Admin مدير المنتدى


عدد المساهمات : 18996 التقييم : 35494 تاريخ التسجيل : 01/07/2009 الدولة : مصر العمل : مدير منتدى هندسة الإنتاج والتصميم الميكانيكى
 | موضوع: كتاب Complete Part Design Handbook - For Injection Molding of Thermoplastics السبت 19 أكتوبر 2019, 4:35 pm | |
| 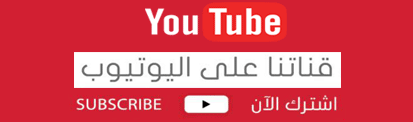
أخوانى فى الله أحضرت لكم كتاب Complete Part Design Handbook - For Injection Molding of Thermoplastics E. Alfredo Campo
 و المحتوى كما يلي :
Subject Index 855 Subject Index A abrasion resistance testing (ASTM D-1044) 740 abrasive wear 361 ABS (acrylonitrile-butadienestyrene) 2, 6 advantages 8 disadvantages and limitations 8 general properties of 7 typical applications 8 accelerated weathering testing (ASTM G 23) 821 acetal (POM, polyacetal) 9 acetal homopolymer bearing to acetal homopolymer shaft 361 to aluminum shaft 361 to nylon 6/6 shaft 361 to steel shaft 360 acrylamate 109 – acrylesterol 110 acrylesterol 109 acrylic (PMMA) 418 high impact 13 acrylonitrile-butadiene-styrene (ABS) 2, 6 additive deposits 674 adhesive application and curing methods 425 for acetal, polyacetal (POM) 422 for copolyester (TPE) 423 for other thermoplastic polymers 423 for polyamide (PA) 422 for polyethylene terephthalate (PET) 423 surface preparation 424 – abrasion 424 – chemical etching 424 – corona discharge 424 – degreasing cleaning 424 – flame treatment 424 – plasma treatment 424 ultra violet curable 421 adhesive bonding 416 acrylic (PMMA) 418 advantages 416 aging 420 anaerobics 418 – advantages 418 – – – – – – – – – – – – – – – – – – – – – – – – – – – – – disadvantages 419 – liquid form 418 cyanoacrylates 419 – advantages 419 – liquid form 419 cyanoadrylates – disadvantages 419 epoxy (EP) 416 – advantages 417 – disadvantages 417 – liquid paste form 416 flexibility 420 joint design for 425 other assembly considerations 420 PMMA – advantages 418 – disadvantages 418 – liquid paste form 418 selection 420 temperature 420 TPU – advantages 417 – disadvantages 417 – liquid paste solvent-based form 417 urethane (TPU) 417 adhesive concerns 419 adhesive families 416 adhesive wear 361 allocated direct investment (ADI) 844 alloy steels AISI 4340 566 nitralloy 135M 566 prehardened AISI 4130 565 prehardened AISI 4140 565 prehardened AISI 4150 565 allyl alcohol 85 anaerobics 418 angled pin slides 718 angle of twist 207 anhydride 85, 99 annealing 541 apparent modulus 130 appearance of product 119 arc ignition 788 arc resistance testing (ASTM D-495) 801 area centroid 150 area moment 150 – – – – – – – – – – – – – – – – – – – – – – – – – – – – – – of inertia 153 aromatic diamines 90 aromatic polyesteramide elastomers (PESA) 76 aromatic polyesters 25 ASA typical applications 54 assembly methods 405 assumptions 163 atactic PP 46 automation 837 auxiliary equipment 837 B bacteria resistance testing (ASTM G 22) 829 balanced geometrical configuration 547 banana gate 662 Barcol hardness testing (ASTM D-2583) 739 beam behavior of 158 bending moment 159 compound loads 184 concentrated end load 184 cross section shearing stresses 166 equally distributed load 184 equilibrium shearing stresses 166 loaded by lateral forces 170 loaded by transverse forces 164 maximum deflection 173 neutral surface of 158 normal stresses in 159 shearing stress 164, 167 simply supported 168, 174 – concentrated center load 174, 181 – couple loaded at one end 176 stress analysis of 158 beam deflection 168 analysis 168 bending moment 178 by double integration method 169 equations 186 fiber glass 146 moment area method 178 – – – – – – – – – – – – – – – – – – – – – – – – –856 Subject Index superposition method 183 bearing polyimide 366 reinforced Kevlar 375 TFE composite 373 bearing materials operating limits 364 behavior of thermoplastics effects of temperature 137 Belleville spring washer 388, 391 from acetal homopolymer 389 loading rate 392 long-term loading characteristics 392 bending moment 159 bevel gears 259 nonparallel and intersecting shafts 259 bis(3-aminopropyl)- polyoxytetramethylene glycol 75 bis(4-maleimidodiphenyl)methane (MDA BMI) 97 bismaleimide (BMI) 97 advantages 98 disadvantages and limitations 98 typical applications 98 bisphenols 89 blind hole 239 counterbored 239 protruding 239 bonding adhesive 413 solvent 413 boss 429 injection molded 222 inside diameter 430 outside diameter 430 boss dimensions for metal insert encapsulation 242 boss wall thickness for metal inserts 240 bottom clamping plate 581 BPA epoxy 112 advantages 113, 114 disadvantages and limitations 114 general properties of 112 typical applications 114 breaking strength 129 brittleness temperature (ASTM D-746) 768 burn marks 673 1,4-butanediol 72 butyl glycidyl ethe 93 – – – – – – – – – – – – – – – – – – – – – – – C calcium carbonate 516 cantilever beam 162 bending moment 162 free end, concentrated load 179 initial modulus of elasticity 381 load at the free end 171 maximum deflection 174 stress-strain curve 381 uniformly distributed load 174, 180 cantilever beam spring 379 design analysis 381 cantilever latch design and material considerations 454 tapered cross section 455 uniform cross section 454 cantilever latch beam assembly force 453 coefficient of friction 453 permissible deflection 452 cantilever spring acetal homopolymer 382 applications 385 empirical data 382 capillary rheometer melt viscosity testing (ASTM D-1703) 782 capital equipment 833 caprolactam 75 carbon arc light (ASTM D-1499) 823 cashew gate 662 cavity insert 698 sidewall strength 699 surface contact area (shut off) 714 cavity plate 580 celluloid 2, 88 cellulose acetate 2 α-cellulose fillers 87 cellulose nitrate 88 cellulosic acetate (CA) 88 cellulosic butyrate (CAB) 88 cellulosic ester 88 advantages 88 disadvantages and limitations 89 typical