Admin مدير المنتدى


عدد المساهمات : 18996 التقييم : 35494 تاريخ التسجيل : 01/07/2009 الدولة : مصر العمل : مدير منتدى هندسة الإنتاج والتصميم الميكانيكى
 | موضوع: كتاب Fundamentals of Machine Component Design - Seventh Edition الخميس 18 أغسطس 2022, 12:10 am | |
| 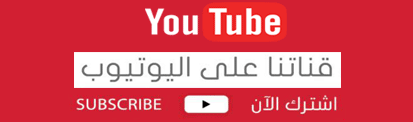
أخواني في الله أحضرت لكم كتاب Fundamentals of Machine Component Design - Seventh Edition Robert C. Juvinall Professor of Mechanical Engineering University of Michigan Kurt M. Marshek Professor of Mechanical Engineering University of Texas at Austin
 و المحتوى كما يلي :
CONTENTS Content available in eBook Student solution available in interactive e-text Preface v Acknowledgments ix Symbols xix P A R T 1 FUNDAMENTALS 1 1 Mechanical Engineering Design in Broad Perspective 1 1.1 An Overview of the Subject 1 1.2 Safety Considerations 2 1.3 Ecological Considerations 7 1.4 Societal Considerations 8 1.5 Overall Design Considerations 10 1.6 Systems of Units 12 1.7 Methodology for Solving Machine Component Problems 14 1.8 Work and Energy 16 1.9 Power 18 1.10 Conservation of Energy 19 2 Load Analysis 24 2.1 Introduction 24 2.2 Equilibrium Equations and Free-Body Diagrams 24 2.3 Beam Loading 34 2.4 Locating Critical Sections—Force Flow Concept 37 2.5 Load Division Between Redundant Supports 39 2.6 Force Flow Concept Applied to Redundant Ductile Structures 41 3 Materials 45 3.1 Introduction 45 3.2 The Static Tensile Test—“Engineering” Stress–Strain Relationships 46 3.3 Implications of the “Engineering” Stress–Strain Curve 47 3.4 The Static Tensile Test—“True” Stress–Strain Relationships 50 3.5 Energy-Absorbing Capacity 51 3.6 Estimating Strength Properties from Penetration Hardness Tests 52 3.7 Use of “Handbook” Data for Material Strength Properties 55 3.8 Machinability 56 3.9 Cast Iron 56 3.10 Steel 57 3.11 Nonferrous Alloys 59 3.12 Plastics and Composites 61 xixii Contents 3.13 Materials Selection Charts 66 3.14 Engineering Material Selection Process 68 4 Static Body Stresses 77 4.1 Introduction 77 4.2 Axial Loading 77 4.3 Direct Shear Loading 79 4.4 Torsional Loading 80 4.5 Pure Bending Loading, Straight Beams 82 4.6 Pure Bending Loading, Curved Beams 83 4.7 Transverse Shear Loading in Beams 88 4.8 Induced Stresses, Mohr Circle Representation 94 4.9 Combined Stresses—Mohr Circle Representation 96 4.10 Stress Equations Related to Mohr’s Circle 99 4.11 Three-Dimensional Stresses 100 4.12 Stress Concentration Factors, Kt 104 4.13 Importance of Stress Concentration 107 4.14 Residual Stresses Caused by Yielding—Axial Loading 109 4.15 Residual Stresses Caused by Yielding—Bending and Torsional Loading 113 4.16 Thermal Stresses 115 4.17 Importance of Residual Stresses 117 5 Elastic Strain, Deflection, and Stability 119 5.1 Introduction 119 5.2 Strain Definition, Measurement, and Mohr Circle Representation 120 5.3 Analysis of Strain—Equiangular Rosettes 122 5.4 Analysis of Strain—Rectangular Rosettes 124 5.5 Elastic Stress–Strain Relationships and Three-Dimensional Mohr Circles 126 5.6 Deflection and Spring Rate—Simple Cases 128 5.7 Beam Deflection 130 5.8 Determining Elastic Deflections by Castigliano’s Method 133 5.9 Redundant Reactions by Castigliano’s Method 144 5.10 Euler Column Buckling—Elastic Instability 148 5.11 Equivalent Column Length for Various End Conditions 150 5.12 Column Design Equations—J. B. Johnson Parabola 151 5.13 Eccentric Column Loading—the Secant Formula 155 5.14 Equivalent Column Stresses 156 5.15 Other Types of Buckling 157 5.16 Finite Element Analysis 158 6 Failure Theories, Safety Factors, and Reliability 161 6.1 Introduction 161 6.2 Types of Failure 163 6.3 Fracture Mechanics—Basic Concepts 164 6.4 Fracture Mechanics—Applications 165 6.5 The “Theory” of Static Failure Theories 174 6.6 Maximum-Normal-Stress Theory 176 6.7 Maximum-Shear-Stress Theory 176 6.8 Maximum-Distortion-Energy Theory (Maximum-Octahedral-Shear-Stress Theory) 177 6.9 Mohr Theory and Modified Mohr Theory 179 6.10 Selection and Use of Failure Theories 180 6.11 Safety Factors—Concept and Definition 182 6.12 Safety Factors—Selection of a Numerical Value 184Contents xiii 6.13 Reliability 186 6.14 Normal Distributions 187 6.15 Interference Theory of Reliability Prediction 188 7 Impact 192 7.1 Introduction 192 7.2 Stress and Deflection Caused by Linear and Bending Impact 194 7.3 Stress and Deflection Caused by Torsional Impact 201 7.4 Effect of Stress Raisers on Impact Strength 204 8 Fatigue 210 8.1 Introduction 210 8.2 Basic Concepts 210 8.3 Standard Fatigue Strengths (Sn′ ) for Rotating Bending 212 8.4 Fatigue Strengths for Reversed Bending and Reversed Axial Loading 217 8.5 Fatigue Strength for Reversed Torsional Loading 218 8.6 Fatigue Strength for Reversed Biaxial Loading 219 8.7 Influence of Surface and Size on Fatigue Strength 220 8.8 Summary of Estimated Fatigue Strengths for Completely Reversed Loading 222 8.9 Effect of Mean Stress on Fatigue Strength 222 8.10 Effect of Stress Concentration with Completely Reversed Fatigue Loading 231 8.11 Effect of Stress Concentration with Mean Plus Alternating Loads 233 8.12 Fatigue Life Prediction with Randomly Varying Loads 240 8.13 Effect of Surface Treatments on the Fatigue Strength of a Part 243 8.14 Mechanical Surface Treatments—Shot Peening and Others 245 8.15 Thermal and Chemical Surface-Hardening Treatments (Induction Hardening, Carburizing, and Others) 246 8.16 Fatigue Crack Growth 246 8.17 General Approach for Fatigue Design 250 9 Surface Damage 255 9.1 Introduction 255 9.2 Corrosion: Fundamentals 255 9.3 Corrosion: Electrode and Electrolyte Heterogeneity 258 9.4 Design for Corrosion Control 259 9.5 Corrosion Plus Static Stress 262 9.6 Corrosion Plus Cyclic Stress 264 9.7 Cavitation Damage 264 9.8 Types of Wear 265 9.9 Adhesive Wear 265 9.10 Abrasive Wear 267 9.11 Fretting 268 9.12 Analytical Approach to Wear 269 9.13 Curved-Surface Contact Stresses 272 9.14 Surface Fatigue Failures 278 9.15 Closure 279 P A R T 2 APPLICATIONS 282 10 Threaded Fasteners and Power Screws 282 10.1 Introduction 282 10.2 Thread Forms, Terminology, and Standards 282xiv Contents 10.3 Power Screws 286 10.4 Static Screw Stresses 295 10.5 Threaded Fastener Types 299 10.6 Fastener Materials and Methods of Manufacture 301 10.7 Bolt Tightening and Initial Tension 301 10.8 Thread Loosening and Thread Locking 305 10.9 Bolt Tension with External Joint-Separating Force 308 10.10 Bolt (or Screw) Selection for Static Loading 312 10.11 Bolt (or Screw) Selection for Fatigue Loading: Fundamentals 318 10.12 Bolt Selection for Fatigue Loading: Using Special Test Data 324 10.13 Increasing Bolted-Joint Fatigue Strength 327 11 Rivets, Welding, and Bonding 329 11.1 Introduction 329 11.2 Rivets 329 11.3 Welding Processes 330 11.4 Welded Joints Subjected to Static Axial and Direct Shear Loading 334 11.5 Welded Joints Subjected to Static Torsional and Bending Loading 337 11.6 Fatigue Considerations in Welded Joints 342 11.7 Brazing and Soldering 344 11.8 Adhesives 344 12 Springs 347 12.1 Introduction 347 12.2 Torsion Bar Springs 347 12.3 Coil Spring Stress and Deflection Equations 348 12.4 Stress and Strength Analysis for Helical Compression Springs—Static Loading 353 12.5 End Designs of Helical Compression Springs 355 12.6 Buckling Analysis of Helical Compression Springs 356 12.7 Design Procedure for Helical Compression Springs—Static Loading 357 12.8 Design of