Admin مدير المنتدى


عدد المساهمات : 18996 التقييم : 35494 تاريخ التسجيل : 01/07/2009 الدولة : مصر العمل : مدير منتدى هندسة الإنتاج والتصميم الميكانيكى
 | موضوع: كتاب Mechanics of Mechanisms and Machines السبت 22 أغسطس 2020, 12:31 am | |
| 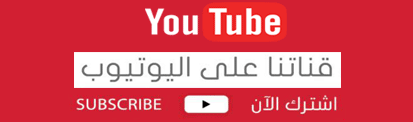
أخوانى فى الله أحضرت لكم كتاب Mechanics of Mechanisms and Machines Ilie Talpasanu and Alexandru Talpasanu
 و المحتوى كما يلي :
Contents Preface xvii Acknowledgments xix Authors . xxi 1. Background 1 1.1 Links and Links Numbering .1 1.2 Joints and Joints Labeling 1 1.3 Graph Representation of a Mechanism .4 1.3.1 Graph .4 1.3.2 Labeling of Nodes and Edges 5 1.3.3 Digraph 6 1.3.4 Paths .6 1.3.5 Open Paths 7 1.3.6 Closed Paths (Cycles) .7 1.3.7 Tree and Spanning Tree 9 1.3.8 Matrix Description of a Digraph . 11 1.3.9 Incidence Nodes–Edges Matrix, G 11 1.3.10 Reduced Incidence Nodes–Edges Matrix, G 12 1.3.11 The Path Matrix, Z . 13 1.3.12 Spanning Tree Matrix, T . 15 1.3.13 Cycle Basis Incidence Matrix, C . 15 1.3.14 Cycle Matroid Fundamentals 17 1.4 Number of Independent Cycles in a Mechanism for Planar and Spatial Mechanisms 18 1.5 Mobility of Planar Mechanisms 19 1.6 Mobility of Spatial Mechanisms . 19 References . 19 2. Kinematics of Open Cycle Mechanisms 21 2.1 Link and Joint Labeling, Frames, Home Position of Mechanism, Mechanism’s Digraph, and Mechanism’s Mobility 21 2.1.1 Link and Joint Labeling 21 2.1.2 Home Position of Mechanism 23 2.1.3 Mechanism’s Digraph .23 2.1.4 Mechanism’s Mobility . 24 2.2 Direct and Inverse Analysis: Frame Orientation and Position for the Spatial Open Cycle Mechanisms 24 2.3 Incidental and Transfer (IT) Notation 25 2.3.1 Notation for Joint Displacement Based on Incidental Digraph’s Edge .25viii Contents 2.3.2 Notation for Frames Based on Digraph’s Nodes .25 2.4 Relative Frames Orientation and Relative Rotation Matrix 26 2.4.1 Relative Rotation Matrix about x m-Axis: IT Notation .26 2.4.1.1 Relative Rotation Matrix about x m .27 2.4.2 Relative Rotation Matrix about ym-Axis: IT Notation .27 2.4.2.1 Relative Rotation Matrix about ym-Axis 28 2.4.3 Relative Rotation Matrix about z m-Axis: IT Notation .29 2.4.3.1 Relative Rotation Matrix about z m-Axis 30 2.4.4 Properties of a Relative Rotation Matrix 31 2.5 Open Cycle Mechanisms: The Relative Rotation Matrices along the Tree 32 2.5.1 Direct and Inverse Relative Rotation Matrix . 32 2.6 Additional Frames on the Same Link 33 2.7 The Absolute Rotation Matrix for Links’ Orientation .33 2.8 Direct Links’ Orientation Analysis for Open Cycle Mechanisms .34 2.8.1 Example of Direct Links’ Orientation for a Spatial Mechanism with 4 DOF 37 2.9 Inverse Links’ Orientation Analysis along a Closed Path (Cycle): The Matroid Method .44 2.9.1 Independent Equations Generated from Entries in Cycle Basis Matrix (Cycle Matroid) .45 2.9.2 The Task Orientation Matrix 46 2.9.3 Example of Inverse Orientation Analysis for an Open Cycle Spatial Mechanism with 4 DOF .47 2.9.4 Example of Inverse Orientation Analysis for an Open Cycle Spatial Mechanism with 5 DOF .48 2.9.5 Example of Inverse Orientation Analysis for an Open Cycle Spatial Mechanism with 6 DOF .50 2.10 Direct Positional Analysis: Governing Equations for Open Cycle Mechanisms 53 2.10.1 Transformation of Vector Components between Frames 53 2.10.2 Linear Displacement at Prismatic, Cylindrical, and Helical Joints .54 2.10.3 Linear Displacement at Revolute, Spherical, and Meshing Joints 54 2.10.4 Constraint Equations for Angular and Linear Displacements 55 2.10.5 Translation Vectors between Frame Origins and Position Vectors for Frame Origins along the Open Path 55 2.10.6 The End-Effector Position Vector .58 2.10.7 Equations for Direct Positional Analysis .58 2.10.8 Joint Position Matrix, r 59Contents ix 2.10.9 COM Position Vectors .59 2.10.10 Example of Direct Positional Analysis for a Spatial Mechanism with 4 DOF 59 2.10.11 Simulations for a Spatial Mechanism with 4 DOF 64 2.10.11.1 Input SW Simulation 64 2.10.11.2 Output from SW Simulation 64 2.10.11.3 Output from Engineering Equation Solver (EES) Calculation .66 2.10.12 Example of Direct Positional Analysis for a Spatial Mechanism with 5 DOF 69 2.10.13 Example of Direct Positional Analysis for a Spatial Mechanism with 6 DOF 70 2.11 Inverse Positional Analysis: Governing Equations for Open Cycle Mechanisms: The Task Position Vector .71 2.11.1 Example of Inverse Positional Analysis for a Spatial Mechanism with 4 DOF 72 2.11.2 Example of Inverse Positional Analysis for a Spatial Mechanism with 5 DOF 73 2.12 The System of Combined Equations for Inverse Orientation and Positional Analysis 73 2.13 The Matroid Method: Equations Based on Latin Matrix and Cycle Matroid Entries .75 2.13.1 The Latin Matrix 75 2.13.2 Algorithm for Automatic Generation of Latin Matrix Based on Digraph Matrices 77 2.13.3 Example of Matroid Method on Inverse Positional Analysis for a Spatial Mechanism with 4 DOF .80 2.13.3.1 Equations for Inverse Positional Analysis 81 2.13.4 Example Solution for Inverse Orientation and Positional Equations for a 4 DOF Mechanism .84 2.13.4.1 Using EES for Inverse Orientation and Positional Analysis of the TRRT 4 DOF Robotic Mechanism .84 2.13.4.2 EES for Direct Positional Analysis of the TRRT 4 DOF Robotic Mechanism 91 2.13.5 Conclusions .93 2.14 The IT Method of Relative Homogeneous Matrices: Combined Equations for Direct Orientation and Positional Analysis 93 2.14.1 Absolute Homogeneous Matrix for Link (Node Digraph), Rm 94 2.14.2 Relative IT Homogeneous Matrix for Joint (Edge Digraph), ITYZ 94 2.14.3 Relations between Absolute and Relative Homogeneous Matrices 96x Contents 2.14.4 Direct Orientation and Positional Combined Equations on Open Cycle Mechanisms 96 2.14.5 End-Effector Absolute Homogeneous Matrix .98 2.14.6 Example for Combined Equations on a 4 DOF Open Cycle Mechanism: Method of Relative Homogeneous Matrices 99 2.15 Inverse Orientation and Positional Combined Equations along a Closed Path: The Homogeneous Matrix Method . 