Admin مدير المنتدى


عدد المساهمات : 18996 التقييم : 35494 تاريخ التسجيل : 01/07/2009 الدولة : مصر العمل : مدير منتدى هندسة الإنتاج والتصميم الميكانيكى
 | موضوع: كتاب Stretch Blow Molding الأربعاء 14 يونيو 2023, 7:11 am | |
| 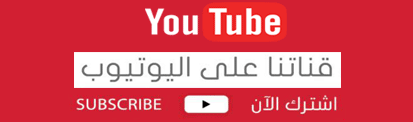
أخواني في الله أحضرت لكم كتاب Stretch Blow Molding Third Edition O. Brandau Member of Society of Plastics Engineers Member of Mensa Canada
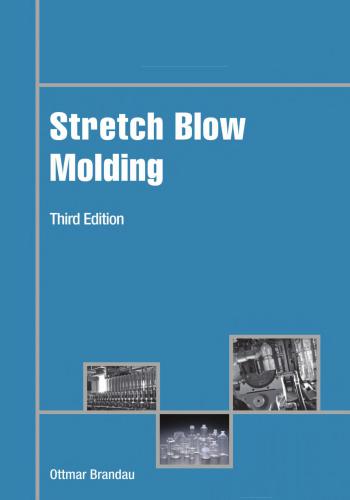 و المحتوى كما يلي :
Table of Contents Preface to the Third Edition Acknowledgments Introduction 1: Short History of Stretch Blow Molding Abstract 2: Material Basics Abstract 2.1. Manufacture and States of PET 2.2. Crystallization of PET 2.3. Drying of PET 2.4. Other Consequences of Insufficient Drying 2.5. Behavior in the Injection Mold 2.6. Behavior in the Blow Mold 3: Reheat Stretch Blow Machine (RSBM) Types Abstract 3.1. Overview 3.2. Differences Between Rotary Machines of Different Manufacturers 3.3. Orientation of Preforms and Bottles 3.4. Movement Actuation 3.5. Shape and Location of Oven Section 3.6. Blow Mold Actuation 3.7. Preform Seal 3.8. Synchronization and Crash Protection 4: Machine Details Abstract 4.1. Oven Section 4.2. Transfer Functions 4.3. Blow Wheel/Blow Clamp 4.4. Machine Timing 4.5. Rotary Machines Comparison 5: Blow Molds Abstract 5.1. Design 5.2. Base Mold 5.3. Making a Mold 5.4. Venting 5.5. Stretch Rod 6: Fundamentals of the Blow Process Abstract 6.1. Process Overview 6.2. Stretch Ratios 6.3. Types of Heat Transfer 6.4. Light Absorption Characteristics of PET 6.5. Optimal Preform Temperature 7: The Blowing Process Abstract 7.1. Reheating Preforms 7.2. Blowing Bottles 7.3. Air Valve Control 8: Injection Stretch Blow Molding Machines Abstract 8.1. Four-Station Machines 8.2. Machine Controls 8.3. Injection Controls 8.4. Interaction Between Injection and Blow 8.5. Conditioning 8.6. Container Blowing 8.7. Hot Runners 8.8. Integrated Two-Stage Stretch Blow Molding 8.9. Single or Two Stage—That is the Question 9: Special Applications Abstract 9.1. Simulation of the Blow Process 9.2. Stretch Blow Molding of Oriented Polypropylene 9.3. Plant-Based Plastics 9.4. Blow Process for Hot-Fill Applications 9.5. Preferential Heating 9.6. Direct Feeding of Preforms into the Blow Machine 9.7. Vision Inspection 9.8. Barrier Enhancing Technologies 9.9. Blow-and-Trim Process 9.10. CSD Bottle Base Failures 9.11. Recycling of PET Bottles 9.12. Preform Aesthetics in the Two-Stage Process 9.13. Blowing Thick-Walled Preforms 10: Troubleshooting of Blowing Problems Abstract 10.1. General Guidelines 10.2. Starting a New Process 10.3. Preblow Pressure Control 10.4. Changing Preform Temperatures 10.5. Output Control 10.6. Troubleshooting of Specific Problems 10.7. Defects Particular to Single-Stage Molding 10.8. Summary of Preform Quality Checks 11: Economics Abstract 11.1. Container Types 11.2. Business Models 11.3. Tooling Costs 11.4. Lightweighing of Bottles and Caps 11.5. Resin Prices 11.6. Bottle Production Costs 11.7. Starting with a New Product 11.8. Recommended Laboratory Equipment for RSBM Plants 11.9. Western Versus Asian Machinery 11.10. Bottle Storage and Transport 12: Preform Design for Single- and Two-Stage Processing Abstract 12.1. Two-Stage Process Injection Molding 12.2. Single-Stage Process Injection Molding 12.3. Goals and Conditions 12.4. The Mechanics of Preform Design 12.5. Putting it all Together 13: Auxiliary Equipment Abstract 13.1. Compressors 13.2. Chillers 13.3. Conveyors and Bottle Storage Devices 14: Training of Operators Abstract 14.1. Current State of Training 14.2. Obstacles to Training Programs 14.3. Rethinking Abstract Concepts 14.4. Language Structure 14.5. Converting Formulas Into Common English Sentences 14.6. Substituting Uncommon Arithmetical Operators 14.7. Presentation Style 14.8. Translating Graphs into Common-Day Language 14.9. Choosing Easy-to-Understand Drawings 14.10. Computer Simulations 14.11. Comprehensive Coverage 14.12. Trainees Involvement 14.13. Assessments 14.14. Conclusions Index x A Acetaldehyde (AA), 7, 21, 268 Additives in injection molding, 198 nanoclays, 200, 201 scavengers, 199 Airback