Helical Compression Springs for Fatigue Loading 360 12.9 Helical Extension Springs 368 12.10 Beam Springs (Including Leaf Springs) 369 12.11 Torsion Springs 374 12.12 Miscellaneous Springs 376 13 Lubrication and Sliding Bearings 379 13.1 Types of Lubricants 379 13.2 Types of Sliding Bearings 379 13.3 Types of Lubrication 380 13.4 Basic Concepts of Hydrodynamic Lubrication 381 13.5 Viscosity 383 13.6 Temperature and Pressure Effects on Viscosity 387 13.7 Petroff’s Equation for Bearing Friction 388 13.8 Hydrodynamic Lubrication Theory 390 13.9 Design Charts for Hydrodynamic Bearings 393 13.10 Lubricant Supply 399 13.11 Heat Dissipation and Equilibrium Oil Film Temperature 401 13.12 Bearing Materials 402 13.13 Hydrodynamic Bearing Design 404 13.14 Boundary and Mixed-Film Lubrication 409 13.15 Thrust Bearings 411 13.16 Elastohydrodynamic Lubrication 412Contents xv 14 Rolling-Element Bearings 413 14.1 Comparison of Alternative Means for Supporting Rotating Shafts 413 14.2 History of Rolling-Element Bearings 415 14.3 Rolling-Element Bearing Types 415 14.4 Design of Rolling-Element Bearings 421 14.5 Fitting of Rolling-Element Bearings 424 14.6 “Catalog Information” for Rolling-Element Bearings 425 14.7 Bearing Selection 429 14.8 Mounting Bearings to Provide Properly for Thrust Load 436 15 Spur Gears 438 15.1 Introduction and History 438 15.2 Geometry and Nomenclature 439 15.3 Interference and Contact Ratio 447 15.4 Gear Force Analysis 450 15.5 Gear-Tooth Strength 453 15.6 Basic Analysis of Gear-Tooth-Bending Stress (Lewis Equation) 454 15.7 Refined Analysis of Gear-Tooth-Bending Strength: Basic Concepts 456 15.8 Refined Analysis of Gear-Tooth-Bending Strength: Recommended Procedure 458 15.9 Gear-Tooth Surface Durability—Basic Concepts 464 15.10 Gear-Tooth Surface Fatigue Analysis—Recommended Procedure 467 15.11 Spur Gear Design Procedures 471 15.12 Gear Materials 475 15.13 Gear Trains 476 16 Helical, Bevel, and Worm Gears 481 16.1 Introduction 481 16.2 Helical-Gear Geometry and Nomenclature 482 16.3 Helical-Gear Force Analysis 486 16.4 Helical Gear-Tooth-Bending and Surface Fatigue Strengths 489 16.5 Crossed Helical Gears 490 16.6 Bevel Gear Geometry and Nomenclature 491 16.7 Bevel Gear Force Analysis 493 16.8 Bevel Gear-Tooth-Bending and Surface Fatigue Strengths 494 16.9 Bevel Gear Trains; Differential Gears 497 16.10 Worm Gear Geometry and Nomenclature 498 16.11 Worm Gear Force and Efficiency Analysis 500 16.12 Worm-Gear-Bending and Surface Fatigue Strengths 505 16.13 Worm Gear Thermal Capacity 507 17 Shafts and Associated Parts 511 17.1 Introduction 511 17.2 Provision for Shaft Bearings 511 17.3 Mounting Parts onto Rotating Shafts 512 17.4 Rotating-Shaft Dynamics 515 17.5 Overall Shaft Design 519 17.6 Keys, Pins, and Splines 523 17.7 Couplings and Universal Joints 526 18 Clutches and Brakes 530 18.1 Introduction 530 18.2 Disk Clutches 530 18.3 Disk Brakes 535 18.4 Energy Absorption and Cooling 536xvi Contents 18.5 Cone Clutches and Brakes 537 18.6 Short-Shoe Drum Brakes 539 18.7 External Long-Shoe Drum Brakes 542 18.8 Internal Long-Shoe Drum Brakes 548 18.9 Band Brakes 550 18.10 Materials 553 19 Belts, Chains, and Other Components 555 19.1 Introduction 555 19.2 Flat Belts 555 19.3 V-Belts 557 19.4 Toothed Belts 561 19.5 Roller Chains 561 19.6 Inverted-Tooth Chains 563 19.7 History of Hydrodynamic Drives 565 19.8 Fluid Couplings 565 19.9 Hydrodynamic Torque Converters 568 20 Micro/Nanoscale Machine Elements 572 20.1 Introduction 572 20.2 Micro/Nanoscale Actuators 573 20.3 Micro/Nanoscale Bearings 579 20.4 Micro/Nanoscale Sensors 583 20.5 Conclusions 595 21 Machine Component Interrelationships—A Case Study 597 21.1 Introduction 597 21.2 Description of Original Hydra-Matic Transmission 597 21.3 Free-Body Diagram Determination of Gear Ratios and Component Loads 600 21.4 Gear Design Considerations 603 21.5 Brake and Clutch Design Considerations 605 21.6 Miscellaneous Design Considerations 606 22 Design and Fabrication of the Mechanical Systems for a Remote Control Car—A Design Project Case Study 609 22.1 Case Study Summary 609 22.2 Project Components 610 22.3 Project Organization 612 22.4 System Design Considerations 613 22.5 RC Car Race 617 Problems (Available in e-text for students) P-1 A Units A-1 A-1a Conversion Factors for British Gravitational, English, and SI Units A-1 A-1b Conversion Factor Equalities Listed by Physical Quantity A-2 A-2a Standard SI Prefixes A-4 A-2b SI Units and Symbols A-5 A-3 Suggested SI Prefixes for Stress Calculations A-6 A-4 Suggested SI Prefixes for Linear-Deflection Calculations A-6 A-5 Suggested SI Prefixes for Angular-Deflection Calculations A-6Contents xvii B Properties of Sections and Solids A-7 B-1a Properties of Sections A-7 B-1b Dimensions and Properties of Steel Pipe and Tubing Sections A-8 B-2 Mass and Mass Moments of Inertia of Homogeneous Solids A-10 C Material Properties and Uses A-11 C-1 Physical Properties of Common Metals A-11 C-2 Tensile Properties of Some Metals A-12 C-3a Typical Mechanical Properties and Uses of Gray Cast Iron A-13 C-3b Mechanical Properties and Typical Uses of Malleable Cast Iron A-14 C-3c Average Mechanical Properties and Typical Uses of Ductile (Nodular) Iron A-15 C-4a Mechanical Properties of Selected Carbon and Alloy Steels A-16 C-4b Typical Uses of Plain Carbon Steels A-18 C-5a Properties of Some Water-Quenched and Tempered Steels A-19 C-5b Properties of Some Oil-Quenched and Tempered Carbon Steels A-20 C-5c Properties of Some Oil-Quenched and Tempered Alloy Steels A-21 C-6 Effect of Mass on Strength Properties of Steel A-22 C-7 Mechanical Properties of Some Carburizing Steels A-23 C-8 Mechanical Properties of Some Wrought Stainless Steels (Approximate Median Expectations) A-24 C-9 Mechanical Properties of Some Iron-Based Superalloys A-25 C-10 Mechanical Properties, Characteristics, and Typical Uses of Some Wrought Aluminum Alloys A-26 C-11 Tensile Properties, Characteristics, and Typical Uses of Some Cast-Aluminum Alloys A-27 C-12 Temper Designations for Aluminum and Magnesium Alloys A-28 C-13 Mechanical Properties of Some Copper Alloys A-29 C-14 Mechanical Properties of Some Magnesium Alloys A-30 C-15 Mechanical Properties of Some Nickel Alloys A-31 C-16 Mechanical Properties of Some Wrought-Titanium Alloys A-32 C-17 Mechanical Properties of Some Zinc Casting Alloys A-33 C-18a Representative Mechanical Properties of Some Common Plastics A-34 C-18b Properties of Some Common Glass-Reinforced and Unreinforced Thermoplastic Resins A-35 C-18c Typical Applications of Common Plastics A-36 C-19 Material Names and Applications A-37 C-20 Designer’s Subset of Engineering Materials A-40 C-21 Processing Methods Used Most Frequently with Different Materials A-41 C-22 Joinability of Materials A-42 C-23 Materials for Machine Components A-43 C-24 Relations Between Failure Modes and Material Properties A-45 D Shear, Moment, and Deflection Equations for Beams A-46 D-1 Cantilever Beams A-46 D-2 Simply Supported Beams A-47 D-3 Beams with Fixed Ends A-49 E Fits and Tolerances A-50 E-1 Fits and Tolerances for Holes and Shafts A-50 E-2 Standard Tolerances for Cylindrical Parts A-51 E-3 Tolerance Grades Produced from Machining Processes A-52xviii Contents F MIL-HDBK-5J, Department of Defense Handbook: Metallic Materials and Elements for Aerospace Vehicle Structures A-53 F.1 Introduction A-53 F.2 Overview