106 2.15.1 The Direct and Inverse Sign of Relative IT Matrices 107 2.15.2 The Inverse of Homogeneous Matrix . 107 2.15.3 The Task Absolute Homogeneous Matrix 108 2.15.4 Example for Orientation and Positional Analysis of a 4 DOF Robotic Mechanism without Vision: Introduction to Robot Programming 109 2.15.5 Orientation and Positional Analysis of a Robotic Mechanism with Vision 124 2.15.6 Example for Orientation and Positional Analysis of a 4 DOF Robotic Mechanism with Vision .125 2.16 Direct Orientation and Positional Analysis for Planar Open Cycle Mechanisms 128 2.16.1 Governing Equation for Links’ Orientation for Planar Open Cycle Mechanisms . 128 2.16.2 Relations between Absolute and Relative Angular Displacements 129 2.16.3 The Path Matrix and Its Transposed, ZT . 130 2.16.4 Example of Simulation for Planar Open Cycle Manipulator with 3 DOF 131 2.16.4.1 Link and Joint Labeling . 131 2.16.4.2 Home Position of Mechanism 131 2.16.4.3 Mechanism’s Digraph for Open Cycle is a Spanning Tree . 132 2.16.4.4 Notation for Frames Based on Digraph’s Nodes . 133 2.16.4.5 Mechanism’s Mobility . 133 2.16.4.6 Constraint Equations for Angular and Linear Displacements 134 2.16.4.7 Relation between Absolute and Relative Angular Displacements . 135 2.16.4.8 The Relative and Absolute Rotation Matrices .136 2.16.5 Direct Positional Analysis: Position Vectors of Frame Origins and End-Effector 138 2.16.5.1 Position Vector Matrix . 139 2.16.5.2 End-Effector Position Vector . 139 2.16.6 Center of Mass Position Vectors . 140Contents xi 2.16.7 The Matroid Method: Equations for Inverse Orientation and Positional Analysis for Planar Open Cycle Mechanisms . 141 2.16.7.1 Equations for Inverse Orientation . 141 2.16.7.2 Equations for Inverse Positional Analysis 142 2.16.7.3 Solution of Nonlinear System of Equations . 144 2.16.8 Application for Inverse Analysis: The Required Manipulator’s Joint Displacements to Place the EndEffector E in Three Task Orientation Positions . 144 2.16.8.1 EES for Inverse Orientation and Positional Analysis of the TRT 3 DOF Manipulator 145 2.16.8.2 EES for Direct Positional Analysis of the TRT 3 DOF Manipulator 148 2.16.9 The IT Method of Relative Homogeneous Matrices: Absolute Homogeneous Matrix and Relative Homogeneous Matrix for Planar Mechanisms . 152 2.16.9.1 Absolute Homogeneous Matrix for Planar Mechanisms, Rm . 152 2.16.9.2 IT Relative Homogeneous Matrix for Planar Mechanisms, ITYZ . 152 2.16.9.3 Planar Mechanisms: Relations between Absolute and Relative Homogeneous Matrices . 153 2.16.10 Example for Orientation and Positional Analysis of a 3 DOF Planar Manipulator . 153 2.16.10.1 The Inverse of Homogeneous Matrix 158 2.17 Velocity Analysis . 159 2.17.1 Direct Angular Velocity Analysis for Open Cycle Spatial Mechanisms . 159 2.17.2 Automatic Generation of Mobile Links’ Angular Velocities from the Path Matrix . 162 2.17.3 Example of Direct Angular Velocity Analysis for Open Cycle TRRT Spatial Mechanism with 4 DOF 162 2.17.4 Example of Direct Angular Velocity Analysis for Open Cycle TRRTR Spatial Mechanism with 5 DOF . 166 2.17.5 Example of Direct Angular Velocity Analysis for Open Cycle TRRTRT Spatial Mechanism with 6 DOF . 169 2.17.6 The Matroid Method for Inverse Angular Velocity Analysis on a Closed Path 172 2.17.7 Cycle Basis Matrix (Matroid) 173 2.17.8 The Relative Angular Velocity Matrix, ? j 173 2.17.9 Inverse Angular Velocity Analysis Equations for TRRTR Spatial Mechanism 176 2.17.10 Inverse Angular Velocity Analysis Equations for TRRTRT Spatial Mechanism 178xii Contents 2.17.11 Direct Linear Velocity Analysis for Open Cycle Spatial Mechanisms 179 2.17.12 Automatic Generation of All Mobile Links’ Linear Velocities from the Path Matrix .184 2.17.13 Example of Direct Linear Velocity Analysis for Open Cycle TRRT Spatial Mechanism with 4 DOF 184 2.17.14 Inverse Linear Velocity Analysis of Open Cycle Mechanisms with Equation Functions of Absolute Angular Velocities .190 2.17.15 Example of Inverse Velocity Analysis for Open Cycle TRRT Spatial Mechanism with Equation Functions of Absolute Angular Velocities .194 2.17.16 The Inverse Linear Velocity Analysis: Governing Equation Functions of Relative Angular Velocities 196 2.17.16.1 The Spanning Tree Matrix, T 198 2.17.16.2 The Analogy to Moment of a Force and Couple from Statics .199 2.17.16.3 The Jacobean Matrix from the Combined Equations for Inverse Angular and Inverse Linear Velocities .200 2.17.16.4 Example of Inverse Velocity Analysis for Open Cycle TRRT Spatial Mechanism with Equation Functions of Relative Angular Velocities 200 2.17.17 Combined Equations for Inverse Velocity Analysis Based on Twists .203 2.17.17.1 Twists for Joints with Single and Multiple DOF 203 2.17.17.2 Geometric Jacobean Based on Twists along the Path in Tree .207 2.17.17.3 Example of Inverse Velocity Analysis for Open Cycle TRRT Spatial Mechanism with Equation Based on Twists 208 2.17.18 Example of Velocity Analysis for Planar Open Cycle Mechanisms with Equation Functions of Absolute Velocities .209 2.17.18.1 Inverse Velocity Analysis of the TRT 3 DOF Manipulator 211 2.17.18.2 Singularities for Inverse Velocity Analysis 212 2.17.19 Example of Velocity Analyses for Planar Open Cycle Mechanisms with Equation Functions of Twists 212 2.17.19.1 Capability of Motion for the TRT Manipulator .213 2.17.19.2 EES for Direct Velocity Analysis of the TRT 3 DOF Manipulator .214Contents xiii 2.18 Velocity Analysis of Planar Open Cycle Mechanisms with All Revolute Joints . 218 Problems 218 References .256 3. Kinematics of Single and Multiple Closed Cycle Mechanisms . 257 3.1 Coordinate Systems for Planar Mechanism 257 3.2 Enumeration of Planar Mechanisms Based on the Number of Cycles 258 3.2.1 Parallel Axes Gear Trains with Gear and Revolute Joints 260 3.3 Position Analysis for Single-Cycle Planar Mechanisms with Revolute Joints 262 3.3.1 The Incidence Nodes–Edges Matrix, G 264 3.3.2 The Cycle Basis Matroid Matrix, C 265 3.3.3 Joint Position Vectors Matrix, rj: .265 3.3.4 Digraph Joint Position Matrix, rc,j .266 3.3.5 Latin Matrix Method for Positional Analysis 267 3.3.6 Centers of Mass Position Vector Matrix, rGm 272 3.3.7 Center of Mass to Joint Position Matrix, LGj . 