Admin مدير المنتدى


عدد المساهمات : 18994 التقييم : 35488 تاريخ التسجيل : 01/07/2009 الدولة : مصر العمل : مدير منتدى هندسة الإنتاج والتصميم الميكانيكى
 | موضوع: كتاب Kinematic Geometry of Surface Machining السبت 14 أبريل 2012, 3:03 pm | |
| 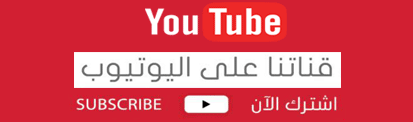
تذكير بمساهمة فاتح الموضوع : أخوانى فى الله أحضرت لكم كتاب Kinematic Geometry of Surface Machining Stephen P. Radzevich
 ويتناول الموضوعات الأتية :
Contents Preface . Author . Acknowledgments Part I Basics 1 Part Surfaces: Geometry 1.1 Elements of Differential Geometry of Surfaces . 1.2 On the Difference between Classical Differential Geometry and Engineering Geometry 1.3 On the Classifcation of Surfaces . 1.3.1 Surfaces That Allow Sliding over Themselves 1.3.2 Sculptured Surfaces . 1.3.3 Circular Diagrams . 1.3.4 On Classifcation of Sculptured Surfaces . References 2 Kinematics of Surface Generation . 2.1 Kinematics of Sculptured Surface Generation . 2.1.1 Establishment of a Local Reference System . 2.1.2 Elementary Relative Motions . 2.2 Generating Motions of the Cutting Tool . 2.3 Motions of Orientation of the Cutting Tool . 2.4 Relative Motions Causing Sliding of a Surface over Itself . 2.5 Feasible Kinematic Schemes of Surface Generation . 2.6 On the Possibility of Replacement of Axodes with Pitch Surfaces. 2.7 Examples of Implementation of the Kinematic Schemes of Surface Generation References 3 Applied Coordinate Systems and Linear Transformations 3.1 Applied Coordinate Systems 3.1.1 Coordinate Systems of a Part Being Machined . 3.1.2 Coordinate System of Multi-Axis Numerical Control (NC) Machine . 3.2 Coordinate System Transformation 3.2.1 Introduction 3.2.1.1 Homogenous Coordinate Vectors 3.2.1.2 Homogenous Coordinate Transformation Matrices of the Dimension 4 × 4 . 3.2.2 Translations . 3.2.3 Rotation about a Coordinate Axis . 3.2.4 Rotation about an Arbitrary Axis through the Origin . 3.2.5 Eulerian Transformation . 3.2.6 Rotation about an Arbitrary Axis Not through the Origin . 3.2.7 Resultant Coordinate System Transformation 3.2.8 An Example of Nonorthogonal Linear Transformation 3.2.9 Conversion of the Coordinate System Orientation . 3.3 Useful Equations 3.3.1 RPY-Transformation 3.3.2 Rotation Operator 3.3.3 A Combined Linear Transformation 3.4 Chains of Consequent Linear Transformations and a Closed Loop of Consequent Coordinate System Transformations 3.5 Impact of the Coordinate System Transformations on Fundamental Forms of the Surface . References Part II Fundamentals 4 The Geometry of Contact of Two Smooth, Regular Surfaces 4.1 Local Relative Orientation of a Part Surface and of the Cutting Tool 4.2 The First-Order Analysis: Common Tangent Plane 4.3 The Second-Order Analysis . 4.3.1 Preliminary Remarks: Dupin’s Indicatrix 4.3.2 Surface of Normal Relative Curvature . 4.3.3 Dupin’s Indicatrix of Surface of Relative Curvature 4.3.4 Matrix Representation of Equation of the Dupin’s Indicatrix of the Surface of Relative Normal Curvature 4.3.5 Surface of Relative Normal Radii of Curvature 4.3.6 Normalized Relative Normal Curvature . 4.3.7 Curvature Indicatrix . 4.3.8 Introduction of the Ir?k(P/T) Characteristic Curve 4.4 Rate of Conformity of Two Smooth, Regular Surfaces in the First Order of Tangency . 4.4.1 Preliminary Remarks 4.4.2 Indicatrix of Conformity of the Surfaces P and T . 4.4.3 Directions of the Extremum Rate of Conformity of the Surfaces P and T 4.4.4 Asymptotes of the Indicatrix of Conformity CnfR (P/T) . 4.4.5 Comparison of Capabilities of the Indicatrix of Conformity CnfR (P/T) and of Dupin’s Indicatrix of the Surface of Relative Curvature 4.4.6 Important Properties of the Indicatrix of Conformity CnfR (P/T) . 