting cycle, 6, 8 cold chamber, 5, 7 conventional high pressure, 3–5 cycle times, 5, 30, 34, 54, 57, 70, 82, 105, 107 hot chamber, 5–6 limitations of, 7–10 origins, 3–5 problems with, 7–10 strategies for improvement, 10 Die filling, see Metal flow Die lubricant, 6, 9, 29–30, 53, 70, 101, 104–106, 152, 158–161, 163, 165 Die surface temperature, 102, 151–155 Die thermal management, 101, 105–108 Dies, see Casting dies Discoloration, 158 Doehler, H.H, 3–5 Drags, 158 Electric shut-off valves, see Vacuum shut-off valves, dynamic Emerging alloys, 173 Erosion, 161 Fins, see Heat checking Flash, 158 Flux contamination, 160 Gas porosity, 29, 34, 53–54, 70, 160 Gutenberg, Johannes, 3 Hard spots, 161 Hawthorne works, 145 Heat checking, 102–106, 159 Heat treating, 10–11, 32, 34, 42– 43, 47, 51, 57–62, 82, 88–89, 91, 162 aluminum T5, 91 aluminum T6, 43, 47, 60, 61, 89 Hydraulic shut-off valves, see Vacuum shut-off valves, dynamic Inclusions, 160 Individuals chart, 150 Inherent variation, see Commoncause variation Integration, 86, 125–130 analysis flow chart, 128 case study, 129–130 costs, 125–127 Interdendritic porosity, 160 Intermittent variation, see Specialcause variation Laminar flow, see Liquid metal flow, laminar Laminations, 159 Lead alloys, 5 Life cycle cost lever, 133 Linotype machine, 3 Liquid metal flow atomized, 15, 19–20, 32, 53 in conventional die casting, 19– 20 at the fill front, 15–19 within a fluid, 13–15 laminar, 13–15 nonplanar, 16–19 planar, 16, 17 predicting, 24 in semi-solid metalworking, 22– 23 in squeeze casting, 21–22 turbulent, 13–15 in vacuum die casting, 19–21 Lost-core technology, 176–177 Magnesium alloy development, 172–173INDEX 221 Magnesium alloy microstructures, 80, 82 Mechanical shut-off valves, see Vacuum shut-off valves, dynamic Mergenthaler, Ottmar, 3 Metal Flow, see Liquid metal flow Metal matrix composites, 173–175 Microstructure of die welds, 103, 104 Nonplanar flow, see Liquid metal flow, nonplanar Phase separation, 165–167 Planar filling, see Liquid metal flow, planar Plunger lubricant, 6 Porosity, 160 gas, 29, 34, 53–54, 70, 160 quantified, 8–9 shrinkage, 7–9, 11, 35, 42, 61, 70, 117–121, 135 sources of gas porosity, 9 Powder die lubricants, 106–108 Powder lubricant application, 107– 108 Process data curves, 150–152 Process simulations, see Simulations Product integration, see Integration Reducing tool lead times, 175– 176 Reynolds number, 14–15 Reynolds, Osborne, 14 Rheocasting, see Semi-solid metalworking Rotary vane vacuum pumps, 35– 36 Semi-liquid casting, see Semisolid metalworking Semi-liquid metalworking, see Semi-solid metalworking Semi-solid billet anatomy, 77–78 behavior during heating, 77–78 dendritic case, 77 extruded, 77–79 magneto-hydrodynamic stirring, 76 Semi-solid casting, see Semi-solid metalworking Semi-solid metalworking aluminum, 67–68, 71–74 case studies, 84–100 comparison to conventional die casting, 82–83 compatible metal systems, 67 die design, 75, 80–81 direct process, 79 direct process manufacturing cell layout, 79–80 equipment, 72–82 heat treatability, 82–83 indirect process, 73–79 indirect process manufacturing cell layout, 73–75 magnesium, 70–82 microstructure (typical), 72–74 origins, 67 proper application of, 82–83 spheroidal microstructure, 71– 74 Shewhart, Walter, 145–147 Shrinkage porosity, see Porosity Short shot, 159 Simulations case studies, 134–138, 140, 141 commitment, 140 common types, 134 effectiveness, 138–139 of high integrity die casting processes, 134–140 planning, 138–139 resources required, 139–140 Sinks, 159 Sludge, 160–161 Soldering, 102–105, 159 Solidification, 3222 INDEX Solidification shrinkage porosity, see Porosity Special-cause variation, 146–153 Squeeze casting case studies, 58–64 comparison to conventional die casting, 57–58 equipment, 56–57 heat treatability, 57–58 microstructure (typical), 53–54 proper application of, 57–58 Squeeze forming, 51–52 Statistical process control applied to high integrity die casting processes, 154–155 case study, 151–154 dartboard comparison of variation, 146–147 of dynamic process characteristics, 149–151 identifying special-cause variation, 149–150 origins, 145–148 out-of-control signals, 149–150 process, 148 product, 148 Strategies for containing porosity, 10–11 Surface staining, 158 Surface veins, see Heat checking Thermal balancing of dies, 105– 106, 108 Thermal cycling of dies, 101–102 Thixocasting, see Semi-solid metalworking Thixomolding case studies, 91–100 machine, 79 magnesium microstructures, 80, 82 manufacturing cell layout, 79– 80 process, 79 runner design, 80–81 Titanium alloys, 173 Turbulent flow, see Liquid metal flow Vacuum die casting case studies, 42–49 equipment, 35–40 proper application of, 40–42 Vacuum pump operating curve, 35 Vacuum pumps, 35–37 Vacuum shut-off valves casting cycle, 32–34 dynamic, 38–40 effectiveness, 38–39, 41 maintenance, 38 placement, 32–33 static, 37–38 timing, 32–34 Vacuum valves, see Vacuum shutoff valves Valves, see Vacuum shut-off valves Venting effectiveness, 29–32 strategies, 32 Viscosity of semi-solid aluminum, 23 of liquid aluminum, 20, 22 Warpage, 161 Welding of dies, 103–104 Western Electric Company, 145, 147 X chart, 150 x-bar chart, 149 Zinc alloys, 3, 57, 62, 67
كلمة سر فك الضغط : books-world.net The Unzip Password : books-world.net أتمنى أن تستفيدوا من محتوى الموضوع وأن ينال إعجابكم رابط من موقع عالم الكتب لتنزيل كتاب High Integrity Die Casting Processes رابط مباشر لتنزيل كتاب High Integrity Die Casting Processes 
|
|