Admin مدير المنتدى


عدد المساهمات : 18996 التقييم : 35494 تاريخ التسجيل : 01/07/2009 الدولة : مصر العمل : مدير منتدى هندسة الإنتاج والتصميم الميكانيكى
 | موضوع: كتاب Fractography in Failure Analysis of Polymers الأحد 17 سبتمبر 2023, 1:57 am | |
| 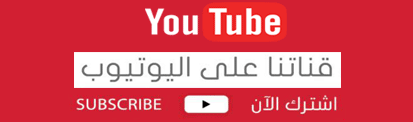
أخواني في الله أحضرت لكم كتاب Fractography in Failure Analysis of Polymers Michael D. Hayes Engineering Systems Inc. (ESI), Atlanta, GA, USA Dale B. Edwards Engineering Systems Inc. (ESI), Aurora, IL, USA Anand R. Shah Engineering Systems Inc. (ESI), Aurora, IL, USA
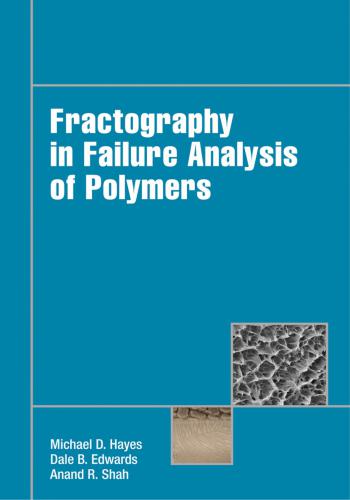 و المحتوى كما يلي :
Table of contents Foreword Preface Acknowledgments 1. Introduction 1.1 Motivations 1.2 What Is Fractography? 1.3 Plastic Material Structure–Property Relationship 1.4 Components of a Failure Investigation References 2. Fractography as a Failure Analysis Tool 2.1 Failure Analysis Fundamentals 2.2 The Scientific Method 2.3 Application of the Scientific Method 2.4 The Role of Fractography in Failure Analysis References 3. Instrumentation and Techniques 3.1 Field or Site Instrumentation and Techniques 3.2 Microscopic Examination of Fracture Surfaces in a Laboratory 3.3 Consideration and Selection of Instruments in Failure Analysis 3.4 Summary 3.5 Regulatory Agencies References 4. Fractography Basics 4.1 Fracture Surface Features and Interpretation 4.2 Brittle Versus Ductile Failures in Polymers 4.3 Crack Path Analysis 4.4 Fracture Features 4.5 Application of Fractography to Failure Analysis References 5. Long-Term Failure Mechanisms in Plastics 5.1 Introduction 5.2 Creep 5.3 SCG/Creep Rupture 5.4 Environmental Stress Cracking 5.5 Aging, Degradation, and Surface Embrittlement 5.6 Summary References 6. Case Studies 6.1 Introduction 6.2 Organization of Case Studies 6.3 Case Study 1: Composite Crossbow 6.4 Case Study 2: Showerhead Bracket 6.5 Case Study 3: Polycarbonate Axle Caps 6.6 Case Study 4: Hot Water Heater Drain Valve 6.7 Case Study 5: PEEK Coupling 6.8 Case Study 6: Icemaker Valve Failure 6.9 Case Study 7: Automotive Part, ABS 6.10 Case Study 8: Seat Belt 6.11 Case Study 9: Automotive Part, PC/ABS 6.12 Case Study 10: CPVC Cover Plate 6.13 Case Study 11: XLPE Storage Tank for Sulfuric Acid Storage 6.14 Case Study 12: Oxidation Failure of HDPE Pipe in Water Service 6.15 Case Study 13: Washing Machine Hose Failure 6.16 Case Study 14: Polyacetal Crimp Fittings 6.17 Case Study 15: PVC Water Main 6.18 Case Study 16: SAN Battery Cases 6.19 Case Study 17: Flame-Retarded Thermoformed PPE–PS 6.20 Case Study 18: 8-in. PVC Pipe 6.21 Case Study 19: Railcar Part, PPE+PS, 20% Glass Filled 6.22 Case Study 20: 48-in. HDPE Pipe 6.23 Case Study 21: HDPE Liner Pipe Used in a High-Pressure Steel Pipeline References 7. Epilogue 7.1 Failure Prevention Index Index Note: Page numbers followed by “f” and “t” refer to figures and tables, respectively. A Acetal, 1213 Acetal crimp fitting, degradation of, 106, 108f Acronyms, for commonly used plastic materials, 27t Acrylonitrile butadiene styrene (ABS), 104105, 141142, 143f, 144, 144f fractured ABS boat steering wheel, 106, 106f, 107f Aging, 103108 American Association for the Advancement of Science, 17 Amorphous thermoplastic, 3 Archive, 14 Argument from ignorance, 16 ASTM D1600, 2728 ASTM E1188, 36 Automotive part, ABS (case study) anti-rattle trigger post, fracture surface of, 143f, 144f anti-rattle trigger post, overall appearance of, 142f background, 141 conclusions, 144145 failure analysis, 141144 fracture, location of, 143f material flow and orange-peel-like surface finish of anti-rattle trigger post, 142f techniques, 141 Automotive part, PC/ABS (case study), 148152 background, 148 conclusions, 151152 failure analysis, 149151 fracture origin location, 150f fracture progression