of Data in MIL-HDBK-5J A-53 F.3 Advanced Formulas and Concepts Used in MIL-HDBK-5J A-54 F.4 Mechanical and Physical Properties of 2024 Aluminum Alloy A-58 F.5 Fracture Toughness and Other Miscellaneous Properties A-64 F.6 Conclusion A-66 G Force Equilibrium: A Vectorial Approach A-68 G.1 Vectors: A Review A-68 G.2 Force and Moments Equilibrium A-69 H Normal Distributions A-71 H.1 Standard Normal Distribution Table A-71 H.2 Converting to Standard Normal Distribution A-73 H.3 Linear Combination of Normal Distributions A-73 I S–N Formula A-74 I.1 S–N Formula A-74 I.2 Illustrative Example A-75 J Gear Terminology and Contact-Ratio Analysis A-76 J.1 Nominal Spur-Gear Quantities A-76 J.2 Actual Quantities A-78 J.3 Illustrative Example A-79 Index I-1SYMBOLS A area, cross-sectional area, arm of planetary gear A point A A 0 original unloaded cross-sectional area a influence coefficient a, a acceleration a crack depth, radius of contact area of two spheres A c effective clamped area a cr critical crack depth A f final area A r area reduction A t tensile stress area, tensile stress area of the thread B actual backlash b section width, half width of contact area measured perpendicular to axes of two parallel contacting cylinders, gear face width, band width C spring index, overall heat transfer coefficient, rated load capacity, heat transfer coefficient, constant (material property) C specific heat c distance from the neutral axis to the extreme fiber, half of crack length, radial clearance, center distance, distance between shafts, crack length c distance from the centroidal axis to the extreme inner fiber, actual distance between gear and pinion centers c cr critical crack length CR contact ratio CR actual contact ratio CG center of gravity C G gradient factor or gradient constant c i distance from the neutral axis to the extreme inner fiber CL load factor CLi life factor c o distance from the neutral axis to the extreme outer fiber CP center of aerodynamic pressure Cp elastic coefficient CR reliability factor c ???? volumetric specific heat C req required value of C Cs surface factor D diameter, mean coil diameter, velocity factor d diameter, major diameter, nominal diameter, wire diameter d av average diameter db diameter of base circle dc collar (or bearing) diameter dc∕dN crack propagation rate (dc∕dN)o crack propagation rate at (ΔK)o dg pitch diameter of gear d i minor diameter of the internal thread dm mean diameter dp pitch diameter, pitch diameter of pinion d r root (or minor) diameter E modulus of elasticity, elastic proportionality constant, tensile elastic modulus E modulus of elasticity (tension) Ep plastic strain e distance between the neutral axis and the centroidal axis, efficiency, eccentricity, train value, edge distance for joint, percent elongation at break e∕D edge margin Eb Young’s modulus for the bolt Ec Young’s modulus for clamped member, compression modulus of elasticity Es secant modulus E t tangent modulus F force, compressive force between the surfaces f relative hardenability effectiveness, coefficient of friction F, F force Fa axial force Fb bolt axial load F bru bearing ultimate strength F bry bearing yield strength Fc clamping force fc collar (or bearing) coefficient of friction Fd drag force, dynamic load xixxx Symbols F cy compression yield strength Fe equivalent radial load, equivalent static force, external force F ext external force vector applied on a member F ga gear axial force F gr gear radial force F gt gear tangential force Fi initial tensile force, initial clamping force F int internal force vector at a cross-section Fn normal force fn natural frequency Fr radial load, radial force Fs strength capacity F solid force when solid F su shear ultimate strength Ft thrust force, tendon force, tangential force, thrust load F tu tensile ultimate strength F ty tensile yield strength Fw wear capacity F wa worm axial force F wr worm radial force F wt worm tangential force G torsional or shear modulus of elasticity g gravitational acceleration or acceleration of gravity, grip length gc constant of proportionality, 32.2 lbm-ft∕lb-s2 H surface hardness, time rate of heat dissipation h section depth, height of fall, leg length, weld size, film thickness, height h 0 minimum film thickness HB Brinell hardness number I polar moment of inertia, moment of inertia, geometry factor, stress invariant i integer Ix moment of inertia about x-axis J polar moment of inertia, spur gear geometry factor K curvature factor, spring rate for angular deflection, stress intensity factor, wear coefficient k spring rate, thermal conductivity, spring rate for linear deflection, number of standard deviations, shaft spring rate K thermal conductivity K′ section property KI stress intensity factor for tensile loading (mode I) KI c critical stress intensity factor for tensile loading (mode I) Ka application factor KB constant of proportionality kb spring constant for the bolt Kc fracture toughness or critical stress intensity factor k c spring constant for clamped members KE kinetic energy Kf fatigue stress concentration factor Ki curvature factor for inner fiber, effective stress concentration factor for impact loading, constant used for calculating initial bolt-tightening force Km mounting factor K max stress intensity factor at ????max K min stress intensity factor at ????min k ms mean stress factor Ko curvature factor for outer fiber, overload factor, critical stress intensity factor for infinite plate with central crack in uniaxial tension Kr life adjustment reliability factor k r reliability factor Ks stress concentration factor for static loading Kt theoretical or geometric stress concentration factor k t temperature factor K???? velocity or dynamic factor Kw Wahl factor, material and geometry factor L length, contact length measured parallel to the axis of contacting cylinder, lead, length of weld, life corresponding to radial load Fr, or life required by the application, pitch cone length L 0 original unloaded length L e equivalent length Lf final length, free length LR life corresponding to rated capacity L s solid height L, ST, LT longitudinal direction, short transverse direction, long transverse direction M moment, internal bending moment, bending moment M0 redundant moment m mass, strain-hardening exponent, module (used only with SI or metric units) m′ mass per unit length of belt M ext external moment vector applied on a member Mf moment of friction forcesSymbols xxi M int generalized internal moment vector at a cross-section Mn moment of normal forces N fatigue life, total normal load, number of active coil turns, number of teeth, number of friction interfaces, number of cycles n rotating speed, number of cycles, normal force, number of equally spaced planet gears, index (subscript), Ramberg-Osgood parameter N′ virtual number of teeth N.A. neutral axis n c critical speed Ne number of teeth Nt total number of turns, number of teeth in the sprocket P load, cumulative probability of failure, bearing unit load, average film pressure, radial load per unit of projected bearing area, pitch point, diametral pitch (used only with English units), diameter or number of teeth of planet, band force, load (force), uniform load P actual pitch p frequency of occurrence, probability of failure, surface interface pressure, pitch, film pressure, circular