applications 89 cellulosic proprionate (CAP) 88 centroid 150, 155 chain extender 104 chamfer edges 715 Charpy impact testing (ASTM D-256) 755 chemical resistance 520 – – – – – – – – – – – – – – – – – – – – – – chip impact testing 755 chlorinated polyolefins 69 chlorotrifluoroethylene (CTFE) 40, 42 circular tooth thickness 300 clamping force calculations 835 coefficient of friction (ASTM D-1894) 742, 743 effects of lubricants 744 self lubricated additives 744 coefficient of linear thermal expansion 135, 245 testing 776 cold drawing 122 cold forged inserts types of materials used 243 cold forged metal inserts for encapsulation 243 cold heading 405 force required to form head 408 procedure and equipment 406 rate and type of loading 408 relaxation of stud and head 408 shaft geometry 407 strength of cold headed joints 408 cold runner cross section 646 dimensions 647 flow tab 654 layout 646 sprue 639 system 639 venting 687 column axially loaded in pinned ends 191 base fixed and free end axially loaded 191 central-supported, axial loaded, both ends fixed 190 eccentrically loaded 188 loading cases 193 long slender 188 pinned ends, axial loaded 189 slenderness ratio 188 structural analysis 188 comparative track index testing (ASTM D-3638/UL 746 A) 804 composite areas 152 compression curves 129 compression properties 733 compressive strength testing (ASTM D-695) 733 – – – – – – – – – – – – – – – – – – – – – – – – – – –Subject Index 857 apparatus 734 conditioning 734 test specimens 734 continuous elongation 122 cooling core insert 632 core valve ejector 637 mold cavity 630 mold cavity insert 631 mold plate 629 copolyester thermoplastic elastomer 71 core pin 716 core surface temperatures 720 corrosion 673 corrosive wear 361 cost analysis basic method 841 graph method 842 molded products 841 cost of sales 845 crazing 512 creep 139, 730, 761 behavior 138 modulus 764 – tests 773 rupture 765 – tests 773 test 730 under long-term load 139 crossed axial helical gears 262 cross linker 104 cross section 155 area 156 crown gears 260 crystallization rate 515 cyanate 89 advantages 91 characteristics 90 disadvantages and limitations 91 general properties of 89 typical applications 92 cyanate esters 89 cyanoacrylates 419 cycloaliphatics 92 cylindrical worm gears 261 D DAP advantages 86 disadvantages and limitations 86 general properties of 85 typical applications 87 – – – – – – – – – – – – – – – – – – – – – – – – – – – – deflection maximum 148 degradation 522 mechanical 522 microbial 523 radiation 522 density gradient testing (ASTM D-1505) 750 designer check list 119 design factors 119 diallyl phthalate (DAP) 86 diallyl phthalate/isophthalate (DAP, DAIP) 85 diamine 97 dibasic acids 99 dielectric constant 797, 798, 799 frequency 799 humidity 799 procedure 800 specimen 800 temperature 799 voltage 799 weathering 799 dielectric constant testing (ASTM D-150) 797 dielectric strength testing (ASTM D-149) 795 short-time test 795 step-by-step test 795 diglycidylether 90 dihydric alcohols 99 dimer acid 75 diphenyl-methane-diisocyanate (MDI) 104 diphenylmethane-4 109 4,4-diphenylmethane diisocyanate 58 direct investment (DI) 844 dissipation factor 798 testing (ASTM D-150) 800 double enveloping worm gears 261 double helical gears 259 double integration procedure 169 draft angles 715 draft walls 547 drawn-eyelet 239 drawn-pin 239 drawn-shell 239 drop weight impact testing (ASTM D-3029) 756 dry-as-molded 136 durometer hardness testing (ASTM D-2240) 739 – – – – – – – – – – – – – – E economic factors 119 edge gate critical dimensions 656 effects of the environment 521 ejection surface area 548 ejection systems 610 ejector blades 717 ejector guide posts and bushings 717 ejector housing 580 ejector pins 581 ejector plate 581, 611 assembly 611 return 717 ejector retainer plate 581 ejector sleeves 611, 717 ejector system 550 elastic limit 126 elastic properties 127 elastic ranges 127 elastomeric alloy thermoplastic vulcanized (TPV) 57, 65 electrical insulation properties 792 electrical lead inserts for encapsulation 253 electrical properties comparison of 809 testing 784 electrical resistance properties 792 electrofusion 408 fitting (SEF) 409 electromagnetic welding 458 advantages 458 applications 458 coil design 460 coils in series or parallel 463 combination coils 462 disadvantages 458 general design considerations 460 hairpin coils 462 joint design 463 materials used for the coils 461 multi-turn coils 462 pancake coils 462 process 459 single turn coils 461 split coils 462 types of coils 461 welding gasket 464 element moment 150 elongation at break 130 encapsulation 239 differential shrinkage effects 244 insert preparation 255 of reinforced metal inserts 253 – – – – – – – – – – – – – – – – – – – – – – – – –858 Subject Index environmental requirements 119 environmental resistance 520 EP advantages 93 disadvantages and limitations 94 general properties of 92 typical applications 94 epichlorohydrin 92 epoxidized butanol 93 epoxidized long chain mono alcohols 93 epoxidized phenols 92 epoxy (EP) 92, 416 ethylene-propylene-diene-monomer rubber (EPDM) 62 ethylene-propylene rubber (EPR) 62 ethylene chlorotrifluoroethylene (ECTFE) 40, 42 ethylene ethyl acrylate (EEA) 38 ethylene interpolymers 69 ethylene methyl acrylate (EMA) 38 ethylene N-butyl acrylate (ENBA) 38 ethylenetetrafluoroethylene (ETFE) 40, 41 ethylene vinyl acetate (EVA) 37 advantages 38 disadvantages and limitations 39 general properties of 37 typical applications 39 evacuation time 696 extensometer 123 external ring gate 658 F face gears 260 falling weight impact testing 757 fan edge gate 657 fatigue 761, 766 feather edges 547 fiber glass orientation flexural modulus 519 tensile stress 518 fiber glass reinforcement limitations 