in brittle manner, 151f fracture surface under stereozoom optical microscope, 150f new uncracked and cracked PC/ ABS instrument panel, overall appearance of, 149f techniques, 148149 B Background information, gathering, 23, 2627 Beach marks. See Rib markings Bifurcations of crack, 52 Branching of crack. See Crack branching Brittle, 94 Brittle fractures, 5557 Brittle versus ductile failures, in polymers, 5360 cautions, 5960 plane stress and plane strain, 5759 C Carbonyl index (CI), 105106 Case studies, 111 automotive part ABS, 141145 PC/ABS, 148152 composite crossbow, 114120 CPVC cover plate, 152156 8-in. PVC pipe, 190195 227Case studies (Continued) flame-retarded thermoformed PPE-PS, 185190 48-in. HDPE pipe, 203211 HDPE liner pipe used in a highpressure steel pipeline, 211221 hot water heater drain valve, 128130 icemaker valve failure, 134141 oxidation failure of HDPE pipe in water service, 165168 PEEK coupling, 130134 polyacetal crimp fittings, 173177 polycarbonate axle caps, 123127 PVC water main, 177180 railcar part, PPE 1 PS, 20% glass filled, 195203 SAN battery cases, 180185 seat belt, 145148 showerhead bracket, 120123 washing machine hose failure, 168173 XLPE storage tank for sulfuric acid storage, 156165 Causes versus mechanisms, 67 Chemical evident on fracture surface, 53 Compound microscopes, 39 Compounding additives, 44 Conic markings, 88, 88f CPVC cover plate, case study, 152156 background, 152 conclusions, 155156 cracks at second machined hole in, 153f failure analysis, 152155 fluid emanating from crack in, 154f, 155f fracture origin area near machined hole, 154f fracture surface from fractured CPVC cover plate, 153f fractures at machined hole, 152f sharp ledges on very smooth surface, 154f techniques, 152 CPVC elbow fitting, 29 CPVC ESC failure, 89, 90f CPVC pipe, 8384, 85f crack in, 102f depict fracture surfaces of, 8384, 85f evidence of microductility on fracture surface of, 102f mechanically driven crack in, 103f Crack arrest marks, 7071 Crack branching, 52, 61, 62f Crack growth, 7, 5960, 61f, 77 Crack opening displacement, 34 Crack path analysis, 6162 Crack propagation, 74, 94, 165166, 190191 Crazing in polymers, 57 Creep, 9395 brittle, 94 deformation, 94 glass transition temperature, 95 response, 94 rupture, 94 failure, 4849, 8687 Critical stress, 98100, 102103 Crossbow, case study, 114120 additional secondary cracks along fractured area, 116f background, 114115 conclusions, 119120 fractured crossbow, 115f fractured end of, 116f large voids and stress whitening, 117f stress whitening and rubbed surface of, 119f surface damage near fracture origin area, 116f techniques/analysis, 115119 228 INDEXvisibility of internal voids on fracture surface, 118f visibility of large voids in the interior of stock, 118f voids near fracture origin at the underside of crossbow body, 118f wear marks on stock near fracture origin, 117f Cross-linked PE (PEX) pipe cracks branching in, 62f fracture origin at a void in, 65f undercut ledges on fracture surface near origin in, 90f in PEX tank fracture near origin, 90f D Damage development, 7 Daubert v. Merrell Dow Pharmaceuticals, Inc., 19 Deductive reasoning, 1416 Defects versus imperfections, 912 Degradation, 64, 7173, 103108 Design defects, 89 Design deficiencies, 1213 Differential scanning calorimeter (DSC), 44 Documentation, 26 photo, 31f, 35f Ductile creep failures, 95 Ductile failures, in polymers, 5360 Ductile fracture origin, 68f Ductility, on fracture surface, 49 Dye penetrants, 41, 42f E Electromagnetic lenses, 43 Embrittlement, 103108 Energy-dispersive X-ray spectroscopy (EDS), 171, 183, 192, 208 Environmental SEM (E-SEM), 4243 Environmental stress crack resistance (ESCR) testing, 208, 212 Environmental stress cracking (ESC), 96103, 127, 140, 152153, 