pitch, uniform level of interface pressure, pressure p actual circular pitch p0 maximum contact pressure pa axial pitch pb base pitch P c tension created by centrifugal force P cr critical load PE potential energy pmax allowable pressure, maximum normal pressure pn circular pitch measured in a plane normal to the teeth Q heat energy transferred to the system, load, total tangential force, flow rate, mass flow rate q number of revolutions, notch sensitivity factor, tangential force Qf volume of lubricant per-unit time flowing across Qs side leakage rate R radius, transmission speed ratio, area ratio, radius of curvature, diameter or number of teeth of ring or annulus gear, ratio of gear and pinion diameter, load ratio, fatigue cycle stress ratio r radius, reliability r radial distance to the centroidal axis ra (max) maximum noninterfering addendum circle radius of pinion or gear rmax ag maximum allowable addendum radius on the gear to avoid interference rmax ap maximum allowable addendum radius on the pinion to avoid interference r ap, rag addendum radii of the mating pinion and gear rb base circle radius, back cone radius rbp, rbg base circle radii of the mating pinion and gear rc chordal radius rf friction radius r g actual pitch radius of gear r i inner radius rp actual pitch radius of pinion R m modulus of resilience rn radial distance to the neutral axis ro outer radius S linear displacement, total rubbing distance, Saybolt viscometer measurement in seconds, bearing characteristic number or Sommerfeld variable, diameter or number of teeth of sun gear, slip S cr critical unit load S e elastic limit S eq equivalent stress—see Table F.4 SF safety factor Sfe surface fatigue strength SH surface endurance strength S–N fatigue stress versus cycles S max maximum fatigue cycle stress—see Table F.4 S n endurance limit S′ n standard fatigue strength for rotating bending Sp proof load (strength) S sy shear yield strength S u ultimate strength, ultimate tensile strength S uc ultimate strength in compression S us ultimate shear strength, ultimate torsional shear strength S ut ultimate strength in tension Sy yield strength S yc yield strength in compression S yt yield strength in tension T torque, brake torque, band brake torque t time, thickness, nut thickness, throat length Ta alternating torque ta air temperature, ambient air temperature Te equivalent static torquexxii Symbols Tf friction torque Tm modulus of toughness, mean torque t o average oil film temperature, oil temperature ts average temperature of heat-dissipating surfaces U stored elastic energy, impact kinetic energy, laminar flow velocity U′ complementary energy V internal transverse shear force, shear force, volume V, V linear velocity, gear pitch line velocity ???? velocity at impact, sliding velocity V60 cutting speed in feet per minute for 60-min tool life under standard cutting conditions V av average velocity Vg gear tangential velocity, pitch line velocity of the gear V gt velocity of gear at contact point in tangent direction V pt velocity of pinion at contact point in tangent direction V gn velocity of gear at contact point in normal direction V pn velocity of pinion at contact point in normal direction Vs sliding velocity Vw worm tangential velocity W work done, weight, volume of material worn away, total axial load Ẇ power w load, load intensity, gravitational force, width Y Lewis form factor based on diametral pitch or module, configuration factor y distance from the neutral axis, Lewis form factor Y cr configuration factor at critical crack size Z section modulus Greek Letters ???? angular acceleration, coefficient of thermal expansion, angles measured clockwise positive from the 0∘ gage to the principal strain axes numbers 1 and 2, factor by which the compressive strength is reduced through buckling tendencies, thread angle, contact angle, cone angle, normalized crack size ???? cr normalized critical crack size ????1 normalized crack size at c1 ????2 normalized crack size at c2 ???? n thread angle measured in the normal plane Δ deflection, material parameter important in computing contact stress ????, ???? deflection ???? linear deflection, wear depth ΔA change in area ΔE change in total energy of the system ΔKE change in kinetic energy of the system ΔK stress intensity range ΔK o stress intensity range at the point o ΔL change in length ΔPE change in gravitational potential energy of the system ΔN12 number of cycles during crack growth from c1 to c2 ???? s solid deflection ???? st deflection caused by static loading (static deflection) ΔT temperature change ΔU change in internal energy of the system ???? lead angle, helix angle, ratio of actual to ideal distance between gear and pinion centers ???? angle between the principal axes and the xand y-axes, angle giving position of minimum film thickness, pressure angle, angle of wrap ????n pressure angle measured in a plane normal to the teeth ???? actual pressure angle ???? pitch cone angle ????xy, ????xz, ????yz shear strains ???? mean, viscosity ???? Poisson’s ratio—see Appendix F ???? Poisson’s ratio ???? normal strain ????1, ????2, ????3 principal strains ????f strain at fracture ????p plastic strain ???? T “true” normal strain ????Tf true normal strain at fracture ???? x, ????y, ????z normal strains ???? angular displacement, angular deflection, slope ???? P max position of maximum film pressure ???? mass density, radial distance ???? normal stress, standard deviation, uniform uniaxial tensile stressSymbols xxiii ????1, ????2, ????3 principal stresses in 1, 2, and 3 directions ????0 square root of strain-strengthening proportionality constant ???? a alternating stress (or stress amplitude) ???? e equivalent stress ???? ea equivalent alternating bending stress ???? em equivalent mean bending stress ???? eq equivalent stress ????g gross-section tensile stress ????H surface fatigue stress ???? i maximum normal stress in the inner surface ????m mean stress ???? max maximum normal stress ????min minimum normal stress ???? nom nominal normal stress ???? o maximum normal stress in the outer surface ???? T “true” normal stress ????x normal stress acting along x-axis ????y normal stress acting along y-axis ???? shear stress, natural period of vibration ????a alternating shear stress ???? av average shear stress ????initial initial shear stress ????m mean shear stress ???? max maximum shear stress ???? nom nominal shear stress ????solid shear stress when solid ???? xy shear stress acting on an x face in the y direction ???? kinematic viscosity ???? angular velocity, impact angular velocity ???? g angular velocity of gear ???? n natural frequency ???? p angular velocity of pinion ???? helix angle, spiral angle X A ABEC see Annular Bearing Engineers’ Committee (ABEC) Abrasive wear, 267–268, 465 ABS (acrylonitrile–butadiene–styrene), 63 Acetal, 63 Acme threads, 286 Acrylic, 63 Acrylic adhesives, 346 Actuators displacement-based, 577–579 force-based, 574–576 Addendum, 442 Adhesive bonding, 344 Adhesive wear, 265–267, 410 AFBMA (Anti-Friction Bearing Manufacturers Association), 424 AGMA (American Gear Manufacturers Association), 438 AISC (American Institute of Steel Construction), 329 Alkyd, 64 Alloying, 61 Alloys aluminum (see Aluminum alloys) cast iron, 56–57 copper, 60, 216, A-29 magnesium, 60, 216–217, A-28, A-30 nickel, 60–61, 216, A-31 