phase, 71 Air consumption, 70 cost, 72 Air conveyors, 44 Air-cooled chiller, 323 advantages and disadvantages of, 324 flow in, 326–327 Air valve control, 101 Alkali cleaning agents, 207 Antislip agents, 44 Aspect ratio, 168 B Balayage process, 153 Baled bottles, 212 Barrier enhancing technologies, 189 additives in injection molding, 198 nanoclays, 200, 201 scavengers, 199 blowing of multilayer preforms, 193–196 multilayer die, 195 SurShield multilayer structure, 195 evaluating barrier solutions, 202 average oxygen concentration post N2 purge, 203 external coatings, 197 solutions, 156 internal plasma coatings, 196–197 companies made developments in, 196–197 methods of barrier enhancements, 193 monolayer solutions, 200 permeation rate, 190 factors, 190 product types, 191 beer, 193 carbonated soft drinks, 192 chemicals, 193 cosmetics, 192 juices and functional drinks, 192 milk, 192 Base cup, 2 Base inserts, 73 Base with hole screen shot, 184 Beer bottles, 268 Bekum’s double-sided extrusion, 2 Blow cavity air flow, 101 Blow clamp, 63 Blow dome, 47 Blow-fill-seal systems, 291 Blowing, problems solving criteria for, inspection of incoming preforms, 261 guidelines, 224 CSD bottles, section weighing, 227, 228 heater lamp settings, correlation, 224 neck support ring (NSR), 224 reheat characteristics, PET, 224 Hall effect sensor, 226346 Index material distribution, effect of various parameters, 249 new process, 227 bottle wall thickness, checking of, 230 lamp settings, 228 pearlescence, 230, 231 preform cooling, 228 pressure setting, 230 reheat and blow, 229 rupture problems, 230 start-up heat profile for, preform, 229 output control, 233 in fastest rotary machines, 233 limit of, 233 quality bottles, yielding of, 234 single-stage machines, preform temperature distribution, 234 in two-stage machines, 233 preblow pressure control, 231 blow of bubble, 231 bottles made with preblow pressure, 231 preblow audit, 231 preform temperature, 231 pressure setting, 232 preform temperatures, changing, 232 in single stage machines, 233 in two-stage machines, 232 preform with scratches, location of lamps, 225, 226 single-stage molding, defects bottle cloudiness, 255 bubbles in, preform/bottle, 256 gate/body splay, 259–260 preform stringing, 256–258 short shots, 260–261 sink marks, 258 specific problems, troubleshooting of base of bottle candle stick, excessive material, 236–237 bottle body, rings forming in, 245–246 bottle split-line, flats on, 244–245 bottle volume with age, excessive changes, 247 burst test, 247–248 circumference of bottle, 246 cracked gates, 251–252 CSD bottles, cracking of, 249–251 drop impact, failure, 252 haze in bottle walls, 239–241 material folding, neck area, 236 neck area, internal folding in, 235 necks, deform, 243–244 off-center gate, 238–239 panel sink, 253–255 pearlescence/stress whitening, 241–242 preform gate, position of, 238 top load test, failure, 253 underblown bottle, 244 uneven axial wall distribution, 249 stretching, 226 Blow machine effective air cooling feature, 88 thermocouple, 88 variable speed motor, 88 Blow mold halves base insert, 74 in and out of mold base, 74 Blow molding, 208, 337 machines, 1 plants, 337 Blow molds, 18, 69, 91 actuation, 46 air valves, use of, 101 dead air loss minimization, 101 aluminum type used, 73 AL 7075 T6, 73 alumenec 89, 73 T-2024, 73 Blowing, problems solving (cont.)Index 347 base mold formation, 76 behavior, 18 design, 73–75 in double-row machine, 122 inside pressure curve, 100 optional air recovery, with, 100 mold-making process, 76 natural stretch ratio, 18 stretch rods, role of, 78–79 venting, 77 Blown bottles, 25 wall thickness measurement by infrared sensors, 186 Blow process for hot-fill applications. See Blow process, for hot-fill applications overview, 81 Blow process, for hot-fill applications amorphous PET, 158 blow mold coating, 163–165 electroless nickel (EN) plating process, 164 blow molds for hot-fill bottles, 162–163 cooling channel layout, 162 preform temperatures incorporation, on mold surfaces, 163 cold aseptic filling, 160 clean room specifications, 161 crystallized neck, 152 demands on bottle, 149–151 concept drawing