273 3.3.8 Absolute Links’ Orientation, ?n . 274 3.3.9 Relative Links’ Orientation, ?j 274 3.3.10 Relative Links’ Orientation from Digraph, ?c,j 276 3.3.11 Transmission Angle . 276 3.3.12 Input to Output Relation .277 3.3.13 Dead Centers 277 3.3.14 Coupler-Point Curves 278 3.3.15 Mechanism Branches 279 3.3.16 Grashof’s Criterion for the Four-Bar Mechanisms and Mechanism Inversions 279 3.4 Single-Cycle Planar Mechanisms with Revolute and Prismatic Joints’ Position Analysis .290 3.4.1 The Planar Crank Slider Mechanism 290 3.4.2 Example: The Planar RRTR Mechanism 304 3.5 Multiple-Cycle Planar Mechanisms with Revolute and Prismatic Joints’ Position Analysis . 318 3.6 Planar Mechanisms with Cams 327 3.6.1 Background . 327 3.6.2 Input–Output Relation 330 3.6.3 Equations for Cam Contour .335 3.6.4 Cam with Constant Velocity Rise or Constant Velocity Fall 338 3.6.5 Cam with Constant Acceleration Rise or Constant Acceleration Fall .345 3.6.6 Cam with Harmonic Motion Rise or Fall .346xiv Contents 3.6.7 Cam with Cycloidal Motion Rise or Fall 347 3.7 Velocity Analysis of Single-Cycle Planar Mechanisms .347 3.7.1 Velocity Analysis for Single-Cycle Planar Mechanisms with Revolute Joints: Example: The Four Bar Mechanism . 352 3.7.2 Velocity Analysis for Single-Cycle Planar Mechanisms with Revolute and Prismatic Joints: Example: The Crank Slider Mechanism .359 3.8 Velocity Analysis for Multiple-Cycle Planar Mechanisms with Revolute and Prismatic Joints 367 3.9 Gears . 375 3.9.1 Parallel Axes Epicyclic Gear Trains . 375 3.9.1.1 Mobility Formula for Gear Trains Based on the Number of Links and Cycles .377 3.9.1.2 Equations Based on Absolute Angular Velocities: The Matroidal Method for Gear Trains 380 3.9.1.3 Gears’ Number of Teeth 384 3.9.2 Gear Trains with the Fixed Parallel Axes (GT) 384 3.9.2.1 Equations Based on Absolute Angular Velocities: The Matroidal Method for GT . 387 3.9.2.2 GT Velocity Ratio 390 3.9.2.3 Gears’ Number of Teeth 390 3.9.3 Bevel Gear Trains . 391 3.9.3.1 Equations Based on Twists: The Matroidal Method for BGT 391 3.9.3.2 Twist Velocity Matroidal Matrix 400 3.9.3.3 Absolute Angular Velocities of Gears, Planets, and Carriers 405 3.9.3.4 Gears’ Number of Teeth 406 3.9.3.5 Automatic Generation of BGT Equations .408 Problems 409 References .441 4. Dynamic and Static Analysis of Mechanisms 443 4.1 Direct Angular Acceleration Analysis for Open Cycle Mechanisms .443 4.1.1 The Joint Relative Angular Acceleration 443 4.1.2 The Joint Axial Angular Acceleration, ?Z .444 4.1.3 Constraint Equations for Axial Angular Acceleration .444 4.1.4 The Joint Complemental Angular Acceleration, ?Z com 445 4.1.5 Links’ Absolute Angular Acceleration Matrix, ?m 446 4.2 Governing Equation for Links’ Absolute Angular Accelerations 446Contents xv 4.3 Matroid Method for Inverse Angular Acceleration Analysis on Closed Cycle Mechanisms . 452 4.3.1 Cycle Basis Matrix Assigned to Relative Angular Accelerations . 452 4.3.2 The Relative Angular Acceleration Matrix, ? j . 452 4.4 Governing Equation for Links’ Absolute Linear Accelerations 454 4.4.1 Direct Linear Acceleration Analysis for Open Cycle Spatial Mechanisms . 457 4.4.2 Example of Direct Linear Acceleration Analysis for Open Cycle TRRT Spatial Mechanism with 4 DOF 458 4.4.3 The Matroid Method for Linear Acceleration Analysis of Single- and Multiple-Cycle Planar Mechanisms 464 4.4.4 Acceleration Analysis for Single-Cycle Planar Mechanisms with Revolute Joints . 467 4.4.5 Acceleration Analysis for Multiple-Cycle Planar Mechanisms 473 4.5 Governing Equations in Dynamics of Mechanisms .484 4.5.1 The Governing Force Equations for Open Cycle Mechanisms 484 4.5.2 The Incidental and Transfer-IT Method on Dynamic Forces and Differential Equations for Open Cycle Mechanisms 486 4.5.3 The Incidence Nodes-Edges Matrix 487 4.5.4 The Reduced Incidence Nodes-Edges Matrix, G .487 4.5.5 The Path Matrix, Z .489 4.5.6 Relation for G and Z Matrices 489 4.5.7 Equations for Reaction Forces on Open Cycle Mechanisms: The IT-Resistant Force .490 4.5.8 The Evaluation of IT Forces 491 4.6 The IT Method on Dynamic Moments and Differential Equations for Open Cycle Mechanisms 492 4.6.1 Equations for Reaction Moment on Open Cycle Mechanisms: The IT-Resistant Moment . 494 4.6.2 The Position Vector Skew-Symmetric Matrix, ? G ( m a × L) and Za m × (L?) . 494 4.6.3 The Evaluation of IT Moments 497 4.6.4 Dynamic Force and Moment Reactions from Joint Constraints 498 4.6.5 Review on Computation of IT Equations for Dynamics of Open Cycle Mechanisms 505 4.7 Closed Cycle Mechanisms: The IT Method for Dynamic Forces and Differential Equations .506xvi Contents 4.7.1 The Incidence Nodes-Edges Matrix: The Reduced and Row Reduced Matrix .507 4.7.2 The Weighting Matrix, W . 511 4.7.3 The Cut-Set Matroid . 511 4.7.4 Governing Dynamic Force Equations for Closed Cycle Mechanism . 512 4.7.5 The Cut-Set Reaction Forces in Joints . 514 4.7.6 The IT-Resistant Force . 515 4.7.7 Reaction Forces in Arcs Tree Expressed from Reaction Forces in Cut-Edges . 515 4.7.8 Force Equations for Multiple-Cycle Mechanisms . 516 4.8 Closed Cycle Mechanisms: The IT Equations for Dynamic Moment Reactions and Differential Equations 517 4.8.1 The Governing Equations to Evaluate the Reactions in Cut-Joints 520 4.8.2 The Cut-Set Reaction Moment in Tree’s Joints: The Cut-Set Matroid Method . 521 4.8.3 Reaction Moment Equations for Closed Cycle Mechanisms: The Resistant Moment 521 4.8.4 Review on Computation of IT Equations for Dynamics of Closed Cycle Mechanisms 521 4.8.5 Examples of Mechanisms with Single and Multiple Cycles: Singularity Coefficient . 526 4.8.6 Example: Dynamic Reactions and Differential Equation for a Mechanism with Gears .550 4.9 Statics of Mechanisms and Machines 559 4.9.1 Background . 