nonferrous alloys, 59–61 steel (see Steel alloys) superalloys, 59–61, A-25 titanium, 61, A-32 zinc, 61, A-33 Allyl (diallyl phthalate), 64 Alternating loads/stress, 233–238 Aluminum anodized, 260 cavitation of, 265 connecting rod, 153–155 corrosion of, 259–261 fretting of, 268–269 notch sensitivity of, 232 Aluminum alloys, 59–60 endurance limit of, 213 fatigue strength diagrams for, 213, 216 mechanical properties/uses of, A-26, A-27 temper designations for, A-28 American Blower Company, 565 American Gear Manufacturers Association (AGMA), 438 American Institute of Steel Construction (AISC), 329 American National Standards lnstitute (ANSI), 5 American Society for Testing and Materials (ASTM), 60, 335 American Society of Mechanical Engineers (ASME), 184, 283, 329, 563 American Welding Society (AWS), 335 Amino, 64 Anaerobic adhesives, 346 Anisotropic materials, 182 Annealing, 117, 263 Annular Bearing Engineers’ Committee (ABEC), 424 Anode, sacrificial, 257, 260 Anodized aluminum, 260 Anodizing, 259 ANSI see American National Standards lnstitute (ANSI) Anti-Friction Bearing Manufacturers Association (AFBMA), 424 Approximations, 16 Ashby’s materials selection charts, 66–68 ASME see American Society of Mechanical Engineers Asperity welding, 266–267 ASTM see American Society for Testing and Materials Automatic transmission, 597 Automobiles load analysis, 25–30 performance analysis, 20–23 power train components, 27–28 transmission components, 28–30 AWS (American Welding Society), 335 Axial impact, 198 Axial loads/loading, 77–79 and Castigliano’s method, 134 with power screws, 295 and residual stresses, 109–113 reversed, 217–218 with roller bearings, 430–431 sign convention for, 80 with springs, 352 with threaded fasteners, 295 B Ball bearings and axial loading, 431 dimensions of, 425–427 history of, 415 life requirement for, 429–430 radial, 414 rated capacities of, 427, 428 reliability requirement for, 430 I-1I-2 INDEX Ball bearings (contd.) rings for, 420 selection of, 429–434 shields/seals for, 419–420 and shock loading, 432 special, 422–423 surface damage to, 273–279 thrust load, mounting for, 436–437 types of, 416, 417 Ball-bearing screws, 292 Band brakes, 550–552 Bars compression/tension, impacted in, 201–202 deflection/stiffness formulas for, 128 energy-absorbing capacity, effect of stress raiser on, 206–208 stress concentration factors of, 108–109 Base units, 12 Basic design objective, 7 Basic hole system, A-51 Beach marks, 210–211 Beam loading, 34–37 Beams bending impact, with compound spring, 200–201 bent cantilever, deflection in, 138–139 centrally loaded, deflection in, 135–136 curved, bending of, 83–88 deflection in, 130–132, A-46–A-49 deflection/stiffness formulas for, 128 extreme-fiber-bending stresses, 87–88 straight, bending of, 82–83 transverse shear loading in, 88–94 Beam springs, 369–374 Bearing(s) ball (see Ball bearings) bearings for shafts, 511–512 definition of, 579–583 micro and nanoscale, 579–583 rolling-element (see Rolling-element) sliding (see Sliding bearings) thrust, 411, 436–437 Bell crank, load analysis of, 31–32 Belt drive, with spur gears, 441 Belts flat, 555–557 toothed (timing), 561 V-, 557–560 Bending of beams, 34–35, 82–88 bevel gears, 494–497 and Castigliano’s method, 134 and fatigue strength, 212–218, 238–240 of gear teeth, 454–464 helical gears, 489–490 and residual stresses, 113–115 and shear stresses, 92–94 sign convention for, 35 worm gears, 505–507 Bending impact, 194–196, 200–201 Bevel gears, 481, 483, 491–498 bending stress with, 494–497 force analysis with, 493–494 geometry of, 491–492 large end, 491 pitch cones, 491 surface fatigue stress with, 494, 496 trains, gear, 497–498 and Tredgold’s approximation, 491 Zerol, 492 Biaxial effect (of stress raisers), 104 Biaxial loading, fatigue strength for reversed, 219–220 Biaxial stresses, 100, 102, 126 modified Mohr theory for, 179 Bioengineering, 33 Blind rivets, 330–331 Body stress(es), 77–118 from axial loading, 77–79 combined, 96–99 concentration factors, 104–107 from direct shear loading, 79–80 induced, 94–96 from pure bending loading, 82–88 residual (see Residual stresses) thermal, 115–117 three-dimensional, 100–104 from torsional loading, 80–82 from transverse shear loading, 88–94 Bolted joint, shear load capacity of, 314–315 Bolts, 299 bracket attachment, selection for, 315–318 design for impact strength of, 206–208 fatigue loading, selection for, 318–323 fatigue strength, increasing, 327–328 initial tightening tension, 301–305, 319–321 pressure vessel flange bolts, selection of, 325–326 static loading, selection for, 312–318 tension of, with external joint-separating force, 308–312 and thread-bearing stress, 295–297 types of, 300 Bonderizing, 259 Bonding, adhesive, 344–346 Boundary lubrication, 381, 409–411 Bracket(s) bolts for attachment of, 315–316 deflection of redundantly supported, 145–147 Brake(s), 530 band, 550–552 cone, 537–539 design considerations, 605–606 disk, 535–536 energy absorption/cooling with, 536–537 long-shoe drum, 542–548 materials for, 553–554 short-shoe drum, 539–542INDEX I-3 Brasses, 60 Brazing, 344 Brinell hardness test, 52–55, 213 British Comets, 4 British Gravitational units, 12–14 British thermal unit, 17 British thermal units per second, 18 Brittle fracture, 163, 204 Brittle materials, 163, 186, 219 Bronzes, 60, 265 Buckingham, Earle, 466 Buckling, 148–150, 157–158 columns, 148–158 eccentric loading, secant formula for, 155–156 of helical compression springs, 357 local, 157–158 of power screws, 298 Building codes, 184 Butt welds, 335, 343 C Cadmium, 260, 280 Camshafts power requirement, 19–20 torque requirement, 17–18 Cantilever beams, 138–139, A-46 Capacitive sensors, 584–585 Carbide, 258 Carbon fiber reinforcement, 63 Carbon nanotube–based piezoresistors, 588–589 Carbon nanotube–based rotary bearings, 582–583 Carbon steels, 57–58, A-12, A-16–A-18 Carburizing, 59, 246 Carburizing steel, A-23 Cardan joint, 527 Case-hardening steels, 59 Castigliano, Alberto, 133 Castigliano’s method elastic deflections determined by, 133–144 redundant reactions by, 144–147 Cast iron, 56–57 cavitation of, 265 endurance limit of, 213 fretting of, 268–269 mechanical properties/uses of (table), A-13–A-14 surface factor for, 220, 221 Cathode, 257 Cavitation, 264–265 Cellulosics, 63 Chains inverted-tooth, 563–564 roller, 561–563 Change, 10 Charpy test, 52, 205 Chemical surface-hardening treatments, 246 Chilling, 57 Chordal action, 562 Chrome plating, 244 Chromium, 258 Chrysler Corporation, 565 Clearance fits, A-50 Clutch(es) cone, 537–539 design considerations, 605–606 disk, 530–535 function of, 530 materials for, 553–554 Coating, 70, 73 Coining, 245 Cold rolling, 245 Column buckling, 148–158 end conditions, column length and, 150–151 equivalent stresses, 156–157 J.B. Johnson parabola for, 151–155 Column loading (of power screws), 298–299 Comb-drive actuators, 576 Comb-drive sensors, 584, 585 Combined stresses, 96–99 Compatibility, of materials, 8 Completely reversed loading, fatigue strength for, 222, 231–233 Components, mechanical, 1 Composites, 65–66 engineering, 65, 67, A-37 material, 65–66 Compound springs, 200–201 Compression, 77, 78 Compression springs, helical see Helical compression springs Concentration, stress see Stress concentration factors Cone clutches/brakes, 537–539 Configuration factor, 166, 248 Conic threaded fasteners, 286 