517 fiber reinforced resins isotropic warpage of 517 fiber reinforcements types of 516 – carbon 516 – glass 516 – high tensile organic fibers 516 – – – – – – – – – – – – – – – – inorganic 516 film edge gate 659 fixing clip spring applications 387 flame retardant polymers 810 flammability characteristics 809 flammable polymers 810 flash 413 ignition temperature testing (ASTM D-1929) 805 flashing 672 flat circular plate equations 196 flexible hinge applications 388 flexural beam stress distribution 145 flexural creep testing 762 flexural modulus 733 effects caused by fiber glass orientation 519 flexural stress 732 flexural testing (ASTM D-790) 730 apparatus 731 test procedures 732 flexure comparison 198 flow orientation 511 flow path 511 flow restriction 511 fluorescent UV lamp, condensation (ASTM G 53) 821 formaldehyde 87, 95 fumaric acid 99 fungi resistance testing (ASTM G 21) 828 G gate 655 effects 664 and mold venting systems 713 type and location 548 gearing design 257 gearing technology designs 294 gear manufacturing processes 257 chipless methods 257 finishing processes 257 metal removal 257 molding 257 gear roundness gating effects 275 gears backlash values 281 bevel gears 259 – nonparallel and intersecting shafts 259 – – – – – – – – – – – – – – – – – – classification of 258 crossed axial helical gears 262 crown gears 260 cylindrical worm gears 261 double enveloping worm gears 261 double helial gears 259 face gears 260 for straight linear motion 262 helical gears 258 helical rack gears 262 helicon and planoid gears 262 herringbone gears 259 horsepower equations 266 hour glass worm gears 261 hypoid gears 261 – nonparallel and nonintersecting shafts 261 internal gears 259 miter gears 260 mold shrinkage 287 mounting on metal shafts 279 multifunction designs 277 parallel to the shaft axis 258 selection of 264 single enveloping worm gears 261 single helical gears 258 skew bevel gears 260 spiral bevel gears 260 spiroid gears 262 spur gears 258 spur pinion gears 262 spur rack gears 262 standard injection molded gears 263 straight bevel gears 259 tolerances 287 worm gears 261 zerol bevel gears 260 gear safety stress 270 gear service factors 265 gears parallel to the shaft axis 258 gear total composite tolerances 283 glass transition temperature 513, 768 glow wire testing 807 glycidyls 92 H halogenated polyolefins 69 hardness scales comparison 740 heat capacity 514 – – – – – – – – – – – – – – – – – – – – – – – – – – – – – – – – – – – – –Subject Index 859 heat deflection temperature (ASTM D-648) 774 test – applied stress 775 – specimen molding 775 – specimen thickness 775 heat flow rate 622 heat transfer barriers 627 coefficient 622 helical compression springs 378 helical gear 258, 289 equations 289 HP (external and internal) 266 helical pinion and gear, 30 teeth or more 320 helical pinion and gear, less than 30 teeth 319 helical pinion less than 30 teeth and gear 30 teeth or more 319 helical rack gear 262 helicon and planoid gears 262 herringbone gears 259 heteroaromatics 101 high current arc ignition testing (UL 746A) 806 high density polyethylene (HDPE) 36 high temperature nylon (HTN) 14 high voltage arc tracking rate (UL-746 A) 803 method ASTM D-2132 803 method ASTM D-2303 803 hinge design side core insert mold 237 hoist ring 718 holes 718 tapped hole sizes 718 Hooke’s law 121, 125 horizontal burning testing (UL 94HB) 811 hot mandrel testing 807 hot plate welding 410 advantages 411 disadvantages 411 joint design 412 hot runner externally heated systems 595 insulated molding systems 597 internally heated systems 594 hot runner mold 588 gates (drops) 590 – hot spear tip thermo-valve gate 593 – – – – – – – – – – – – – – – – – – – – – – hot tip fixed and valve torpedo gates 592 – hot tip spreader insert gate 591 – reciprocating pin valve gate 592 – reverse taper sprue gate 591 – straight sprue gate 591 – straight sprue molten insulated gate 591 – tit edge gate 591 temperature control systems 589 – bands and coil heaters 590 – cartridge heaters 589 – cast-in heaters 590 – heat pipes 590 – torpedo heaters 590 – tubular heaters 589 valve pin gate 663 hot tip torpedo 600 hot wire coil ignition testing (UL 746A/ASTM D-3874) 807 hot wire ignition time 787 hour glass worm gears 261 hourly machine rate 845 HTN advantages 15 disadvantages and limitations 16 general properties of 14 typical applications 16 hub 143 hub/shaft coefficient of friction 441 hypoid gears 261 nonparallel and nonintersecting shafts 261 I impact fracture mechanism 752 impact resistance 513 testing 751 impact testing 760 injection mold classification 545 design considerations 545, 550 injection molding cycles 528 injection molding process effects on fiber glass orientation 517 injection pressure 653 inserts base wall thickness 241 minimum clearance 241 instrumented high speed plunger impact tester 760 instrumented impact testing 758 instrumented pendulum testers 758 – – – – – – – – – – – – – – – – – – – – – – – – – integral life hinges 232 design 233 interchangeable insert molds 585 internal gas voids 672 internal gears 259 internal ring gate 659 internal sharp corners 222 ionomer 16 advantages 17 disadvantages and limitations 18 typical applications 18 isochronous stress-strain curves 764 isocyanate 104 Izod impact testing (ASTM D-256) 753 J journal bearing annealing effects 354 axial and thrust grooves for lubrication 344 axial wall thickness 347 babbitt 336 bronze 336 carbon-graphite 337 cast-iron 337 clearances 365 coefficient of friction 359 design 335 – for lubrication 342 – principles 345 failures due to small clearances 360 felt snapped-on ring design 342 length-to-inside diameter ratio of 354 load carrying contact surface 350 load reaction across the length 350 