559 4.9.2 The Governing Equations for Closed Cycle Mechanisms 559 4.9.3 Example: Static Reactions and Break Torque Calculation for a Mechanism with Gears 560 4.10 Conclusions 565 Problems 566 References . 573 Index . 575 Index Page numbers followed by f indicate figures. A absolute acceleration, 443 absolute and relative angular displacements, 129–130, 135 absolute angular acceleration governing equation for links, 446–452 matrix, 446 absolute angular velocities bevel gear trains (BGT), 395 equations based on, 380–384 of gears, planets, and carriers, 405–406 gear trains with fixed parallel axes, 388 parallel axes epicyclic gear trains, 382 absolute homogeneous matrix for link, 94 for planar mechanisms, 152, 153 relative and, 96 absolute linear accelerations direct linear acceleration analysis example, 458–464 for open cycle spatial mechanisms, 457–464 governing equation for links, 454–484 single- and multiple-cycle planar mechanisms acceleration analysis, 467–484 matroid method, 464–466 absolute links’ orientation matrix, 274 planar crank slider mechanism, 298 versus time, 287, 288f, 299–300f, 312–313f absolute rotation matrix for links’ orientation, 33–34 for mobile links, 397 absolute velocity, 159 acceleration analysis for multiple-cycle planar mechanisms, 473–484 for single-cycle planar mechanisms with revolute joints, 457–473 acceleration matroidal matrix, 464–466 acceleration matroidal vector, 454–457 angular displacements, 55 absolute and relative, 129–130, 135 constraint equations for, 55, 134–135 arcs, 45 axial angular acceleration, 443 constraint equations for, 444–445 B bevel gear trains (BGTs), 377 absolute angular velocities of gears, planets, and carriers, 405–406 absolute angular velocity matrix, 395 automatic generation of equations, 408–409 equations based on twists, 391–400 gears’ number of teeth, 406–407 twist velocity matroidal matrix, 400–405 bottom dead center (BDC) position, 302, 304 C cam; see also planar mechanism, with cams for constant velocity follower, 441 joint, 3, 3f cam contour, equations for, 335–338 center of mass acceleration, 458 center of mass position vectors, 140–141 matrix, 272–273 center of mass to joint position matrix, 273576 Index chord, 9, 44 closed cycle mechanisms gears bevel gear trains (BGT), 391–409 gear trains with fixed parallel axes (GT), 384–391 parallel axes epicyclic gear trains (EGT), 375–384 inverse angular acceleration analysis on, 452–454 IT equations for dynamic moment reactions and differential equations, 517–558 cut-set matroid method, 521 gears, examples, 550–558 governing equations to evaluating reactions in cut-joints, 520–521 IT equations computation, 521–526 resistant moment, 521 singularity coefficient, examples, 526–550 IT method for dynamic forces and differential equations, 506–517 cut-set matroid, 511–512 cut-set reaction forces in joints, 514 force equations for multiple-cycle mechanisms, 516–517 governing dynamic force equations, 512–514 incidence nodes-edges matrix, 507–510 IT-resistant force, 515 reaction forces in arcs tree, 515–516 reduced and row reduced matrix, 507–510 weighting matrix, 511 kinematics of single and multiple, 257–441 multiple-cycle planar mechanisms with revolute and prismatic joints position analysis, 318–327 with revolute and prismatic joints velocity analysis, 367–375 planar mechanism coordinate systems for, 257–258 enumeration, 258–262 parallel axes gear trains, 260–262 planar mechanism, with cams background, 327–330 constant acceleration motion during follower’s rise/fall, 345–346 constant velocity motion during follower’s rise/fall, 338–345 cycloidal motion during follower’s rise/fall, 347 equations for cam contour, 335–338 harmonic motion during follower’s rise/fall, 346 input–output relation, 330–334 problems, 409–423 single-cycle planar mechanisms, see single-cycle planar mechanisms statics of mechanisms, governing equations for, 559–560 closed paths (cycles), 7–8, 45 complemental angular acceleration, 443, 445–446 complemental linear acceleration, 455–456 complex link, 1, 2f COM position vectors, 59 computer-aided design (CAD) drawings, 46 constant acceleration motion during follower’s rise/fall, 345–346 constant velocity motion during follower’s rise/fall, 338–345 Coriolis acceleration, 456, 465 coupler-point curves, 278–279, 290f crank-rocker mechanism coordinates for joints for, 431, 434 versus Latin matrix, 430 mobile links’ orientation in time, 432 crank slider mechanism, 359–367, 361f frames for, 257, 258f versus Latin matrix, 433 links’ orientation angles for, 436 mobile links’ orientation in time, 435 cut-joints governing equations to evaluating reactions in, 520–521 cut-set matroid method, 511–512, 521 cut-set reaction forces, in joints, 514Index 577 cycle base matroid, 350 for bevel gear trains (BGT), 391 cycle basis matrix assigned to relative angular accelerations, 452 incidence matrix (C), 15–17 independent equations generated from entries in, 45–46 cycle basis matroid matrix, 78, 173, 265, 332 bevel gear trains (BGT), 394–395 planar crank slider mechanism, 292–293 planar RRTR mechanism, 307 two-cycle planar mechanism, 477 cycle matroid, 45–46 fundamentals, 17–18 cycles, 44, 106 closed paths, 7–8, 45 cycloidal motion, during follower’s rise/ fall, 347 cylinder–plane joint, 3f, 4 D dead center position, 277, 278f planar crank slider mechanism, 302 planar RRTR mechanism, 314 differential equation of motion from actuating forces, 504 from actuating torques, 505 digraph, 6, 6f bevel gear trains (BGT), 391 cut-sets, 512 epicyclic gear trains (EGT), 375 gear trains with fixed parallel axes (GT), 386 joint position matrix, 266–267 matrix description of, 11 open cycle mechanism’s, 23–24 planar crank slider mechanism, 292 planar RRTR mechanism, 306 relative links’ orientation matrix from, 276 direct analysis orientation and positional analysis of mechanisms, 24 direct and inverse relative rotation matrix, 32 direct and inverse sign of relative IT matrices, 107 direct angular acceleration analysis joint axial angular acceleration, 444 constraint equations for, 444–445 joint complemental angular