Connecting rods, determining diameter, 152–153 Conservation of energy, 19–23 Constant-force springs, 377 Constant-life fatigue diagram, 224, 227, 228 Contact modulus, 272 Contact ratio (CR), 447–449, A-76–A-80 Copolymerization, 61 Copper alloys, 60, 216, A-29 Copper, corrosion of, 260 Corrosion, 255–265 crevice, 259 with cyclic stress, 264–265 design for control of, 259–261 and electrode/electrolyte heterogeneity, 258–259 with static stress, 262–264 Corrosion engineering, 255 Cost(s) of machined parts, 56 of materials, 45 of safety factor, 185 Coulomb, C. A., 176 Coulomb-Mohr theory, 179 Countershaft, internal loads in transmission, 35–37I-4 INDEX Couplings fluid, 565–568 shaft, 526–529 CR see Contact ratio Crack length, 165, 246–250 propagation, 164, 167, 247, 252 Cracks, stress-corrosion, 262–264 Crevice corrosion, 259 Critical sections, 37–39 Critical stress intensity factor, 164 Crossed helical gears, 481, 490 Cross-linked plastics, 62 Curved surfaces, contact stresses with, 272–278 Cyaniding, 59 Cyclic stress, and corrosion, 264 Cylindrical threaded fasteners, 286 D Damper, 192 Damping, 194 Dashpot, 192 Dedendum, 442 Deflection, 119 beam, 130–132 Castigliano’s method for determining, 133–144 caused by linear/bending impact, 194–201 caused by torsional impact, 201–204 formulas for, 128–129 and redundant reactions, 144–147 of springs, 348–353 torsional, 129 DeMoivre, 187 Density, and strength, 67–68 Design, 1–12 ecological objectives of, 7–8 overall considerations in, 10–12 process, 68 safety considerations in, 2–7 societal objectives of, 8–10 Design overload, 183 “Design stress,” 182 Diallyl phthalate (allyl), 64 Dimensionally homogeneous equations, 12 Dimensions, primary/secondary, 12 Direct shear loading, 79–80 Disk brakes, 535–536 Disk clutches, 530–535 Disk sander shaft, safety factor of, 238–240 Displacement-based actuators electrochemical actuators, 579 piezoelectric actuators, 578 shape memory alloy, 579 thermomechanical actuators, 577–578 Distortion (plastic strain), 163 Double shear, 39, 80 Drum brakes long-shoe, 542–548 short-shoe, 539–542 Ductile (nodular) iron, 57, A-15 Ductile materials, 163 fatigue strength of, 218–219, 223 machinability of, 57 Ductility, 49, A-23, A-45 Durability (of materials), 8 Duranickel alloys, 60 Dynamic loading see Fatigue; Impact E Eccentricity ratio, 155 Eccentric loading columns, 155–156 welds, 337–342 Ecological issues, 7–8 Economic issues, 279–280 Eddy current proximity sensors, 585–586 Efficiency (of power screws), 291–292 Elastic instability/stability, 148–150 Elasticity, modulus of, 46 Elastic limit, notation convention for, 46 Elastic region (true stress–strain curve), 51 Elastic strains, 119 see also Strains Elastic stress–strain relationships, 126–127 Elastohydrodynamic lubrication, 412, 464 Electrical insulators, 260 Electrical resistance strain gages, 121 Electrochemical actuators, 579 Electrochemical reaction, 255–258 Electrolytes, 257, 261 Electromagnetic actuator, 574–575 Electromagnetic (EM) microactuators, 574–575 Electron beam welding, 333 Electroplating, 244, 257, 280 Electroslag welding, 333 Electrostatic actuator, 575–576 Elongation (at fracture), 48 End-quench test, Jominy, 58 Energy conservation of, 19–23 and work, 16–18 Energy absorption capacity bolt design modification to increase, 206–208 of brakes, 536–537 effect of stress raisers on, 199–200 of materials, 51–52, 198 Engineering, 1 Engineering model, 16 Engineering stress–strain curve, 47–49 Engineering values, 46 English Engineering units, 12–14 Epoxies, 64, 345–346INDEX I-5 Equations characteristic, 103 dimensionally homogeneous, 12 equilibrium, 24–34 Equiangular rosettes, 122–124 Equilibrium and load determination, 24 and redundant reactions, 144 and residual stresses, 117 Euler, Leonhard, 148 Euler column buckling, 148–158 F “Fail-safe” design, 4 Failure, 161–190 see also Fatigue; Surface damage analysis, 250, A-53 and axial stress, 79 definition of, 163 distortion, 163 fracture, 164–174 mode, A-45 theories of, 174–182 Fasteners, threaded see Threaded fasteners Fatigue, 210–212 life prediction, 240–243 S-N formula, 230, A-74–A-75 surface fatigue failures, 278–279 and surface treatments, 243–245 in welded joints, 342–343 Fatigue life prediction, 240–243 Fatigue loading bolt selection for, 318–327 screw selection for, 318–323 spring design for, 360–368 Fatigue strength, 212–240 for completely reversed loading, 222, 231–233 concentrated stress, effect of, 231–232 definition of, 213 increasing bolted-joint, 327–328 mean stress, effect of, 222–231, 233–240 for reversed bending/reversed axial loading, 217–218 for reversed biaxial loading, 219–220 for reversed torsional loading, 304–305 for rotating bending, 212–217 and safety factors, 182–183 and surface size, 220–222 surface treatments, effect of, 243–245 Fatigue zone, 210 FCAW (flux-cored arc welding), 333 Ferrite, 258 Ferrous materials, endurance limit of, 213 Fiber-reinforced plastics, 63 Fillet welds, 335–337 Finishing, 70, 73, 74 Finite element analysis, 158–159 steps of, 158–159 Fits, A-50–A-52 Flame cutting, 117 Flame hardening, 59 Flat belts, 555–557 Flexural bearings, 580–581 Fluid couplings, 565–568 Fluoroplastics, 63 Flux-cored arc welding (FCAW), 333 Flywheel, 18 Foot-pound force, 17 Force units of, 14 work done by, 17 Force-based actuators electromagnetic actuator, 574–575 electrostatic actuator, 575–576 optomechanical actuators, 576 Force flow critical sections, location of, 37–39 with redundant ductile structures, 41–43 Formability, 73 Föttinger, H, 565 Fracture(s), 163–164, 210–212 Fracture mechanics, 164–174 of thick plates, 167–168 of thin plates, 165–167 Fracture toughness, 164 Free-body analysis of loads, 24 acceleration, automobile undergoing, 26–27 constant speed, automobile at, 25–26 internal loads, determination of, 30–31 power train components, automotive, 27–28 with three-force member, 31–34 transmission components, automotive, 28–30 Free-body diagram method, 600–603 Free-spinning locknuts, 306 Fretting, 268–269 Friction with power screws, 290 with rolling-element bearings, 415 viscous, 388 Fusion (welding), 330 G Galling, 267 Galvanic action, 255, 259, 261 Galvanic corrosion, 260 Galvanic series, 256 Garter springs, 377 Gas metal arc welding (GMAW), 332 Gas tungsten arc welding (GTAW), 332–333 Gas welding, 333 Gears, 438 bevel (see Bevel gears) design considerations, 603–605 helical (see Helical gears)I-6 INDEX Gears (contd.) materials for, 475 spur (see Spur gears) terminology, A-76–A-80 worm (see Worm gears) Gear system, 597 Glass fiber reinforced plastics, 63 GMAW (gas metal arc welding), 332 Goodman lines, 227, 228 Government standards, 4–5 Graphene-based nanoelectromechanical resonators, 595 Gray iron, 56, A-13 Greases, 379 Grinder, torsional impact in, 202–204 GTAW (gas tungsten arc welding), 332–333 Guest, J. J., 177 Guest’s law, 177 H Hall effect sensors, 586 Hammer peening, 263 Hardness, and machinability, 56 Hardness tests Brinell, 52–55 Jominy end-quench test, 58 penetration, 52–55 Rockwell, 52–55 Hastelloys, 60–61 Hazard, 5–6 Helical compression springs, 348–368 buckling analysis of, 356–357 end designs of, 355–356 fatigue loading, design procedure for, 360–368 static loading, design procedure for, 357–360 stress/strength analysis for, 353–355 Helical extension springs, 368–369 Helical gears, 482–490, 605 see also Spur gears angle of, 482, 