4.4.7 The Converse Indicatrix of Conformity of the Surfaces P and T in the First Order of Tangency 4.5 Plücker’s Conoid: More Characteristic Curves . 4.5.1 Plücker’s Conoid . 4.5.1.1 Basics . 4.5.1.2 Analytical Representation 4.5.1.3 Local Properties . 4.5.1.4 Auxiliary Formulas . 4.5.2 Analytical Description of Local Topology of the Smooth, Regular Surface P 4.5.2.1 Preliminary Remarks 4.5.2.2 Plücker’s Conoid 4.5.2.3 Plücker’s Curvature Indicatrix 4.5.2.4 AnR (P)-Indicatrix of the Surface P 4.5.3 Relative Characteristic Curves 4.5.3.1 On a Possibility of Implementation of Two of Plücker’s Conoids 4.5.3.2 AnR(P/T)-Relative Indicatrix of the Surfaces P and T 4.6 Feasible Kinds of Contact of the Surfaces P and T . 4.6.1 On a Possibility of Implementation of the Indicatrix of Conformity for Identifcation of Kind of Contact of the Surfaces P and T 4.6.2 Impact of Accuracy of the Computations on the Desired Parameters of the Indicatrices of Conformity CnfR(P/T) 4.6.3 Classifcation of Kinds of Contact of the Surfaces P and T . References . 5 Profiling of the Form-Cutting Tools of the Optimal Design . 5.1 Profling of the Form-Cutting Tools for Sculptured Surface Machining 5.1.1 Preliminary Remarks . 5.1.2 On the Concept of Profling the Optimal Form-Cutting Tool 5.1.3 R-Mapping of the Part Surface P on the Generating Surface T of the Form-Cutting Tool . 5.1.4 Reconstruction of the Generating Surface T of the Form-Cutting Tool from the Precomputed Natural Parameterization . 5.1.5 A Method for the Determination of the Rate of Conformity Functions F 1, F 2, and F 3 . 5.1.6 An Algorithm for the Computation of the Design Parameters of the Form-Cutting Tool 5.1.7 Illustrative Examples of the Computation of the Design Parameters of the Form-Cutting Tool . 5.2 Generation of Enveloping Surfaces 5.2.1 Elements of Theory of Envelopes . 5.2.1.1 Envelope to a Planar Curve 5.2.1.2 Envelope to a One-Parametric Family of Surfaces 5.2.1.3 Envelope to a Two-Parametric Family of Surfaces . 5.2.2 Kinematical Method for the Determining of Enveloping Surfaces . 5.3 Profling of the Form-Cutting Tools for Machining Parts on Conventional Machine Tools . 5.3.1 Two Fundamental Principles by Theodore Olivier 5.3.2 Profling of the Form-Cutting Tools for Single-Parametric Kinematic Schemes of Surface Generation . 5.3.3 Profling of the Form-Cutting Tools for Two-Parametric Kinematic Schemes of Surface Generation . 5.3.4 Profling of the Form-Cutting Tools for Multiparametric Kinematic Schemes of Surface Generation . 5.4 Characteristic Line E of the Part Surface P and of the Generating Surface T of the Cutting Tool . 5.5 Selection of the Form-Cutting Tools of Rational Design . 5.6 The Form-Cutting Tools Having a Continuously Changeable Generating Surface 5.7 Incorrect Problems in Profling the Form-Cutting Tools 5.8 Intermediate Conclusion References . 6 The Geometry of the Active Part of a Cutting Tool 6.1 Transformation of the Body Bounded by the Generating Surface T into the Cutting Tool . 6.1.1 The First Method for the Transformation of the Generating Body of the Cutting Tool into the Workable Edge Cutting Tool . 6.1.2 The Second Method for the Transformation of the Generating Body of the Cutting Tool into the Workable Edge Cutting Tool . 6.1.3 The Third Method for the Transformation of the Generating Body of the Cutting Tool into the Workable Edge Cutting Tool . 6.2 Geometry of the Active Part of Cutting Tools in the Tool-in-Hand System 6.2.1 Tool-in-Hand Reference System . 6.2.2 Major Reference Planes: Geometry of the Active Part of a Cutting Tool Defned in a Series of Reference Planes . 6.2.3 Major Geometric Parameters of the Cutting Edge of a Cutting Tool 6.2.3.1 Main Reference Plane 6.2.3.2 Assumed Reference Plane 6.2.3.3 Tool Cutting Edge Plane . 