155156, 181183, 185190, 196198 agent, 9697 characteristics of, 96 differentiating SCG/creep from, 100103 failures, 49, 67f Environmental variables affecting product performance, 225t Evidence, definition of, 14 F Fabrication errors, 89 Failure analysis fundamentals, 613 causes versus mechanisms, 67 defects versus imperfections, 912 design deficiencies, 1213 fractography’s role in, 2021 material selection, 1213 primary versus secondary causes, 8 root causes, types of, 89 Failure investigation, 23 basic elements, 17 components of, 34 “Failure of will,” fallacy of, 15 Failure prevention, 223226 Fallacies/user error, 1516 Fallacious logic, 1516 Fast fracture area on fracture surface, 5253 Fatigue striations, 7887 fatigue crack growth versus slow crack growth, 8387 on fracture surface of PS toothbrush failure, 7881, 80f on fracture surface of SAN field fracture, 7881, 80f on HDPE pipe fracture surface, 7881, 81f Field investigation, 2438 INDEX 229Field investigation (Continued) field microscopy, 37 information gathering, 2526 photogrammetry and digitization, 3738 product specific information, visual inspection for, 2633 visual and photographic techniques, 3337 Finite element analysis (FEA), 140f, 163, 171, 172f, 174175, 196, 200, 202 Flame-retarded thermoformed PPEPS, case study, 185190 background, 185 conclusions, 189190 cracking at thermoformed bend in the bus seat material, 187f cracking of plastic seat material adjacent to attachment to frame, 186f cracks around attachment hole in seat material, 186f failure analysis, 186189 SEM images of cracks, 187f smooth fracture origin at outer surface of the seat panel, 188f strain measurements, 188189, 189f techniques, 185186 Flaw, 10 Foreign materials on fracture surface, 53 Forking, 61 Fourier transform infrared (FTIR) spectroscopy, 152, 155f Fractography, definition of, 2 Fracture features, 6290 conic or parabolic markings, 88, 88f fatigue striations, 7887 fatigue crack growth versus slow crack growth, 8387 fracture origin(s), 6365 hackles, 7475 mirror zone, 6670 mist region, 70 ratchet marks or ledges, 8990, 89f rib markings/beach marks, 7073 river patterns or river markings, 7577 Wallner lines, 7778 Fracture modes, 5152, 52f Fracture origin, 6466 at geometric discontinuity in PMMA, 66f at an inclusion in PVC, 65f at a void in PEX tube, 65f Fracture surface, 4853 acrylic, 74, 76f bifurcations of crack, 52 crack branching, 52 ductility, 49 failure characteristics, 4849 fast fracture area on, 5253 foreign materials or chemicals on, 53 fracture direction for mating parts, 5152 location and nature of fracture origin, 49 microscopic examination of, 3843 optical microscopy, 3941 scanning electron microscopy (SEM), 4243 river patterns/hackles on, 77, 77f roughness, 50 slow crack growth (SCG) region on, 5253 smoothness, 50 straight/curved crack, 52 stress whitening on, 50 striations/lines on, 51 T-junctions, 52 undercut ledges on, 82, 90f various features of, 64f 230 INDEXFracture type, identification of, 21 Frye test, 19 G Gel permeation chromatography (GPC), 147148, 147t Glass transition temperature, 95 H Hackles, 7475, 75f HDPE liner pipe used in a highpressure steel pipeline, case study, 211221 background, 211212 conclusions, 220221 failed liner pipes long fracture surfaces in, 213f typical outer surface gouges and scratches on, 212f failure analysis, 212220 mechanical testing, 212 multiple fracture origins, 150151, 213215, 214f HDPE pipe, 49 48-in. HDPE pipe (case study), 203211 background, 203204 conclusions, 211 cracks on inner surface of pipe sample, 205f cracks in the pipe, exposing, 206f failure analysis, 209211 fracture surfaces of different cracks, 206f, 207f material testing, 208209 pipe section with approximate location of through-wall cracks, 204f section