483 bending stress with, 489, 490 crossed, 481, 490 force analysis with, 486–489 geometry of, 482–486 meshing, 487–489 pitch of, 482, 483, 485, 486 surface fatigue stress with, 490 Helical threads, 282, 283 Hencky, H., 177 Hertz, Heinrich, 273, 276 Hertz contact stresses, 273, 276, 464, 466 Hierarchy of needs, 10 High-carbon steels, 57 High-molecular-weight polyethylene, 61 High-performance interferometers, 591 High-strength low-alloy (HSLA) steels, 58 Holmes, Oliver Wendell, 161 Hooke’s joint, 527 Hooke’s law, 46 Hoop tension, 39 Horsepower, 18, 19 HSLA (high-strength low-alloy) steels, 58 Hubs, 512 Hueber, M. T., 177 Hydra-Matic transmission basic components, 598 design features, 600 power flow and gear ratios, 598, 599, 600 Hydraulic control system, 597 Hydraulic springs, 347 Hydrodynamic bearings design charts for, 393–399 design of, 404–409 Hydrodynamic drives, history of, 565 Hydrodynamic lubrication, 380–383, 390–392 Hydrodynamic torque converters, 555, 568–571 Hydrogen embrittlement, 244 Hydrostatic lubrication, 381 I Impact, 192–208 bending, 194–196, 200–201 linear, 194–201 static loading vs., 192–194 torsional, 201–204 Impact factor, 186, 194 Impact loading, with roller bearings, 430–431 Impulsive loading see Impact Inconel alloys, 61 Induced stresses, 94–96 Induction hardening, 59, 246 Inductive sensors, 585–586 Industry standards, 4–5 Inertia, moments of, A-7 Inertia welding, 333 Ingenuity, 3–4 Instability, elastic, 148–150 Insulators, 260 Interference fits, A-50 Interference points, 447–449 Interference theory of reliability prediction, 188–190 Internal loads in free-body analysis, 30–31 in transmission countershaft, 35–37 International Standards Organization (ISO), 282, 386 Inverted-tooth chains, 563–564 Iron, 257 see also Cast iron Iron-based superalloys, 59, A-25 ISO see International Standards Organization ISO screw threads, 282–283 Izod test, 52, 205 J Jacks, screw-type, 286 Johnson, J. B., 151–152 Johnson column formula, 151–155INDEX I-7 Joinability, 73, A-42 Joint(s) increasing fatigue strength of bolted, 327–328 riveted, 41–43 shear load capacity of bolted, 314–315 universal, 526–529 welded (see Welded joints) Jominy, Walter, 58 Jominy end-quench test, 58 Joule, 17 Joule heating, 577 Joules per second, 18 K Keyways (keyseats), 512, 525 Kilowatt, 18 L Laplace, P., 187 Laser beam welding, 333 Leaf springs, 369–374 Leonardo da Vinci, 415, 438 Lewis, Wilfred, 454 Lewis equation, 454–456 Life cycle, total, 4 Life quality index (LQI), 9–10 Limit elastic, 46 proportional, 46 Linear actuators see Power screws Linear cumulative-damage rule, 240–241 Linear impact, 197–200 Linearly elastic stress–strain relationships, 126–127 Linear plastics, 62 Linear variable differential transformers (LVDTs), 585 Loads/loading, 24–43 axial (see Axial loads/loading) with beams, 34–37 direct shear, 79–80 dynamic, 192, 193 eccentric, 155–156, 337–342 fatigue, 318–327, 360–368 and force flow, 37–39 with free bodies (see Free-body analysis of loads) impact (see Impact) pure bending, 82–88 and redundant ductile structures, 41–43 redundant supports, division between, 39–41 static, 192, 193 torsional loading, 80–82 transverse shear, 88–94, 298 Local buckling, 157–158 Locknuts, 306–307 Lock washers, 306 Long-shoe drum brakes, 542–548 internal long shoe, 548–550 nonpivoted long shoe, 542–548 pivoted long shoe, 548 Low-carbon steels, 57 Low-molecular-weight polyethylene, 61 LQI (Life quality index), 9–10 Lubricant(s) supply of, 399–401 types of, 379 Lubrication see also Viscosity boundary, 381, 409–411 elastohydrodynamic, 412, 464 hydrodynamic, 380–383, 390–392 hydrostatic, 381 mixed-film, 381, 410 self-, 410 M Machinability, 56 Machine component problems, methodology for solving, 14–16 Machine components, 597 Magnesium, 260 fretting of, 268–269 notch sensitivity of, 232 Magnesium alloys, 60, 216 mechanical properties of, A-30 temper designations for, A-28 Magnesium bronze, 265 Malleable iron, 57 Manufacturing, 69–71, 74 Margin of safety, 186 Maslow, Abraham, 10 Material properties, 68–75 Materials, 45–75 see also specific materials anisotropic, 182 for brakes/clutches, 553–554 brittle, 163, 179 for clutches/brakes, 553–554 compatibility of, 8 composites, 61, 65–66 corrosion of (see Corrosion) database, property, 45 ductile, 163 ecological factors in selection of, 8 energy absorption capacity of, 51–52, 198 engineering stress–strain curve for, 47–49 ferrous, 213 for gears, 475 “handbook” data on strength properties of, 55 isotropic, 182 machinability of, 56 names of (table), A-37–A-39 nonferrous (see Nonferrous metals/materials) penetration hardness tests, 52–55 properties of, 69–70 relative durability of, 8 for rivets, 330 for screws/nuts/bolts, 301I-8 INDEX Materials (contd.) selection charts for, 66–68 selection factors, 70–73 selection of, 68 selection procedure, 73–75 for sliding bearings, 402–403 for springs, 347 static tensile test for, 46–47, 50–51 strength charts for, 67–68 and stress concentration factors, 104–107 true stress–strain curve for, 50–51 value of, 45 Maximum-distortion-energy failure theory (maximum-octahedral-shear-stress failure theory), 177–179 Maximum-normal-stress failure theory, 176 Maximum-shear-stress failure theory, 176–177 Maxwell, James Clerk, 177–178 Mean stress, and fatigue strength, 222–231, 233–240 Mechanical engineering, 1 Medium-carbon steels, 57 Melamine, 64 MEMS sensors, 583, 584 Metal-inert gas (MIG) welding, 332 Metal plates, corrosion of, 261–262 Metals see also specific metals corrosion of, 255–258 database for properties of, 45 physical properties of (table), A-11 tensile properties of (table), A-12 Microactuators, 573–579 Microelectromechanical systems (MEMS) devices, flexural bearings in, 580–581 Micro/nanoscale machine elements description, 572 low-cost production, 572 Microreyn, 383 Microscale piezoelectric actuator, 578 MIG (metal-inert gas) welding, 332 MIL-HDBK-5J, 45, 164, 218, A-53–A-67 Millipascal-second, 383 Miner rule, 240 Mises, R. von, 177 Mixed-film lubrication, 381, 410 Mode I, 164 Modern gear-cutting machines, 605 Modulus of elasticity, 46 Modulus of resilience, 52, 200 Modulus of rupture, 201 Modulus of toughness, 52, 200 Mohr, Otto, 96 Mohr circle combined stresses, 96–99 and failure prediction, 176–177 for induced stresses, 94–96 for strain, 120–122, 126–127 stress state representation, 99–100 three-circle diagram, 104 three-dimensional, 126–127 for two parallel cylinders, 276 Mohr theory and fatigue strength, 220 modified, 179–180 Monomers, 61 Moore rotating-beam fatigue-testing machine, 212–213 N Nanoscale actuators, 573–579 Nanoscale flexural bearings, 581 National Bureau of Standards, 255 Necking, 48 Needle bearings, 608 Needle roller bearings, 417, 420, 421 Newton • meter, 17 Newton’s law of viscous flow, 383 Newton’s second law, 12–14 Nickel alloys, 60–61, 216, A-31 Nickel-based superalloys, 60–61 Nickel, corrosion of, 258 Nickel plating, 244 Nitriding, 59, 246 Nodular (ductile) iron, 57 Nominal mean stress method, 236 Non-feedback tunneling sensors, 592 Nonferrous alloys, 59–61 Nonferrous metals/materials for columns, 157 electroplating, 244 endurance limit of, 213 Normal distribution, 187–188, A-71–A-73 Notched impact tests, 205 Notches, 231, 417 Notch sensitivity factor, 232 Nuts locknuts, 306 with power screws, 286–289 and thread-bearing stress, 295–297 Nylon (polyamide), 63 O Ocvirk’s