acceleration, 445–446 joint relative angular acceleration, 443 links’ absolute angular acceleration matrix, 446 for open cycle mechanisms, 443–446 direct angular velocity analysis for open cycle spatial mechanisms, 159–161 example with DOFs, 162–172 directional angles, 27 directional cosines, 27 direct linear acceleration analysis for open cycle spatial mechanisms, 457–464 example, 458–464 direct linear velocity analysis for open cycle spatial mechanisms, 179–184 example with DOF, 184–190 direct orientation analysis example for spatial mechanism with 4 DOF, 37–44 governing equations for, 36, 42–43 for open cycle mechanisms, 34–44 direct positional analysis COM position vectors, 59 end-effector position vector, 58 equations for, 58 examples for spatial mechanism with 4 DOF, 59–69 with 5 DOF, 69–70 with 6 DOF, 70–71 governing equations for open cycle mechanisms, 53–71 joint position matrix, r, 59 linear displacements constraint equations, 55 at joints, 54 translation vectors between frame origins, 55–58 vector components transformation between frames, 53–54578 Index disjoint internal regions, 7, 7f dynamics of mechanisms evaluation of IT forces, 491–492 governing equations in, 484–492 incidence nodes-edges matrix, 487 IT-resistant force, 490–491 open cycle mechanisms governing force equations for, 484–485 incidental and transfer-IT method for, 486–487 path matrix, 489–490 reduced incidence nodes-edges matrix, 487–488, 489–490 E edge digraph (ITYZ) relative IT homogeneous matrix for joint, 94–96 edge/node labeling, 5 end-effector absolute homogeneous matrix, 98–99 end-effector coordinates from EES and SW, 248, 255 for TRRT spatial mechanism, 245 for TRT planar manipulator, 247 end-effector frame’s orientation, 35, 36, 38–39f end-effector linear acceleration, 463, 464f end-effector position vector, 58, 62, 139–140 for home position, 63 end-effector velocity components for TRRT mechanism, 191f Engineering Equation Solver (EES) calculation for direct positional analysis, 91–93, 148–152 for direct velocity analysis, 253 for inverse orientation and positional analysis, 84–91, 145–148 parametric table, 246–247, 249–252, 254 for planar mechanisms, 284 simulations, 66–69 epicyclic gear trains (EGT), see parallel axes epicyclic gear trains (EGT) Euler angles, 37 Euler formula, 8, 19 external region, 8, 8f F fictitious equilibrium, 497 fictitious joint, 44 force equations, 560 four-bar mechanism, 352–359, 353f frame for, 257, 258f four-cycle IT dynamic equations, 525–526 frame orientation and position, for spatial open cycle mechanisms, 24–25 incidence nodes–edges matrix, 11–12 reduced incidence nodes–edges matrix, 12–13 G gear joint, 3, 3f gear ratios bevel gear trains, 402 gear trains with fixed parallel axes, 389 matroidal method for gear trains, 382–383 gears bevel gear trains (BGTs) absolute angular velocities of gears, planets, and carriers, 405–406 automatic generation of equations, 408–409 equations based on twists, 391–400 gears’ number of teeth, 406–407 twist velocity matroidal matrix, 400–405 dynamic reactions and differential equation, example, 550–558 gear trains with fixed parallel axes (GT), 384–391 equations based on absolute angular velocities, 387–389 gears’ number of teeth, 390–391 velocity ratio, 390Index 579 parallel axes epicyclic gear trains, 375–384 equations based on absolute angular velocities, 380–384 gears’ number of teeth, 384 mobility formula, 377–380 static reactions and break torque calculation, example, 560–565 gear trains with fixed parallel axes (GT), 384–391 equations based on absolute angular velocities, 387–389 gears’ number of teeth, 390–391 GT velocity ratio, 390 geometric Jacobian for angular velocities, 174 graph theory, 4–5 Grashof’s criterion, 279–290 Gruebler formula, 19 GT velocity ratio, 390 H harmonic motion, during follower’s rise/fall, 346 Hartemberg and Denavit (HD) notation, 95 home position with cam, 329 direction angles at, 43–44 joint position matrix for, 63 of mechanism, 23, 23f, 131–132 planar crank slider mechanism, 294 state, homogeneous matrix method, 110–113, 111f homogeneous matrix method direct and inverse sign of relative IT matrices, 107 home-position state, 110–113, 111f inverse of, 107–108 inverse orientation and positional combined equations along closed path, 106–128 IT relative homogeneous matrices, 93–106 for planar mechanisms, 152–153 orientation and positional analysis of robotic mechanism without vision, 109–123 of robotic mechanism with vision, 124–128 part-approach state, 113–115, 113f part-grasped state, 115–117, 115f robot programming, 109–123 target-approach state, 117–120, 118f target-reached state, 120–123, 121f task absolute homogeneous matrix, 108–109 I incidence links–joints matrix, 78, 332 planar crank slider mechanism, 292 planar RRTR mechanism, 306 incidence matrix, partitions of, 513 incidence nodes–edges matrix, 11–12, 264, 391–394, 487, 507–510 incidental and transfer (IT) notation on dynamic moments and differential equations for closed cycle mechanisms, 506–517 for open cycle mechanisms, 492–506 forces, evaluation of, 491–492, 497–498 for frames based on digraph’s nodes, 25 for joint displacement based on incidental digraph’s edge, 25 moments, evaluation of, 497–498 for open cycle mechanisms, 486–487 relative homogeneous matrices, 93–106 for planar mechanisms, 152–153 relative rotation matrix about x m-axis, 26–27, 241 about ym-axis, 27–29, 242 about z m-axis, 29–31, 242 -resistant force, 490–491, 494, 515 incidental matrix, 95 independent cycles, 9–10, 10f for planar and spatial mechanisms, 18–19 inertial frame, 257 input joint rates and output end-effector linear and angular velocities for TRT manipulator, 254580 Index input–output relation planar crank slider mechanism, 301 planar mechanism with cams, 330–334 planar RRTR mechanism, 314 single-cycle planar mechanisms, 277, 289f input parameters, 36 inverse analysis application for, 144–152 orientation and positional analysis of mechanisms, 24 inverse angular velocity analysis