of HDPE pipe received for analysis, 203f techniques, 204209 wall thickness measurements, 204f, 205f crazing ahead of fatigue crack in, 70, 71f, 72f degradation of, 107108 failure in, 74f mud cracking of inner surface of, 108f point load failure in, 73f rib markings on, 73f in water service, oxidation failure of (case study), 165168 background, 165 conclusions, 168 crack in pipe after sectioning the pipe longitudinally, 166f embrittled inner surface, SCG, and mud cracking on inner surface of the pipe, 167f failure analysis, 166168 five mil depth of degraded material at inner surface, 167f HDPE pipe sample with crack, 166f techniques, 165166 HDPE tensile test specimen, 5455 before and after testing, 55f notched and cooled in liquid nitrogen, 56f tested with razor notch, 56f High-density polyethylene. See HDPE Hooke’s law, 5758 Hot water heater drain valve, case study, 128130, 128f background, 128 conclusions, 130 techniques and analysis, 128130, 129f Human roots, causes of failure, 9 I Icemaker valve failure, case study, 134141 background, 134135 conclusions, 141 failure analysis, 138141, 139f INDEX 231Icemaker valve failure, case study (Continued) Faro laser scan deviation plots for subject plate, 138f for typical exemplar plate, 138f inspection, 135137 crack on outlet stem portion of valve body, 136f lab examination, 135137 laser scan of guide plates, 137 separated valve body showing fracture surfaces, 136f subject icemaker, 134f, 135f Imperfections, 912 Inadmissible evidence, 15 Inductive reasoning, 1416 Information gathering, 2526 environmental factors, 26 Injection molding, 29, 30f Instrumentation/techniques consideration and selection of, 4345, 45t field/site investigation, 2438 field microscopy, 37 information gathering, 2526 photogrammetry and digitization, 3738 product specific information, visual inspection for, 2633 visual and photographic techniques, 3337 microscopic examination of fracture surfaces, 3843 environmental SEM (E-SEM), 4243 optical microscopy, 3941 scanning electron microscopy (SEM), 4243 regulatory agencies, 4647 Irrelevant evidence, 15 L Laser scanning, 25, 38 Latent roots, 9 Linear elastic fracture mechanics (LEFM), 179, 194 Linear-low-density polyethylene (PELLD), 28 Liquid crystal polymer (LCP), 82 fatigue failure in, 84f fracture origin at the edge of, 85f Litigation standard, 1820 Frye test, 19 physical evidence, 18 U.S. Federal Rules of Evidence 702 (FRE), 1920 Logic, definition of, 14 Logic fallacies, 1516 Long-term failure mechanisms, in plastics aging, 103108 creep, 9395 degradation, 103108 environmental stress cracking (ESC), 96103 differentiating SCG/creep from, 100103 SCG/creep structure, 9596 surface embrittlement, 103108 Low-density polyethylene (LDPE) resin, 145, 146f, 147148, 147f M Manufacturer, identifying, 28 Manufacturing date, documenting, 32 Manufacturing defects, 89 Material defects, 89 Material properties, 4445, 45t Material selection, 1213, 224 Microcracking, 35, 107f Microscopic examination of fracture surfaces, 3843 optical microscopy, 3941 scanning electron microscopy (SEM), 4243 environmental SEM (E-SEM), 4243 232 INDEXMicrovoids in plastics, 5960 Mirror zone, 6670, 69f Mist region, 70, 71f Mode of failure, 67 Mud cracking, 106, 108f N National Fire Protection Association (NFPA), 1617 Noryl resin, 185190, 195196, 202203 GFN2 701 material, 200202 stress rupture curve for, 202f mechanical properties of, 188t Nylon axial fatigue test, 82, 83f O Optical microscopy, 23, 3941 categories of, 39 limitations of, 4041 Organic synthetic polymers, 23 Oxidation induction time (OIT), 159160, 165166, 168 P Parabolic markings, 88, 88f Part failure, 12 PE 3408 tensile specimen brittle fracture of, 5455, 56f ductile failure of, 5455, 55f, 56f PEL model, 14 PELA model, 