for hot-fill bottle, 151 double-blow/two-wheel process, 156–159 bottle mold and container dimensions, affect of temperatures, 159 heat setting with cooling air blowing through the stretch rods, 159 heat-set wide-mouth jars, 157 neck finish, during hot-fill process, 158 preforms, reheated in the neck down position, 158 specially designed jar bottom, 160 economic considerations, 160 first bottle mold, 159 and heat-set wide-mouth jars, 157 hot-fill process, 148–149 temperatures in a glass and PET bottle behave and controlled distortion, 149 vacuum panels contract in, 150 materials for hot-fill bottles, 165 molds for heat set, 154 panel-less designs, 166 percentage of shrinkage, 155 process, 151–153, 156 crystallized neck, 152 heat set, made from stainless steel, 154 thermo image, preform for heat set, 153 standard heat setting, 159 standard process, 158 thermo image, preform for heat set, 153 volume shrinkage test, 154–156 percentage of shrinkage, 155 Blow process, simulation of, 136 applications, 139–140 costs and benefits, 140 and output, 137–139 preparations, 136–137 Blow station, 112 Blow wheel, 63 Bottle failures, 208 Bottle production. See also Business models; Production costs, bottle build machine output, 286 capital cost, major influence on part cost, 297348 Index cause and effect, machine output, 287 demand and supply, 285 fully automatic test machine, 295 high-cavitation machines, 288 planning process, 292 process flow, 288 blow-fill-seal systems, 291 blow molding machine, 289 buffer time, 289, 290 cost and heat history, 290 downstream equipment, 289 Monobloc configuration, 291 overflow bottles and deliver, 290 palletizing/depalletizing systems, 289 types of packing, 288 value-added services, 288 process selection, 286 RSBM machines, 287 scrap rate, 298 seasonal demand, 286 SKUs, 287 storage and transport, 298–299 transportation costs, 288 Western vs. Asian machinery, 293–297 Bottles blowing, 91, 93–99 high-pressure blow, 98–99 mechanical adjustment careful point, 93 mold closed, 94 mold opening, 99 preblow pressure, role of, 96–97 stretch rod at base insert, 97–98 stretch rod engagement, 95 stretch speed, role of, 97 set value base weight, 187 wall thickness monitoring system, 188 Bottle-to-bottle recycling, 211 Bubble cavity filling, 98 delaying high-pressure blow, 99 Burst test, 247–248 Business models axial stretch ratio, 270 blow ratio, 270 bottle production costs, 282–285 bottles and caps, lightweighing of, 272 lighter caps, 273 lighter necks, 272 new bottle designs, 277 special machines, 279 converters, 269 internal hoop stretch ratio, 270 machine setup sheets, 271 PCO 1881 closure, 275, 276 PET bottles manufacturing, ways to, 269 preform body and gate wall thickness, 271 preforms and bottles, 269 preform temperatures, 271 preform weight, 270 resin prices, 280 banding agreements, 281 costs balancing, 281 HDPE, 281 LDPE, 281 market, 281 PE, 281 PET, 281 raw materials, 280 supply and demand, 280 tooling costs neck size for, categories of CSD, 270 rationalization, 270 selection of tooling components, matching range, 270 Western vs. Asian machinery, 293–297 Bottle production. See also Business models; Production costs, bottle (cont.)Index 349 C Cam-driven movements, 46 Cam-driven pneumatic cylinders, 69 Candle stick, 236 Cappello design, 279, 280 Carbonated soft drinks (CSD), 2, 67, 207, 263 base design, 264 bottles, 301 base failures, 207 burst test for, 247 common neck finishes for, 265 containers, 77 cracking of, 249 maximum carbonation loss, 265 petaloid base, 264 Catalysts, 7 Caustic soda, 214 Central water chilling system, 325 Champagne style base, 92 Changeover times, 68 CHDM. See Cyclohexane dimethanol (CHDM) Chiller refrigeration cycle, 323 Chillers air-cooled system, 323 auxiliaries cooling, 328 capacity, units used to describe, 327 chilled water requirements, calculation of, 327 correction factor/relative humidity, 322 hydraulic oil cooling, 328 process cooling, 328 pump sizing, 329 refrigeration cycle, 323 water-cooled system, 323 Coating technologies, 4 Compressor air delivery capacity, impact, 320 air requirements, calculation of compressor cycle, 318 