equations for TRRTR spatial mechanism, 176–177 for TRRTRT spatial mechanism, 178–179 twists example, 208–209 geometric Jacobean, 207–208 for joints with single and multiple DOF, 203–207 inverse linear velocity analysis, of open cycle mechanisms with equation functions of absolute angular velocities, 190–194 example, 194–196 with equation functions of relative angular velocities, 196–201 analogy to moment of force and static couples, 199–200 example, 200–203 Jacobean matrix from combined equations, 200 redundant and nonredundant system, 203 spanning tree matrix, 198–199 twists example, 208–209 geometric Jacobean, 207–208 for joints with single and multiple DOF, 203–207 inverse links’ orientation analysis along closed path (cycle), 44–53 example for spatial mechanism with 4 DOF, 47–48 with 5 DOF, 48–50 with 6 DOF, 50–53 independent equations, 45–46 task orientation matrix, 46–47 inverse of homogeneous matrix, 107–108 inverse of relative matrix, 32 inverse positional analysis equations for, 81–84 examples for spatial mechanism with 4 DOF, 72, 73–74, 80–84 with 5 DOF, 73, 74–75 governing equations for open cycle mechanisms, 71–73 J Jacobean matrix, for inverse angular and inverse linear velocities, 200 joint axial angular acceleration, 444 constraint equations for, 444–445 joint complemental angular acceleration, 445–446 joint coordinates, 64 joint linear accelerations, 457–458, 466 joint position matrix, 59, 60–62 for home position, 63 planar crank slider mechanism, 297 planar RRTR mechanism, 311 vectors matrix, 265–266 joint relative angular acceleration, 443 joints and labeling, 1–4 relative constraints matrix, 76 twists for, 203–227 K kinematics of closed cycle mechanisms, see closed cycle mechanisms of open cycle mechanisms, see open cycle mechanisms Kirchhoff’s Matrix Tree Theorem, 12 Kutzbach formula, 19, 507 L Latin matrix, 75–77 algorithm for automatic generation of, 77–79Index 581 cam–follower mechanism, 333 entries for crank-rocker mechanism, 430 entries for TRT manipulator, 251 entries versus time for crank slider mechanism, 433 entries versus time for RRTR planar mechanism, 437 equations for columns, 143–144 equations for rows, 143 gear trains with fixed parallel axes, 387 method for positional analysis, 267–272 parallel axes epicyclic gear trains, 380 planar RRTR mechanism, 307 two-cycle planar mechanism, 477 vector components for, 293 and velocity matroidal matrix, 348–350 Latin velocity vector, 180 between frame origins along closed path, 192f linear displacements constraint equations for, 55, 134–135 at joints, 54 link(s) constraints matrix, 76 and joint labeling, 21–22 and numbering, 1 link and joint numbering bevel gear trains (BGT), 391 epicyclic gear trains (EGT), 375 gear trains with fixed parallel axes (GT), 386 M matroid method for bevel gear trains (BGT), 391–400 cut-set reaction moment in tree’s joints, 521 cycle basis matrix, 173 example on inverse positional analysis equations, 81–84 for spatial mechanism with 4 DOF, 80–84 example solution for inverse orientation and positional equations for 4 DOF mechanism, 84–92 for gear trains, 380–384 with fixed parallel axes, 387–389 for inverse angular acceleration analysis on closed cycle mechanisms, 452–454 cycle basis matrix, 452 relative angular acceleration matrix, 453–454 for inverse angular velocity analysis on closed path, 172 inverse links’ orientation analysis along closed path, 44–53 Latin matrix, 75–77 algorithm, 77–79 for linear acceleration analysis of single- and multiple-cycle planar mechanisms, 464–466 for planar open cycle mechanisms equations for inverse orientation, 141–142 equations for inverse positional analysis, 142–144 equations for Latin matrix, 143–144 solution of nonlinear system of equations, 144 for velocity equations of mechanisms with cycles, 350–351 matroids, 17–18 mechanism absolute rotation matrix, 35, 36, 41–42 mechanism branches, 279 mechanism, graph representation of; see also specific entries closed paths (cycles), 7–8 cycle basis incidence matrix, C, 15–17 cycle matroid fundamentals, 17–18 digraph, 6 matrix description of, 11 graph, 4–5 incidence nodes–edges matrix, G, 11–12 labeling of nodes and edges, 5 open paths, 7582 Index mechanism, graph representation of (cont.) path matrix, Z, 13–14 paths, 6–7 reduced incidence nodes–edges matrix, G, 12–13 spanning tree matrix, T, 15 tree and spanning tree, 9–10 meshing joint, 54 mobility formula for epicyclic gear trains (EGT), 377–380 gear trains with fixed parallel axes (GT), 386 planar crank slider mechanism, 292 of planar mechanism, 19, 133–134 planar RRTR mechanism, 306 of spatial mechanisms, 19, 24 moment equations, 560 motion differential equations of, 535–550 joint and link constraints for, 210 multiple-cycle mechanisms force equations for, 516–517 multiple-cycle planar mechanisms acceleration analysis for, 473–484 with revolute and prismatic joints position analysis, 318–327 with revolute and prismatic joints velocity analysis, 367–375 multiple joined links, 4, 4f N node digraph (Rm) absolute homogeneous matrix for link, 94 node/edge labeling, 5 nonlinear system of equations for positional analysis, 269–272 planar crank slider mechanism, 294 planar RRTR mechanism, 308 null rotation, 32 O open cycle mechanisms absolute rotation matrix for links’ orientation, 33–34 additional frames on same link, 33 direct and inverse analysis, 24–25 direct angular acceleration analysis joint axial angular acceleration, 444–445 joint complemental angular acceleration, 445–446 joint relative angular acceleration, 443 links’ absolute angular acceleration matrix, 446 direct links’ orientation analysis for, 34–44 direct positional analysis COM position vectors, 59 end-effector position vector, 58 equations for, 58 examples for spatial mechanism, 59–71 joint position matrix, r, 59 linear displacements, 54–55 translation vectors between frame origins, 55–58 vector components transformation between frames, 53–54 equations based on Latin matrix and cycle matroid entries, 