short bearing approximation, 392 Oil bath, 399 Oil collar, 399 Oil grooves, 400 Oil holes, 400 Oil lubricants, 379, 399–401 Oil pump, 400–401 Oil ring, 399, 400 Oldham coupling, 527 “The One-Hoss Shay,” (Oliver Wendell Holmes), 161–163 Optical heterodyne interferometers, 590–592 Optical sensors, 590–592INDEX I-9 Optomechanical actuators, 576 OSHA, 4–5 Overdesign, 161 Overhauling power screws, 290 Overload, design, 183 Oxide coatings, 259 P Packaging, 8 Paints, 260 Palmgren rule, 240 Parallel loading (welds), 334–337 Parallel plate actuators, 575–576 Parallel plate capacitive sensors, 584, 585 Parkerizing, 259 Pascal-seconds, 383 Passivation, 258, 261 Pearlite, 258 Performance requirement, 68, 69 service, 70–71 Petroff’s equation, 388–389 Phase transformations, 117 Phenolic, 65 Phenylene oxide, 63 Phosphate coatings, 259 Photoelastic patterns, 453 Piezoelectric actuators, 578 Piezoelectric bimorph actuator, 578 Piezoelectric sensors, 589–590 Piezoresistive sensors, 586–590 Pillow block, 312–314 Pinion, 440 Piston ring, tangential deflection of, 139–144 Pitch cones, 491 Pitch diameter, 443, 485, 498, 499 Pitting, 278, 464, 466 Plain carbon steels, 57–58 Planes, principal, 95 Plane strain/stress, 164 Planet bearings, 607 Plasma arc welding, 333 Plastic distortion, 163 Plastics, 61–65 applications of, A-36 designation of, 62 mechanical properties of, A-34 reinforcement of, 63 thermoplastics, 63–64, A-35 thermosets, 63–65 Plastic strain-strengthening region (true stress-strain curve), 51 Plates corrosion of metal, 259–262 local buckling/wrinkling in, 157 stress concentration factors of, 110 thick, fracture mechanics of, 167–168 thin, fracture mechanics of, 165–167 Plating, 244, 257 Pneumatic springs, 347 Pole deflection, preventing, 144–145 Polyamide (nylon), 63 Polycarbonate, 64 Polyester, 64, 65 Polyethylenes, 61, 62, 64 Polyimide, 64 Polymerization, 61 Polymers, 61–62 Polyphenylene sulfide, 64 Polypropylene, 64 Polystyrene, 64 Polysulfone, 64 Polyurethane, 64, 65 Polyvinyl chloride (PVC), 64 Poncelet, 210 Power, 18–19 camshafts, 19–20 Power screws, 286–294 axial load with, 295 column loading of, 298–299 efficiency of, 291–292 friction coefficients, values of, 290 overhauling, 290–291 purpose of, 286 rolling contact in, 292–294 self-locking, 290–291 with square thread, 289, 291 thread angle in normal plane, values of, 290 thread bearing stress with, 295–297 thread forms for, 286 thread shear stress with, 297–298 thread sizes for, 286 thrust collar with, 289 torque applied to nut in, 286–289 torsional stresses with, 295 transverse shear loading with, 298 Power train, automotive, 27–28 Power transmission, 555–571 by belt, 555–557 by chain, 561–563 by gear (see Gears) by hydrodynamic drive, 565 Press, screw, 298 Pressure, and viscosity, 264–265 Pressure vessel flange bolts, selection of, 325–326 Prevailing-torque locknuts, 306 Primary dimensions, 12 Primers, 260 Principal planes, 95 Processing, 8 Professional engineering, 1 Proportional limit, 46I-10 INDEX Pure bending loading, 82–88 with curved beams, 83–88 with straight beams, 82–83 PVC (polyvinyl chloride), 64 R Racks, 445 Radial tension, 88 Rectangular strain rosettes, 124–126 Recycling, designing for, 7–8 Redundant ductile structures, 41–43 Redundant reactions, 144–147 Redundant supports, 39–41 Reinforcement of plastics, 63 web, 40 Reliability, 161, 186–187 interference theory of reliability prediction, 188–190 and normal distributions, 187–188 Rene alloys, 61 Residual stresses, 109–115 and axial loading, 109–113 and bending, 113–115 and heat, 115–117 in steel, 117 and torsional loading, 113–115 Residual stress method, 235 Resilience modulus of, 52, 200 Resistance welding, 333 Resonance-based mass sensors, 594 Resonance-based strain sensors, 594–595 Reversed bending, fatigue strength for, 231–233 Reversed loading fatigue life prediction with, 240–243 fatigue strength for axial, 217–218 fatigue strength for biaxial, 222 fatigue strength for completely, 222, 231–233 fatigue strength for torsional, 218–219 Reyn, 383 Reynolds, Osbourne, 383 Reynolds equation for one-dimensional flow, 392 Reynolds equation for two-dimensional flow, 392 Rigidity, test for, 46 Riveted joints, 41–43 Rivets, 329–330 blind, 330–331 cost-effectiveness of, 330 materials for, 330 standards for, 329 threaded fasteners vs., 330 tubular, 330–331 Rockwell hardness test, 52–55 Rods connecting, 152–155 deflection/stiffness formulas for, 128 energy-absorbing capacity, effect of stress raiser on, 199–200 straight, impacted in compression/tension, 197–198 Roller chains, 561–563 Rolling-element bearings, 413–437 see also Ball bearings and axial loading, 431 catalogue information for, 425–427 cylindrical, 417, 418, 420 design of, 421–424 dimensions of, 425–427 fitting of, 424 friction with, 415 history of, 415 life requirement for, 429–430 needle, 417, 420, 421 rated capacities of, 427, 428 reliability requirement for, 430 selection of, 429–434 and shock loading, 432 sliding bearings vs., 413, 415 spherical, 417, 418, 421 surface damage to, 273–279 tapered, 417, 419, 421 thrust load, mounting for, 436–437 types of, 415–421 Rotating bending, fatigue strength for, 212–218 Rotating machine components, power transmitted by, 18–19 Rubber, energy absorption capacity of, 199 Rupture, modulus of, 201 Rust, 257 S Sacrificial anode, 257, 260 Safety/safety factors, 2–7, 182–184 awareness of, 2 definition of, 182–184 estimation of, for steel pan, 181–182 and ingenuity, 3–4 and margin of safety, 186 nontechnical aspects, 6–7 selection of numerical value for, 184–185 techniques/guidelines for ensuring, 4–6 SAW (submerged arc welding), 333 Saybolt seconds, 384 Scoring, 266 Screw(s), 299–301 see also Power screws ball-bearing, 289 fatigue loading, selection for, 318–323 fatigue strength, increasing, 327–328 static loading, selection for, 312–318 tamper-resistant, 301 types of, 300 Screw press, 298 Scuffing, 267 Secant formula, 155–156 Secondary dimensions, 12 Sections, properties of, A-7–A-9INDEX I-11 Self-locking power screws, 290 Self-locking screws, 305–308 Self-loosening (of screws), 305–308 Self-lubrication, 410 Sems, 299 Sensors micro and nanoscale, 583–760 Shaft(s), 511–529 bearings for, 511–512 definition of, 511 deflections in, 130–133 design considerations with, 519–523 dynamics of rotating, 515–518 fatigue with, 236–238 joining of, 523–526 mounting parts onto rotating, 512–514 rigid couplings for, 526 stresses in, 96–99 torque-transmitting connections with, 523–526 torsional stress/deflection of, 202–204 transmission countershaft, internal loads, 35–37 universal joints with, 527–528 Shape memory alloys (SMA), 579 Shear modulus of elasticity, and viscosity, 383, 384 Shear/shear loading direct, 79–80 double, 39, 80 in load analysis, 34–37 and sign convention, 35 sign convention for, 80 Shear strains, 120, 121 Shear stresses in beams, 88–94 and bending stresses, 92–94 and distortion, 163 Shielded metal arc welding (SMAW), 331 Shock see Impact Shock absorber, 192 Short-shoe drum brakes, 539–542 Shot peening, 245–246, 263 Significant strength
كلمة سر فك الضغط : books-world.net The Unzip Password : books-world.net أتمنى أن تستفيدوا من محتوى الموضوع وأن ينال إعجابكم رابط من موقع عالم الكتب لتنزيل كتاب Fundamentals of Machine Component Design - Seventh Edition رابط مباشر لتنزيل كتاب Fundamentals of Machine Component Design - Seventh Edition 
|
|