14 Photogrammetry and digitization, 25, 3738 laser scanning, 38 PhotoModeler Scanner software, 3738 Physical evidence, 16, 18 Physical roots, 9 Plane strain, 5759, 9596 Plane stress, 5759 Polyacetal crimp fittings, case study, 173177 background, 173 conclusions, 176177 crimp fitting assembly, schematic of, 175f failure analysis, 173176 field failure, 174f techniques, 173 Polycarbonate (PC) axle caps, case study, 123127 appearance of fracture surface showing crack initiation, 125f background, 123 conclusions, 127 failed axle cap with complete circumferential fracture, 124f failure analysis, 125127, 127f molding flaws, 125f, 126f observations, 123125 partial crack under flange near gate, 124f two truck wheel axle caps, 124f Polycarbonate part, depict fracture surfaces of, 8384, 86f Polyetherether ketone (PEEK) coupling, case study, 130134, 131f background, 130 conclusions, 134 failure analysis, 133134 multiple fracture origins and fatigue striations, 133f multiple initiation sites and fatigue striations, 132f observations, 130132 semi-elliptical fatigue fracture origins, 131f small cutout fragment, 131f fracture surface on, 131f surface and microvoids/ microcracks, 133f thin section of cutout fragment, mating fracture in, 132f Polyethylene (PE), 9798 high-magnification fracture surface in, 60f INDEX 233Polyethylene (PE) (Continued) low-magnification view of SCG in, 60f Polymer classification, 23 Polymer material variables, 224t Polymeric materials, basic fracture features in, 63t Polymethyl methacrylate (PMMA) fracture origin at geometric discontinuity in, 66f mirror zone at the origin area of brittle fracture in, 68f multiple crazes in, 54 Polyphenylene etherpolystyrene (PPE-PS) material, 50 ESC failure in, 51f Polystyrene (PS), 4849, 8182, 82f Polyvinyl chloride (PVC), 155156, 177180, 177f, 190195 8-in. PVC pipe, case study, 190195 background, 190 conclusions, 194195 crack initiation area, 193f critical pressure versus crack length, 195f failed PVC pipe, 191f failure analysis, 193194 fractographic observations prior to destructive examination, 191f fracture initiation region, 192f fracture surface, stereomicroscopy of, 192f techniques, 190192 fracture origin at an inclusion in, 65f fracture surface, parabolic markings visible on, 88, 88f PVC water main, case study, 177180 background, 177 conclusions, 180 fracture origin area in the bell end of PVC pipe, 177f fracture origin showing SCG area and fast fracture area, 178f techniques and analysis, 177180 Presuppositions, 1415 Processing variables, 224225, 225t Product performance, environmental variables affecting, 225t Product specific information, visual inspection for, 2633 Punctuation marks, 2728 R Railcar part, PPE 1 PS, 20% glass filled (case study), 195203 background, 195196 conclusions, 202203 cracking, 197f, 198f evidence of fibers running longitudinal to the direction of fracture, 200f failure analysis, 196202 finite element analysis, 200201 stress relaxation testing, 202 stress rupture testing, 201202 thermogravimetric analysis (TGA), 198200 fracture surface, examining, 199f techniques, 196 vent assembly, 197f Ratchet marks/ledges, 8990, 89f Red herring, 1012, 15 Retardation, 184 Rib markings, 7073, 72f, 73f, 74f River markings, 7577 River patterns, 7577 Root cause, 23 definition of, 8 failure analysis, 8 types of, 89 Rotational molding, 3233 Rubbers, 23 234 INDEXS Safety concerns, checking, 25 Scanned electron beam, 43 Scanning electron microscopy (SEM), 23, 4243, 113 environmental SEM (E-SEM), 4243 Scientific method, 1316 applications of, 1620 litigation standard, 1820 multidisciplinary approach, 1718 deductive versus inductive reasoning, 1416 Seat Belt, case study, 145148 background, 145 conclusions, 148 cracked LDPE seat belt scabbard, 146f