75–93 equations for inverse orientation and positional analysis, 73–75 governing force equations for, 484–485 home position of mechanism, 23, 23f homogeneous matrix method direct and inverse sign of relative IT matrices, 107 home-position state, 110–113, 111f inverse of, 107–108 inverse orientation and positional combined equations along closed path, 106–128 orientation and positional analysis, examples, 109–128 part-approach state, 113–115, 113f part-grasped state, 115–117, 115f robot programming, 109–123 target-approach state, 117–120, 118f target-reached state, 120–123, 121f task absolute homogeneous matrix, 108–109Index 583 inverse links’ orientation analysis along closed path (cycle), 44–53 example for spatial mechanism, 47–53 independent equations, 45–46 task orientation matrix, 46–47 inverse positional analysis equations for, 81–84 examples for spatial mechanism, 72–75, 80–84 governing equations for, 71–73 IT method for, 25, 492–506 dynamic force and moment reactions from joint constraints, 498–505 on dynamic forces and differential equations for, 486–487 equations for reaction moment, 494 IT equations computation, 505–506 IT moments evaluation, 497–498 position vector skew-symmetric matrix, 494–497 relative homogeneous matrices, 93–106 kinematics of, 21–255 Latin matrix, 75–79 link and joint labeling, 21–22 Matroid method, 44–53 mechanism’s digraph, 23–24 mobility, 24 planar open cycle mechanisms absolute and relative angular displacements, 129–130 absolute homogeneous matrix, 152, 153 application for inverse analysis, 144–152 center of mass position vectors, 140–141 direct orientation and positional analysis for, 128–158 direct positional analysis, 138–140 end-effector position vector, 139–140 example for orientation and positional analysis, 153–158 example of simulation with 3 DOF, 131–138 governing equation for links’ orientation for, 128–129 IT relative homogeneous matrix, 152–153 matroid method, 141–144 path matrix and its transposed matrix, 130 position vector matrix, 139 relative homogeneous matrices, 152–153 problems, 218–241 reaction forces equations on, 490–491 relative homogeneous matrices, IT method of, 93–106 relative rotation matrix relative frames orientation, 26–32 along tree, 32–33 spatial TRRT mechanism, 21, 22f velocity analysis, see velocity analysis open paths, 7 orthogonality between cycle base matroid and cutset matroid, 512 orthonormal matrix (D), 31 P parallel axes epicyclic gear trains (EGT), 375–384 absolute angular velocity matrix, 378 classification, 427–429 gears and carrier absolute rotation matrices, 379 gears’ number of teeth, 384 matroidal method for gear trains, 380–384 mobility formula for, 377–380 relative angular velocity matrix, 378 relative rotation matrices, 379 unit vectors for axes of rotation, 380 part-approach position, 64, 88, 89f part-grasped position, 64, 88–89, 90f path matrix (Z), 13–14, 509 automatic generation of mobile links’ angular velocities from, 162, 184584 Index path matrix (Z) (cont.) bevel gear trains (BGT), 394 dynamics of mechanisms, 489 and its transposed matrix, 130 and reduced incidence nodes-edges matrix, 489–490 paths, 6–7, 24, 24f peripheral cycle, 8, 8f planar mechanisms with cams, 327–347 background, 327–330 constant acceleration motion during follower’s rise/fall, 345–346 constant velocity motion during follower’s rise/fall, 338–345 cycloidal motion during follower’s rise/fall, 347 equations for cam contour, 335–338 harmonic motion during follower’s rise/fall, 346 input–output relation, 330–334 classification, 424–426 coordinate systems for, 257–258 crank slider mechanism, 290–304 enumeration, based on number of cycles, 258–262, 259f parallel axes gear trains, 260–262 independent cycles in mechanism for, 18–19 mobility of, 19 planar RRTR mechanism coordinates for joints for, 438 example, 304–318 versus Latin matrix, 437 links’ orientation angles for, 439 planar open cycle mechanisms absolute and relative angular displacements, 129–130 application for inverse analysis, 144–152 EES for direct positional analysis, 148–152, 247–252 EES for inverse orientation and positional analysis, 145–148 center of mass position vectors, 140–141 direct positional analysis, 138–140 end-effector position vector, 139–140 position vector matrix, 139 example for orientation and positional analysis of 3 DOF planar manipulator, 153–158 inverse of homogeneous matrix, 158 example of simulation with 3 DOF absolute and relative angular displacements, 135 constraint equations for angular and linear displacements, 134–135 home position of mechanism, 131–132 link and joint labeling, 131 mechanism’s digraph, 132–133 mechanism’s mobility, 133–134 notation for frames based on digraph’s nodes, 133 relative and absolute rotation matrices, 136–138 governing equation for links’ orientation for, 128–129 matroid method equations for inverse orientation, 141–142 equations for inverse positional analysis, 142–144 solution of nonlinear system of equations, 144 path matrix and its transposed matrix, 130 relative homogeneous matrices absolute homogeneous matrix, 152, 153 IT relative homogeneous matrix, 152–153 plane–plane joint, 3, 3f Plucker coordinates, 398 positional analysis; see also single-cycle planar mechanisms Latin matrix method for, 267–272 nonlinear system of equations for, 269–272 positional constraints, 210–211 position vectors, 55–58, 57fIndex 585 matrix, 139 skew-symmetric matrix, 494–497 prismatic joint, 2, 3f R reaction forces, in arcs tree, 515–516 reaction moment equations on closed cycle mechanisms, 521 equations on open cycle mechanisms, 494 from joint constraints, 498–505 reduced and row reduced matrix, 507–510 reduced incidence nodes-edges matrix, 487–488 reduced matrix, partitions of, 509 redundant and nonredundant system, 201 reference axis, 26, 28 relative acceleration, 443 relative angular acceleration, 443, 453–454 cycle basis matrix assigned to, 452 relative angular velocity, 159 matrix, 173–176, 395–396 relative homogeneous matrices direct