lubricated axial groove oil wick with seal 342 lubricated axial oil wick with debris pocket 342 lubricated felt ring design 342 lubricated oil wick connected to rod bearing 342 materials used 335 mounting 347 plugged bronze 336 pressure equation 367 pressure-velocity (PV) limits 358 rubber 337 self-centering 348 self-lubricated 338, 363 sintered porous metal 336 – – – – – – – – – – – – – – – – – – – – – – – – – – – – – – – – – –860 Subject Index split bushing 348 temperature effects on 356 thermal effects on clearances 357 types of service and motion of 354 with round holes for lubrication/ debris trap 344 wooden 337 L Lame’s equation 396 layout of mold cavity and core inserts 714 LCP advantages 19 disadvantages and limitations 19 general properties of 18 typical applications 19 leader pins 581 and bushings 716 leakproof encapsulation of various inserts 253 Lewis tooth form factor 266 life hinges mold design considerations 235 proper gate design 236 lift holes 718 LIM advantages 80 disadvantages and limitations 81 general properties of 78 injection molding machine modifications 79 mold design recommendations 80 mold requirements 80 silicone processing 79 typical applications 81 limited oxygen index testing (ASTM D-2863) 815 linear low density polyethylene (LLDPE) 36 liquid components feeding system 79 liquid crystal polymer (LCP) 18 liquid injection molding 3 liquid injection molding silicone (LIM ) 77 loads types of 158 locating ring 580, 713 locating spring application 386 long molding cycles 673 long-term thermal aging index 772 – – – – – – – – – – – – – – – – – – – – – – – loss angle 798 loss index 798 lost core 602 molding machine – clamping system 604 – injection molds 604 – injection unit 604 low density polyethylene (LDPE) 36 lubrication hydrodynamics 339 M “MQ1” requirements 721 machine cost 836 machine nozzle 639 machine size 833 maleic anhydride 97 modified vinyl esters 113 manufacturing costs additional 848 material handling 833 material selection coefficient of thermal expansion effects 245 mathematical models 121 mating material hardness 362 surface finishing 362 mating spur gears tooth form comparison 304 maximum close mesh center distance 309 MDI 110 melamine formaldehyde 87 melamine formaldehyde (MF) 87 melt flashing inside the insert blind hole 249 melt flow 511 rate 781 – loading the polymer 781 – moisture 781 – preheat time 781 – volume of sample 781 testing 779 melt index testing (ASTM D-1238) 780 melting point 768 test (ASTM D-795) 767 melt processible rubber (MPR) 57, 69 melt viscosity 783 metal fasteners 427 metal insert 239 – – – – – – – – – – – – – – – – – anchorage for encapsulation 246, 250 drawn pin 251 drawn shell 251 flat plate 250 irregular shape 252 large drawn shell 252 large surface 252 thin tubular 250 metal insert encapsulating process problems 249 metal insert floating (movement) 249 metallocene polyethylene (MPE) 38 metaresin diallyl isophthalate (DAIP) 85 methylene dianiline (MDA) 97 MF advantages 88 disadvantages and limitations 88 general properties of 87 typical applications 88 miter gears 260 modified diphenylmethane-4,4- diisocyanate (MDI) 109 modified vinyl ester resins 113 modulus of elasticity 129, 733 moisture effects on nylon 523 mold cooling channel 619 heat removal 621 heat transfer 618 high volume production 546 production 546 prototype 545 surface finishing 571 – procedures 573 – diamond polishing 576 – electrical discharge machining (EDM) 573 – grinding 573 – machining 573 – stoning 574 mold amortization 845 mold base 578 “A” cavity plate 580 “B” cavity plate 580 bottom clamping plate 581 ejector housing 580 ejector pins 581 ejector plate 581 ejector retainer plate 581 functions of components 579 leader pins 581 – – – – – – – – – – – – – – – – – – – – – – – – – – – – – – – – – – –Subject Index 861 locating ring 580 return pins 581 shoulder bushings 582 sprue bushing 580 sprue puller pin 581 standard components 578 stop pins 581 support pillars 581 support plate 580 top clamping plate 580 mold cavity 606, 720 surface temperature 529 temperature control 530 mold cavity identification 711 mold cavity pressure monitoring 719 mold construction 709 finishing 712 requirements 713 welding 712 mold cooling 615, 638 channel location 619 fluid 628 system 549 mold cost 838 estimate factors 839 – per total mold cost factor 840 mold debug 720 mold deposit 669, 673 mold design 709 detailed 552 effects on the injection molding process 549 preliminary 551 mold drawing standards 709 molded-in stress 256, 512 molded parts tolerances 705 mold ejection air poppet valve ejection system 613 blade system 612 mechanical ejection valve system 613 pin system 612 stripper plate ejection system 614 mold general assembly 718 mold halves interlocks 719 mold identification tag 719 mold layout 552, 704 mold modifications documentation for 710 mold shrinkage 531, 538, 710 calculations 748 – – – – – – – – – – – – – – – – – – – – – – – – – – – – – – – process condition effects 533 mold shrinkage test (ASTM D-955) 744 conditioning 746 gate type 747 injection pressure 747 location 747 mold temperature 747 post molding testing 747 size 747 test conditions 746 test procedures 746 test specimens 746 wall thickness 747 mold steel 553, 557 chemical composition 559, 560 corrosion resistance 569 economical grade 569 finishing process 572 general grade 569 performance grade 569 surface finish 572 mold support pillars 705 mold temperature control 616, 715 mold tryout 720 mold venting 550, 666 design 674 logic seal 691 negative coolant pressure 691 process problems 672 molecular structure amorphous polymer 6 semi-crystalline polymer 6 moment area applications of 179 first theorem 178 second theorem 178 procedure 178 moment of