6.2.3.4 Tool Back Plane 6.2.3.5 Orthogonal Plane 6.2.3.6 Cutting Edge Normal Plane 6.2.4 Analytical Representation of the Geometric Parameters of the Cutting Edge of a Cutting Tool . 6.2.5 Correspondence between Geometric Parameters of the Active Part of Cutting Tools That Are Measured in Different Reference Planes . 6.2.6 Diagrams of Variation of the Geometry of the Active Part of a Cutting Tool 6.3 Geometry of the Active Part of Cutting Tools in the Tool-in-Use System . 6.3.1 The Resultant Speed of Relative Motion in the Cutting of Materials . 6.3.2 Tool-in-Use Reference System 6.3.3 Reference Planes 6.3.3.1 The Plane of Cut Is Tangential to the Surface of Cut at the Point of Interest M 6.3.3.2 The Normal Reference Plane 6.3.3.3 The Major Section Plane 6.3.3.4 Correspondence between the Geometric Parameters Measured in Different Reference Planes . 6.3.3.5 The Main Reference Plane . 6.3.3.6 The Reference Plane of Chip Flow . 6.3.4 A Descriptive-Geometry-Based Method for the Determination of the Chip-Flow Rake Angle . 6.4 On Capabilities of the Analysis of Geometry of the Active Part of Cutting Tools 6.4.1 Elements of Geometry of Active Part of a Skiving Hob . 6.4.2 Elements of Geometry of the Active Part of a Cutting Tool for Machining Modifed Gear Teeth . 6.4.3 Elements of Geometry of the Active Part of a Precision Involute Hob 6.4.3.1 An Auxiliary Parameter R . 6.4.3.2 The Angle fr between the Lateral Cutting Edges of the Hob Tooth . 6.4.3.3 The Angle x of Intersection of the Rake Surface and of the Hob Axis of Rotation . References 7 Conditions of Proper Part Surface Generation 7.1 Optimal Workpiece Orientation on the Worktable of a Multi-Axis Numerical Control (NC) Machine 7.1.1 Analysis of a Given Workpiece Orientation 7.1.2 Gaussian Maps of a Sculptured Surface P and of the Generating Surface T of the Cutting Tool 7.1.3 The Area-Weighted Mean Normal to a Sculptured Surface P 7.1.4 Optimal Workpiece Orientation . 7.1.5 Expanded Gaussian Map of the Generating Surface of the Cutting Tool 7.1.6 Important Peculiarities of Gaussian Maps of the Surfaces P and T . 7.1.7 Spherical Indicatrix of Machinability of a Sculptured Surface 7.2 Necessary and Suffcient Conditions of Proper Part Surface Generation 7.2.1 The First Condition of Proper Part Surface Generation 7.2.2 The Second Condition of Proper Part Surface Generation . 7.2.3 The Third Condition of Proper Part Surface Generation 7.2.4 The Fourth Condition of Proper Part Surface Generation 7.2.5 The Fifth Condition of Proper Part Surface Generation . 7.2.6 The Sixth Condition of Proper Part Surface Generation . 7.3 Global Verifcation of Satisfaction of the Conditions of Proper Part Surface Generation 7.3.1 Implementation of the Focal Surfaces 7.3.1.1 Focal Surfaces . 7.3.1.2 Cutting Tool (CT)-Dependent Characteristic Surfaces . 7.3.1.3 Boundary Curves of the CT-Dependent Characteristic Surfaces 7.3.1.4 Cases of Local-Extremal Tangency of the Surfaces P and T 7.3.2 Implementation of R-Surfaces . 7.3.2.1 Local Consideration 7.3.2.2 Global Interpretation of the Results of the Local Analysis . 7.3.2.3 Characteristic Surfaces of the Second Kind . 7.3.3 Selection of the Form-Cutting Tool of Optimal Design 7.3.3.1 Local KLR-Mapping of the Surfaces P and T 7.3.3.2 The Global KGR-Mapping of the Surfaces P and T 7.3.3.3 Implementation of the Global KGR-Mapping . 7.3.3.4 Selection of an Optimal Cutting Tool for Sculptured Surface Machining References . 8 Accuracy of Surface Generation . 8.1 Two Principal Kinds of Deviations of the Machined Surface from the Nominal Part Surface . 8.1.1 Principal Deviations of the First Kind . 8.1.2 Principal Deviations of the Second Kind 8.1.3 The Resultant Deviation of the Machined Part Surface 8.2 Local Approximation of the Contacting Surfaces P and T . 