orientation and positional combined equations example on 4 DOF, 99–106 on open cycle mechanisms, 96–98 edge digraph, 94–96 end-effector absolute homogeneous matrix, 98–99 IT method of, 93–106 node digraph, 94, 96 for planar mechanisms, 152–153 relative linear acceleration, 456 relative links’ orientation matrix, 274–275 from digraph, 276 planar crank slider mechanism, 299 relative matrix, inverse of, 32 relative rotation matrix bevel gear trains (BGT), 396–397 direct and inverse, 32 properties of, 31–32, 243–244 along tree, 32–33 about x m-axis, 26–27, 241 about ym-axis, 27–29, 242 about z m-axis, 29–31, 242 relative velocity, 159 resistant moment, 521 revolute joint, 2, 3f, 54 rotation; see also relative rotation matrix about x m-axis, 241 about ym-axis, 242 about z m-axis, 242 row-reduced incidence matrix, 510 S scaling factor, 94 screw joint, 2, 3f screws at joints, 397–398 screw’s lead, 2, 3f simple link, 1, 2f single-cycle IT dynamic moment equations, 523, 527–532 solution for, 533 single-cycle planar mechanisms acceleration analysis for, 467–473 with revolute and prismatic joints example, planar RRTR mechanism, 304–318 planar crank slider mechanism, 290–304 with revolute joints absolute links’ orientation, 274 center of mass to joint position matrix, 273 centers of mass position vector matrix, 272–273 coupler-point curves, 278–279 cycle basis matroid matrix, 265 dead centers, 277–278 digraph joint position matrix, 266–267 Grashof’s criterion, 279–290 incidence nodes–edges matrix, 264 input to output relation, 277 joint position vectors matrix, 265–266 Latin matrix method, 267–272 mechanism branches, 279 position analysis for, 262–290586 Index single-cycle IT dynamic moment equations (cont.) relative links’ orientation, 274–276 transmission angle, 276–277 velocity analysis for, 347–367 with revolute and prismatic joints, 359–367 with revolute joints, 352–359 singularities for inverse velocity analysis, 212 singularity coefficient examples of mechanisms with single and multiple cycles, 526–550 skew-symmetric matrices, 494, 496, 518 sliding pair, 2, 3f SolidWorks (SW) motion simulation, 64–69 end-effector’s path from, 151f spanning tree, 9–10, 24f bevel gear trains (BGT), 391, 394 epicyclic gear trains (EGT), 375 gear trains with fixed parallel axes (GT), 386 matrix (T), 15, 198–199 planar crank slider mechanism, 292 planar RRTR mechanism, 306 spatial mechanisms independent cycles for, 18–19 mobility of, 19 TRRT, 21–22 sphere–plane joint, 3f, 4 spherical joint, 3, 3f springs, 1 states of the joint coordinates, 109 statics of mechanisms and machines background, 559 example, 560–565 governing equations for closed cycle mechanisms, 559–560 T target-approach position, 64, 89, 90f target-reached position, 64, 91, 91f task absolute homogeneous matrix, 108–109 task orientation matrix, 46–47 task position vector, 71–73 task velocity vector, 193 teaching-by-doing approach, 109 three-cycle mechanisms force equations for, 516–517 IT dynamic equations, 524–525 top dead center (TDC) position, 302, 303–304 translation matrix, 95 translation vectors, 55–58 transmission angle for four-bar mechanism, 276–277, 289f planar crank slider mechanism, 301 planar RRTR mechanism, 313 transpose matrix, 14 tree, 9–10 turning pair, 2, 3f twists combined equations for inverse velocity analysis on for cylindrical joint, 207 for prismatic joint, 206 for revolute joint, 203–205 for screw joint, 207 for spherical joint, 206–207 example of velocity analyses capability of motion for TRT manipulator, 213–214 EES for direct velocity analysis of TRT 3 DOF manipulator, 214–218 for planar open cycle mechanisms, 212–218 matroidal method for BGT, 391–400 velocity matroidal matrix, 400–405 two-cycle mechanisms force equations for, 516–517 IT dynamic equations, 523–524 planar mechanism acceleration analysis for, 473–484 links’ orientation and slider displacement for, 440 U unit screw lower vector w.r.t. meshing joint, 399–400 upper vector w.r.t. fixed frame, 398 unit vectors for axes of rotationIndex 587 bevel gear trains (BGT), 397 epicyclic gear trains (EGT), 380 gear trains with fixed parallel axes (GT), 380, 386 V vector components, transformation between frames, 53–54 velocity analysis automatic generation of mobile links’ angular velocities, 162, 184 direct angular velocity analysis example with DOFs, 162–172 for open cycle spatial mechanisms, 159–161 direct linear velocity analysis example with DOF, 184–190 for open cycle spatial mechanisms, 179–184 example for planar open cycle mechanisms with equation functions of absolute velocities, 209–212 with equation functions of twists, 212–218 inverse angular velocity analysis equations for TRRTR spatial mechanism, 176–177 for TRRTRT spatial mechanism, 178–179 inverse linear velocity analysis, of open cycle mechanisms with equation functions of absolute angular velocities, 190–196 with equation functions of relative angular velocities, 196–203 matroid method cycle basis matrix, 173 for inverse angular velocity analysis, 172 for multiple-cycle planar mechanisms with revolute and prismatic joints, 367–375 of planar open cycle mechanisms with revolute joints, 218 relative angular velocity matrix, 173–176 of single-cycle planar mechanisms, 347–367 with revolute and prismatic joints, 359–367 with revolute joints, 352–359 twists, combined equations for inverse velocity analysis on example for open cycle TRRT spatial mechanism, 208–209 geometric Jacobean, 207–208 for joints with single and multiple DOF, 203–207 velocity matroidal matrix, 400–401 gear trains with fixed parallel axes, 387–388 Latin matrix and, 348–350 parallel axes epicyclic gear trains, 381 W weighting matrix, 511 world frame, 257 Y yaw–pitch–roll angles, 37 Z zero-pitch screw, 205
كلمة سر فك الضغط : books-world.net The Unzip Password : books-world.net أتمنى أن تستفيدوا من محتوى الموضوع وأن ينال إعجابكم رابط من موقع عالم الكتب لتنزيل كتاب Mechanics of Mechanisms and Machines رابط مباشر لتنزيل كتاب Mechanics of Mechanisms and Machines 
|
|