inertia 150, 152, 155, 156 of a circle 153, 154 of a rectangle 153 of a semicircular area 154 T-section 154 MPR advantages 70 disadvantages and limitations 70 general properties of 69 typical applications 71 N neutral axis 156, 159 location of the 163 – – – – – – – – – – – – – – – – – – – – – – – – – – – – – – – – – – – – – – Newtonian flow 511 nitrile rubber 66 nonmetallic inserts for encapsulation 255 notches 222 novolac two stage-(novolac) resin 95 epoxy polymers 113 Nusselt laminar flow number 621 Nusselt turbulent flow number 621 nylon 2 moisture effects 136 O open hole 239 organic acid 85 orthoresin diallyl phthalate (DAP) 85 OSA typical applications 54 outdoor weathering testing (ASTM D-1435) 827 overlap edge gate 657 oxidation photo 522 oxidizing olefins 92 P PA advantages 22 disadvantages and limitations 22 typical applications 22 PA 6 general properties of 20 PA 6/12 general properties of 21 PA 6/6 general properties of 20 PAK advantages 84 disadvantages and limitations 85 general properties of 84 typical application 85 PAR advantages 26 disadvantages and limitations 26 general properties of 25 typical applications 27 parallel axis theorem 152 part geometries 212 parting line 607 angled mold 608 – – – – – – – – – – – – – – – – – – – –862 Subject Index complex mold 608 flat mold 607 local stepped mold 609 non-flat mold 608 profiled mold 608 PB advantages 97 disadvantages and limitations 97 typical applications 97 PBT advantages 33 disadvantages and limitations 34 general properties of 33 typical applications 34 PC advantages 30 disadvantages and limitations 30 general properties of 29 typical applications 30 PE general properties of 36 high density polyethylene (HDPE) 36 high molecular weight (HMW) 37 linear low density polyethylene (LLDPE) 36 low density polyethylene (LDPE) 36 PEEK advantages 28 disadvantages and limitations 28 general properties of 27 typical applications 28 PEI advantages 24 disadvantages and limitations 24 general properties of 23 typical applications 24 pendulum impact tests 753 perfluoro alkoxy alkane (PFA) 40, 41 perfluoroethylene-propylene copolymer (FEP) fluorinated 40 perfluoroethylene propylene (FEP) fluorinated 41 performance testing 723 PET advantages 35 disadvantages and limitations 36 general properties of 35 typical applications 36 PF advantages 96 – – – – – – – – – – – – – – – – – – – – – – – – – – – – – – – – – – – – disadvantages and limitations 96 general properties of 94 typical applications 96 PGT-1 gear tooth design data 296 PGT-1 helical mating gears center distance 322 PGT-1 helical mating gears strength balance 319 PGT-1 tooth design 295 PGT-1 tooth helical gear design equations 317 PGT-2 gear tooth design 297 PGT-2 tooth design for spur and helical gears 297 PGT-2 tooth helical gear design equations 317 PGT-3 gear tooth design 298 PGT-3 tooth design for spur and helical gears 298 PGT-4 gear tooth design 299 PGT-4 tooth design for spur and helical gears 299 PGT close mesh center distance between spur gears 308 gear horsepower equation basic parameters 324 gear tooth form comparison 300 helical gearing 314 helical gear specifications 334 helical pinion specifications 333 spur and helical gears horsepower rating 323 spur and helical gear specifications 328 spur gear specifications 332 spur mating gears strength balance 305 spur pinion specifications 331 phase angle 798 phenol 95 phenol formaldehyde (phenolic, PF) 94 phenol glycidyl ethers 92 phenolic 2 phthalic anhydride 85 PI advantages 102 disadvantages and limitations 102 general properties of 102 typical applications 103 – – – – – – – – – – – – – – – – – – – – – – – pin hinge conventional types 237 design snap-in 238 standard lug 238 pin point gate 660 pipe plugs 715 pipe tapped holes 715 plasticity 127 plastic range 122, 127 plastics beginning of 1 plastics selection 117 plate bending under edge boundaries 200 classification 195 compensation factor for deflection 200 edge support 197 equations 201, 202 flat circular 194 flexure stress distribution 198 simply supported, uniformly distributed load 197 simply supported, concentrated center load 198 stress analysis 195 stresses 197 under concentrated center load 199 under concentrated load 196 uniformly distributed load, fixed edge 204 uniformly distributed load, simply supported edge 204 with fixed edge 199 PLC rating 787, 788 PMMA advantages 13 disadvantages and limitations 14 general properties of generic unfilled 13 typical applications 14 Poisson’s ratio 136 poly (11-amino-undecanoic) 75 polyamide (PA, nylon) 2, 20 polyamide thermoplastic elastomer 75 polyamide TPE advantages 77 disadvantages and limitations 77 general properties of 75 typical applications 77 – – – – – – – – – – – – – – – – – – – – – – – – – – – – –Subject Index 863 polyarylate (PAR) 25 polyarylether ketone (PEAK) 27 polybutadiene (PB) 97 polybutylene terephthalate (PBT) 33 polycarbonate (PC) 28 polyester alkyd (PAK) 83 polyetheramide (PETA) 75 polyetheresteramide (PEEA) 75 polyetherether ketone (PEEK) 27 polyetherimide (PEI) 23 polyetherketone ketone (PEKK) 27 polyethylene (PE) 2, 36 polyethylene terephthalate (PET) 34 polyimide (PI) 101 polyisocyanate 104 polymer families 3 polymer melt behavior 511 polymer reinforcements 515 polymers 1 classification of 4 critical properties 514 general characteristics of 513 molecular structure of 6 polymethyl metacrylate (acrylic, PMMA) 12 polyol 104 polyolefin thermoplastic elastomer (TPO) 57, 62 polyoxyethylene glycol 75 polyoxypropylene glycol 75 polyoxytetramethylene glycol 75 polyphenols 89 polyphenylene oxide (PPO) modified 31 polyphenylene sulfide (PPS) 44 polypropylene (PP) 46, 62, 66 glycol 72 polystyrene (PS) 48 polysulfone (PSU) 49 polytetrafluoroethylene (PTFE) 39 