8.2.1 Local Approximation of the Surfaces P and T by Portions of Torus Surfaces 8.2.2 Local Confguration of the Approximating Torus Surfaces . 8.3 Computation of the Elementary Surface Deviations . 8.3.1 Waviness of the Machined Part Surface 8.3.2 Elementary Deviation hss of the Machined Surface . 8.3.3 An Alternative Approach for the Computation of the Elementary Surface Deviations . 8.4 Total Displacement of the Cutting Tool with Respect to the Part Surface . 8.4.1 Actual Confguration of the Cutting Tool with Respect to the Part Surface . 8.4.2 The Closest Distance of Approach between the Surfaces P and T . 8.5 Effective Reduction of the Elementary Surface Deviations 8.5.1 Method of Gradient 8.5.2 Optimal Feed-Rate and Side-Step Ratio 8.6 Principle of Superposition of Elementary Surface Deviations . References . Part III Application 9 Selection of the Criterion of Optimization . 9.1 Criteria of the Effciency of Part Surface Machining 9.2 Productivity of Surface Machining 9.2.1 Major Parameters of Surface Machining Operation 9.2.2 Productivity of Material Removal 9.2.2.1 Equation of the Workpiece Surface . 9.2.2.2 Mean Chip-Removal Output . 9.2.2.3 Instantaneous Chip-Removal Output 9.2.3 Surface Generation Output . 9.2.4 Limit Parameters of the Cutting Tool Motion 9.2.4.1 Computation of the Limit Feed-Rate Shift . 9.2.4.2 Computation of the Limit Side-Step Shift 9.2.5 Maximal Instantaneous Productivity of Surface Generation 9.3 Interpretation of the Surface Generation Output as a Function of Conformity References . 10 Synthesis of Optimal Surface Machining Operations 10.1 Synthesis of Optimal Surface Generation: The Local Analysis 10.1.1 Local Synthesis . 10.1.2 Indefniteness . 10.1.3 A Possibility of Alternative Optimal Confgurations of the Cutting Tool 4 10.1.4 Cases of Multiple Points of Contact of the Surfaces P and T . 4 10.2 Synthesis of Optimal Surface Generation: The Regional Analysis .4 10.3 Synthesis of Optimal Surface Generation: The Global Analysis .4 10.3.1 Minimization of Partial Interference of the Neighboring Tool-Paths 4 10.3.2 Solution to the Boundary Problem .4 10.3.3 Optimal Location of the Starting Point .4 10.4 Rational Reparameterization of the Part Surface 4 10.4.1 Transformation of Parameters 4 10.4.2 Transformation of Parameters in Connection with the Surface Boundary Contour 4 10.5 On a Possibility of the Differential Geometry/Kinematics (DG/K)-Based Computer-Aided Design/Computer-Aided Manufacturing (CAD/CAM) System for Optimal Sculptured Surface Machining . 4 10.5.1 Major Blocks of the DG/K-Based CAD/CAM System . 4 10.5.2 Representation of the Input Data . 4 10.5.3 Optimal Workpiece Confguration 4 10.5.4 Optimal Design of the Form-Cutting Tool .4 10.5.5 Optimal Tool-Paths for Sculptured Surface Machining .4 10.5.6 Optimal Location of the Starting Point . 4 References 4 11 Examples of Implementation of the Differential Geometry/ Kinematics (DG/K)-Based Method of Surface Generation 4 11.1 Machining of Sculptured Surfaces on a Multi-Axis Numerical Control (NC) Machine .4 11.2 Machining of Surfaces of Revolution 4 11.2.1 Turning Operations 4 11.2.2 Milling Operations . 4 11.2.3 Machining of Cylinder Surfaces .4 11.2.4 Reinforcement of Surfaces of Revolution 4 11.3 Finishing of Involute Gears 4 References 4 Conclusion 4 Notation 4
كلمة سر فك الضغط : books-world.net The Unzip Password : books-world.net أتمنى أن تستفيدوا منه وأن ينال إعجابكم رابط من موقع عالم الكتب لتنزيل كتاب Kinematic Geometry of Surface Machining - Stephen P. Radzevich رابط مباشر لتنزيل كتاب Kinematic Geometry of Surface Machining - Stephen P. Radzevich 
عدل سابقا من قبل Admin في الخميس 21 نوفمبر 2019, 5:08 pm عدل 6 مرات |
|