failure analysis, 145147 LDPE seat belt scabbard, fracture surface of, 147f loading on seat belt scabbard, single point source of, 146f techniques, 145 Semicrystalline materials, 6667 Semicrystalline polymers, 3, 224225 Service life anomalies, 89 Shear yielding, 5657 Showerhead bracket, case study, 120123 background, 120 conclusions, 123 crack initiation at injection gate, 122f cracking at gate location, 121f failure analysis, 121123 fractured bracket, 121f hand-held shower product, overall view of, 120f higher magnification of crack at gate, 122f observations, 120121 Simple microscopes, 39 Site investigation. See Field investigation Slow crack growth (SCG), 48, 5253, 5960 continuous SCG in HDPE samples, 8485, 86f discontinuous SCG in HDPE samples, 8485, 87f versus fatigue crack growth, 8387 low-magnification view of, in polyethylene, 60f SCG/creep rupture, 9596 versus environmental stress cracking, 100103 Solid-state structure, development of, 224225 Stereomicroscopes, 39 Strain optical coefficient, 184 Straw-man argument, 16 Stress crack agents, 100t, 101102 Stress cracking failures in polyethylene, 9798 Stress intensity factor, 6970, 179180, 194 Stress state, 58 ahead of cracked or notched material, 58f in notched material, 59f Stress whitening on fracture surface, 50 Striations on fracture surface, 51 Structureproperty relationship, 23, 44 Styrene acrylonitrile (SAN) battery cases, case study, 180185 background, 180 conclusions, 185 example of cracks, 181f failure analysis, 183184 material found on fracture surface, 182f observations, 180182 INDEX 235Styrene acrylonitrile (SAN) battery cases, case study (Continued) photoelastic birefringence patterns around gates, 184f typical fracture surface, 182f Styrene acrylonitrile (SAN) field fracture, 7881, 80f Surface embrittlement of polymers, 103 T Tensile test, 54, 54f HDPE, 55f, 56f Thermoplastic, 23 Thermosets, 23 T-junctions, 52, 6162 Twist hackle, 7475, 76f, 77 U Undercut ledges on fracture surface, 82, 90f Uniaxial and biaxial stress states, 5657 U.S. Federal Rules of Evidence 702 (FRE), 1920 “Unobtainable perfection,” 15 User errors, 89, 15 UV degradation, 104 V Variabilities in materials, 10 Viscoelasticity, 9394 Visual and photographic techniques, 3337, 36t ASTM E1188, 36 digital camera and accessories, 3334, 34t hand-held instruments, 33 microcracks identification, 35 Visual inspection for product specific information, 2633 manufacturing date, documenting, 32 rotational molding, 3233 V-shaped dual gooseneck flexible light adapter, 39 W Wallner lines, 7778, 78f, 79f Washing machine hose failure, case study, 168173 background, 168 conclusions, 173 crack pattern on inner surface, 169f exemplar part, cross section of, 172f failed washing machine hose, 169f failure analysis, 171172 FEA of tube in bending that is constrained on right end, 172f fracture surface, 169f fracture surface, 170f observations, 168171 tool marks, 170f Wehnelt cylinder, 42 X XLPE storage tank for sulfuric acid storage, case study, 156165 background, 156158 bottom surface of the tank, 157f changes in elevation, visualizing, 160, 161f conclusions, 163165 crack in bottom panel, 157f ductility on fracture surface, 159f failure analysis, 159163 hackles in final fracture region near outer surface, 161f microcracking, 159f removed section containing crack (s), 157f step at tailing edge of a void in UHMWPE, 162f step in PC, 161f step in PE, 162f steps at an inclusion in PE pipe, 162f subject tank, 156f techniques, 158
كلمة سر فك الضغط : books-world.net The Unzip Password : books-world.net أتمنى أن تستفيدوا من محتوى الموضوع وأن ينال إعجابكم رابط من موقع عالم الكتب لتنزيل كتاب Fractography in Failure Analysis of Polymers رابط مباشر لتنزيل كتاب Fractography in Failure Analysis of Polymers 
|
|