polytetramethylene ether 72 polyurethane (PUR) 104 chemistry 58 polyvinyl chloride (PVC) 2, 51 polyvinyl fluoride (PVF) 40 polyvinylidene fluoride (PVDF) 40, 42 polyxylene 103 advantages 103 disadvantages and limitations 103 typical applications 103 POM advantages 11 – – – – – – – – – – – disadvantages and limitations 11 general properties of 9 typical applications 11 POM copolymers general properties of 9 poor surface 673 post-mold shrinkage 531, 538 post hinges insert molded 237 potassium acetate aqueous 527 power factor 798 PP advantages 47 atactic PP 46 disadvantages and limitations 47 general properties of 46 syndiotactic PP 46 typical applications 47 PPO advantages 32 disadvantages and limitations 32 general properties of 31 typical applications 32 PPS advantages 45 disadvantages and limitations 45 general properties of 44 typical applications 45 Prandtl number 621 press/lock slotted metal insert 242 press fitting 437 circular assembly 441 dimensional changes 442 interference 439 joint strength 441 metal hub and plastic shaft 440 metal shaft and plastic hub 439 shaft and hub made of different materials 439 shaft and hub made of the same material 439 pressure drop 651 pressure vessel ASME code 403 bolted end cap design 401 bursting pressure 403 cylindrical equations 399 design 393, 400 – pressure 403 – temperature 403 flat closed end, thin-walled 394 loadings 403 operating pressure 403 – – – – – – – – – – – – – – – – – – – – – – – – – – – – – – – – – – – – – – permissible over pressures 404 pressure relief devices 403 proof of design adequacy 403 regulations 402 set pressures 404 – tolerances 404 snap-fit end cap design 401 spherical closed end, thin-walled 394 stress caused by combined loads 403 tensile strength 403 testing prototype 402 testing requirements 404 thick-walled 396 thin-walled 393 processing temperatures 655 product cost 831 product design 115, 511 effects on the injection molding process 546 profit on fixed investment 845 profit on working capital 845 property materials 115, 116 property comparison 118 property data sheet 724 proportional boss geometries 548 proportional limit (PL) 126 protruding metal insert encapsulation 249 protruding screw 239 protruding shaft 239 PS advantages 48 disadvantages and limitations 49 expandable polystyrene (EPS) 48 general properties of 48 general purpose (GPPS) 48 high impact (HIPS) 48 rubber modified medium (MIPS) 48 typical applications 49 PSU advantages 50 disadvantages and limitations 50 general properties of 49 typical applications 51 PTFE advantages 42 disadvantages and limitations 43 general properties of 39 typical applications 43 pull out force 143 – – – – – – – – – – – – – – – – – – – – – – – – – – – – – – – –864 Subject Index PUR advantages 106 disadvantages and limitations 107 general properties of 104 high-density RIM systems 105 low-density flexible RIM systems 105 medium-density flexible RIM systems 105 reaction product 105 reinforced integral skin foam 106 rigid 105 – block foams 105 – integral skin foams 106 semirigid 105 thermoplastic 105 typical applications 107 PVC advantages 52 disadvantages and limitations 52 general properties of 51 typical applications 52 pyroxylin 88 Q quality control tests 119 R radial displacement 149 radius of gyration 158 reaction injection molding (RIM) 110 rectangular edge gate 656 regrinds 833 relative thermal indices 770 relaxation 139, 761 relief edge vent 678 residual stress 775 resin commodity 4 engineering 4 high performance engineering 5 intermediate 4 processing characteristics 119 resole single stage (resole) resin 95 retaining plate 611 return pins 581, 717 Reynolds number 621 rib deflection analysis 216, 217 strength analysis 215 – – – – – – – – – – – – – – – – – – – – – – – – – – stress analysis 216, 217 rib design structural reinforced or foam resins 215 structural reinforced resins 215 surface appearance 215 Rockwell hardness testing (ASTM D-785-60T) 737 rough finishing 673 round edge gate 661 runner relief edge vent 688 runner system 549 rupture 761 under long-term load 139 S SAN acrylic (ASA) 53 advantages 54 disadvantages and limitations 54 general properties of 53 olefin-modified (OSA) 53 typical applications 54 SBS advantages 62 disadvantages and limitation 62 general properties of 60 typical applications 62 screw self-tapping 432 – boss dimensions 433 – pull-out force equation 432 – stripping torque equation 432 shakeproof hi-lo – boss hole diameter 434 – thread cutting 435 – thread forming 435 thread cutting lead 431 thread forming taper lead 431 tri-lobular – boss hole size 436 – twin lead thread forming 435 screw insert tolerances 240 secant modulus 130 secondary molding operations 848 section area 150, 155 section modulus 163 SEF advantages 409 components 409 sequence of operations 409 self-tapping screws 429 – – – – – – – – – – – – – – – – – – – – – – – – – – – – – – – – self ignition temperature testing (ASTM D-1929) 805 selling price 845 shar testing apparatus 735 test specimen 735 shearing force 164 shearing strain 207 shearing stress 208 shear rate 511, 655, 783 shear strength testing (ASTM D-732) 735 short shots 672 shot size 655 shoulder bushings 582 SI advantages 108 disadvantages and limitations 108 fluids 108 typical applications 109 silicone (SI) 107 single enveloping worm gears 261 single helical gears 258 single stage (resole) resin 95 sintered vent plugs 690 skew bevel gears 260 smoke density testing (ASTM D-2843) 817 smoke generation testing 817 smooth internal sharp corners 547 snap fitting 444 cantilevered latch 447 cantilever latch 450 cantilever latch design 449 circular internal undercut depth 447 circular undercut 445 equations for cantilever beams 451 stripping circular undercut 446 soldering heat resistance 775 solvent bonding advantages 414 disadvantages 414 of ABS 414 of acrylic (PMMA) 414 of cellulosic 415 of nylon (PA) 415 of polycarbonate (PC) 415 of polystyrene (PS) 415 of polysulfone (PSU) 415 of PPO/PPE 415 of PVC 415 specific gravity testing test procedures 749 – – – – – – – – – – – – – – – – – – – – – – – – –Subject Index 865 specific gravity testing (ASTM D-792) 748 specimen conditioning 726 SPI-SPE mold steel surface finishing comparison kit 571 spider gate 659 spin welding 476 inertia process 479 joint designs 480 pivot process 477 process 480 types of processes 477 variables 477 spiral bevel gears 260 spiroid gears 262 spot welding 509 spring design 377 spring ratchet applications 385 sprue bushing 580, 641, 713 diaphragm gate 658 extension nozzle 642 gate 656 hot 643 performance alloy 642 puller 644 – pin 581 sizing 643 spur gear 258 addendum 268 – circle 268 AGMA number 268 angle of action 268 backlash 268 base circle diameter 268 base pitch 268 calculations 279 center distance 268 circular pitch 268 circular tooth thickness 268 classic designs 273 clearance 269 dedendum 269 design requirements 273 diametral pitch 269 equations 279, 280 face width 269 fillet radius 269 flank 269 gear ratio 269 interference 269 involute 269 line of action 269 number of teeth in gear 269 – – – – – – – – – – – – – – – – – – – – – – – – – – – – – – – – – – – – – – – – number of teeth in pinion 269 outside diameter 269 pitch circle 269 pitch diameter 269 pitch backlash 281 pressure angle 269 root circle 269 root diameter 269 terminology and definitions 268, 269 tooth 282 – form comparison 303 – loading 271 – stress 270 – tangential force 270 – transferred torque 270 whole depth of tooth 269 working depth of tooth 269 spur pinion and gear both with 35 teeth or more, circular tooth thickness 306 with less than 35 teeth, circular tooth thickness 305 spur pinion gear 262 spur pinion with less than 35 teeth, gear with 35 teeth or more circular tooth thicknesses 305 spur rack gear 262 SRIM processing 110 stainless steel 568 410 568 420 568 440C 568 standard mold base 582 advantages 583 disadvantages 583 standard mold tool steels 719 steel boron alloy 556 carbon spring 555 carburizing alloy 555 carburizing carbon 554 electrical 556 free machining carbon 554 H-alloy 555 hardening carbon 555 high carbon 554 high strength low alloy 555 high temperature 557 low carbon 553 low temperature alloy 556 low temperature carbon 555 medium carbon 554 nitriding 556 – – – – – – – – – – – – – – – – – – – – – – – – – – – – – – – – – – – – – – – – – stainless 556 tool 556 ultra high strength 557 used in thermoplastic injection mold components 570 steel families 553 stiffness 513 stop buttons 717 stop pins 581 straight bevel gear 259, 290, 291 HP 266 strain 125 analysis 130 stress 123, 125 compressive 133 flexural 134 working 132 stress-strain 122 behavior 121 creep 730 curve 122, 124, 125, 126 – isochronous 141 recovery (hysteresis) 138 stress-strain tension 735 stress analysis 130 stress relaxation 765 structural design 120, 211 of ribs 213 stud heads profiles and dimensions 509 styrene acrylonitrile (SAN) 53 styrenic block copolymer (SBS) 60 support pillars 581, 717 support plate 580 surface finish molded product 549 surface preparation 424 abrasion 424 chemical etching 424 corona discharge 424 degreasing cleaning 424 flame treatment 424 plasma treatment 424 surface hardness testing 736 surface resistivity testing (ASTM D-257) 794 syndiotactic PP 46 T tab edge gate 658 taber abrasion testing 741 talc 516 tangent modulus 129 – – – – – – – – – – – – – – – – – – – – – – –866 Subject Index Teflon (TFE) fabric composite bearings 373 tensile creep testing 761 elongation 727 impact testing (ASTM D-1822) 755 modulus 727 strength 123, 129 – test 726 stress 125 – effects caused by fiber glass orientation 518 test 122 tensile testing (ASTM D-638) 122, 725 crosshead speed 729 equipment 725 moisture absorption effects 729 molecular orientation 728 specimen 123, 726 temperature effects 729 tension curves 129 terephthalic acid 72 testing 723 tetraglycidylamine 90 thermal conductivity 514, 619 testing (ASTM C-177) 777 thermoplastic elastomer (TPE) 3, 55 thermoplastic hinge design co-extruded 238 thermoplastic Kevlar reinforced bearings 375 thermoplastic polyurethane elastomer (TPU) 57 thermoplastic resins 3 thermoplastics physical properties of 265 thermoset epoxies 83 families 83 melamines 83 phenolics 83 polyesters 83 polymers 4, 82 silicones 83 thread cutting 430 threaded female metal inserts 244 threaded insert tolerances 240 thread forming 430 threads ACME 226 – – – – – – – – – – – – – – – – – – – – – – – – – – – American National 226 British Association Standard 226 buttress 225 collapsible core for molding 224 creep effects 227 injection molded 224 square 226 standard forms 225 unified 226 V-threads 226 Whitworth 226 three-plate mold cold runner system 586 thrust bearing pressure equation 367 tolerances molded product 548 with finishing operations 244 without finishing operations 244 toluene diisocyanate (TDI) 104 tool steels 711 air hardening 567 air hardening SAE A2 567 air hardening SAE A4 567 air hardening SAE A6 567 air hardening SAE D2 568 air hardening SAE S7 567 carburizing 566 carburizing SAE P2 566 carburizing SAE P6 567 CPM-10V 566 effects of alloying 559, 560 – aluminum (Al) 561 – carbon (C) 560 – chromium (Cr) 561 – cobalt (Co) 562 – manganese (Mn) 561 – molybdenum (Mo) 561 – nickel (Ni) 562 – silicon (Si) 561 – tungsten (W) 562 – vanadium (V) 561 effects of heat treatment 562 flame hardening 562 for molds 712 heat treatment 563 induction hardening 563 nitriding 563 oil hardening 567 oil hardening SAE O 567 precipitation hardening 563 prehardened 564 – SAE H13 565 – SAE P20 564 – – – – – – – – – – – – – – – – – – – – – – – – – – – – – – – – – – – – – – – – – – – – – – – – SAE P21 564 properties and characteristics 559 tooth design maximum allowable outside diameter 302 top clamping plate 580 torsion equations 209 structural analysis 207 torsional springs 388 total profit 845 toughness 513 TPE advantages 55, 73 disadvantages 56 disadvantages and limitations 74 families 56 general properties of 71 typical applications 74 TPO advantages 65 disadvantages and limitations 65 general properties of 63 typical applications 65 TPU advantages 59 disadvantages and limitations 59 general properties of 57 polyester-based 58 polyether-based 58 typical applications 60 TPV advantages 68 disadvantages and limitations 68 general properties of 66 typical applications 68 triazine resins 89 tunnel gates 661 twisting moment 207 two-plate molds 584 two-stage-(novolac) resin 95 U UL 94-5VA classification (bars and plaques) 814 UL 94-5VB classification (bars and plaques) 814 UL 94-5V classification 814 UL 94 flammability testing 811 UL flammability classifications 814 UL insulation systems recognition 791 UL temperature index 770 – – – – – – – – – – – – – – – – – – – – – – – – –Subject Index 867 ultrahigh molecular weight polyethylene (UHMWPE) 38 ultrasonic insertion 500 advantages 501 configurations 501 equipment requirements 502 process guidelines 503 product design 502 ultrasonic spot welding 509 ultrasonic stud heading 506 flush head profile 508 hollow head profile 508 knurled head profile 508 multiple ultrasonic stud heading 508 rosette head profiles 508 stud profiles 506 ultrasonic stud staking 503 joint design 503 ultrasonic welding 482 amplitude of vibrations 488 basic components 483 basic principles 482 basic shear joint design with flash trap 491 chamfer shear joint 491 design limitations 494 effects caused by 497 – colorants 499 – flame retardants 498 – foaming agents 498 – impact modifiers 498 – melt flow modifiers 498 – mold release lubricants 497 – plasticizers 498 – reinforcements and fillers 499 energy director butt joint 492 energy director step joint design 493 energy director tongue and groove joint design 493 equipment 483 grades of resins 496 holding fixture 487 hold time 488 horn 486 joint designs 489 moisture absorption 495 process variables 487 reground material 495 shear joint design 489 thrust pressure 488 welding configurations 494 welding dissimilar resins 495 – – – – – – – – – – – – – – – – – – – – – – – – – – – – – – – – – – – – – – – – – – – weld time 488 undercuts 227 core pins and ejector wedge 228 external radial with angled pin slides 231 external side, using an angled pin slide 230 external side, with slides actuated hydraulically 230 offset ejector pin 229 Underwriter’s laboratories (UL) yellow cards 785 uniform wall thickness 547 UniLifter 229 unsaturated polyester (UP) 98 UP advantages 100 arthophthalic polyester resins 99 bisphenol A (BPA) fumarates 99 chlorendics 100 classifications 99 dicyclopentadiene 100 disadvantages and limitations 101 general properties of 99 isophthalic or terephthalic polyester 99 typical applications 101 urethane (TPU) 417 hybrid 109 advantages 111 disadvantages and limitations 111 typical applications 111 user’s price 845 V vapor deposits 674 vented cold runner system 713 vented ejector pins 717 vented sprue puller 714 venting 671 air poppet valve/stripper plate cavity 683 characteristics 669 cold runner 687 core and ejector pin ring groove 681 internal undercut ejection 685 mold cavity vacuum 693 parting line 675 problems 670 product design for 667 rectangular ejector blade 683 single angle pin slide mold 686 – – – – – – – – – – – – – – – – – – – – – – – – – – – – – – – sintered porous insert plugs 690 system – ejector ring 681 vertical burning testing, UL 94-5V, UL 94-5VA, UL 94-5VB 813 vertical burning testing, UL 94-V0, UL 94-V1, UL 94-V2 812 vertical insert mold 587 vibration welding 465 aligning and fixturing 473 amplitude 471 angular modes 466 butt joints 473 comparing to other assembly methods 469 equipment 471, 474 high frequency 465 joint design 472 linear methods 468 material 468 modes 466 part geometry 468 shape 468 size 468 thrust pressure on the joint interface 471 tolerances 474 vibration frequency 471 weld time 472 Vicat softening point (ASTM D-1525) 767 vinyl ester (BPA) 111 viscoelastic modulus 147 viscosity 655 volume resistivity testing (ASTM D-257) 793 W wall draft angle 213 wall thickness symmetrical 211 uniform 211 water absorption testing (ASTM D-570) 750 water testing carbon arc light 823 xenon arc light 825 wear 741 abrasive 361 adhesive 361 corrosive 361 weathering creep factors (degradation) 818 – – – – – – – – – – – – – – – – – – – – – – – – – – – – –868 Subject Index micro-organisms 820 moisture 820 oxidation 820 temperature 819 tests 818 ultraviolet (UV) radiation 819 weldability of amorphous thermoplastic resins 496 of semi-crystalline thermoplastic resins 496 of thermoplastic materials 496 – – – – – – – – – weld bead 413 weld line 541, 673 injection molding machine problems 543 molding process parameters 544 mold problems 543 product design 542 resins 542 strength 542 wollastonite 516 worm gear 261, 292 worm gear analysis 293 – – – – – – X xenon arc light (ASTM D-2565) 825 Y yield modulus 130 yield point (Y) 127 yield strength 129 Young’s modulus 121 Z zerol bevel gears 260
كلمة سر فك الضغط : books-world.net The Unzip Password : books-world.net أتمنى أن تستفيدوا من محتوى الموضوع وأن ينال إعجابكم رابط من موقع عالم الكتب لتنزيل كتاب Complete Part Design Handbook - For Injection Molding of Thermoplastics رابط مباشر لتنزيل كتاب Complete Part Design Handbook - For Injection Molding of Thermoplastics 
|
|