constant-volume/variable-pressure machines, 317–319 discrete steps, 317 function of, 317–319 relevant correction factors, 321 selection, 320 site air demand (SAD), 320 Conditioning core for oval container, 121 Conditioning station machine, 120 Container blowing, 121–123 Convectional heat, 55 Conventional oven system, 54 Conveyors, 219, 329 soft-drop type, 219 Conveyors and bottle storage devices conveyors, 329 palletizer/depalletizer systems, 330 Silos, 330 unscramblers, 332 feature rotating disks, 333 Cooling time, 17 Copolymer resins, 5 Cost-effective operation, 14 Crystallization, 9 CSD. See Carbonated soft drinks (CSD) Custom containers neck finishes of, 267 Plastic Bottle Institute, 266 reheat stretch blow molding (RSBM) process, advantages, 267 Cyclohexane dimethanol (CHDM), 8 Cylinder-driven movements, 46 D Decontamination, 215 DEG. See Diethylene glycol (DEG) Diethylene glycol (DEG), 7 E Eastman chemicals, 281 EG. See Ethylene glycol (EG) Ejection station, 112 Elastic deformation, 19, 20350 Index Electrically operated valve air-operated, switch to, 101 Electromagnetic spectrum, 84 Equilibration time, 339 ESL. See Extended shelf life (ESL) Ethylene glycol (EG), 6 Ethylene vinyl alcohol (EVOH), 143 Extended shelf life (ESL), 4 Extruder melting in, 112–113 throat, 112 F Fan cooling, 57 FDA. See US Food and Drug Administration (FDA) First-in first-out (FIFO), 299 Flakes, 206, 212, 215, 216 Four-station machines, 108–111 conditioning, 120–121 device heater bands, 120 temperature-controlled conditioning cores, 120 function, 121 G Gas chromatograph, 25 Gripper, 44 H Hall effect sensor, 226 HDPE. See High-density polyethylene Heating configuration mandrels spinning prevention, 170 Heat-set bottles, 266 High-density polyethylene (HDPE), 140, 281 and PET prices, diverged over time, 282 High-quality bottle, blow molds, importance of, 73 High-speed machines, 44 air conveyors, 44 antislip agents, 44 gripper, 44 transfer ring, 44 Homopolymer, 5 Hopper, 30 Hot-fill bottle bottle bottom use, 167 hole vents, 78 Hot runners, 123–129 brazing, 127 curved melt paths, 127 flow channel design, 123–128 gate mechanism, 128–129 single-stage molding, 124 single-stage setup melt distribution, 126 thermally gated nozzle, 128 husky injection molding systems, 279 I Infrared lamps, 53, 83, 85 emission peaks, 53 pinch sections, 53 quartz, 53 typical range of emitted wavelength, 85 Injection controls, 114–118 hold pressure, 116 hold time, 116 injection pressure, 114–115 injection speed, 114–115 transition point, choosing of, 116 interaction with blow, 118–119 tools, 110 two-stage molding, 126 vertical tooling, 109 advantage, 109 disadvantage, 111 Injection controls cooling time, 116 cushion control, 117 practical example, 118Index 351 Injection mold behavior, 14 components, 14 Injection molding machine, 215 Injection stretch blow molding (ISBM), 107 four-station process, 109 machine cold start, 113 integrated two-stretch blow molding (ITSBM), 108 soft start, 113 three or four station, 108 Integrated two-stretch blow molding (ITSBM), 108, 130–131 Intrinsic viscosity (IV), 7, 97 IPA. See Isophthalic acid (IPA) Irregular shaped bottles hoop extension calculation method, 168 ISBM. See Injection stretch blow molding (ISBM) Isophthalic acid (IPA), 8 ITSBM. See Integrated two-stretch blow molding (ITSBM) IV. See Intrinsic viscosity (IV) L Laminar flow, velocity profile in, 327 Lamp adjustment, 91 Lamp control, 55 Layout, 50 close spacing, 50 infrared lamps, 50 LDPE. See Low-density polyethylene (LDPE) Lightweight bottles, 28 Linear condensation polymer, 7 Linear continuous motion machines, 34 Linear machines, 61 Linear ovens, 38, 92 U-shaped track system, with, 92 Linear RSBM machine typical mold design, 74 Linear shuttle type machines, 30 Locking mechanisms, 63 Low-density polyethylene (LDPE), 140, 281 M Machine controls, 112–113 melting in extruder, 112–113 Machine cutter path creation computer-aided design (CAD)/ computer-aided manufacture (CAM) programs, role of, 76 Machine timing, 63 Magna-Mike, 226 Maximum drying temperature, 13 Melt channel ring-shaped temperature spike, 125 Melt phase condensation, 6 Microwaves, 46 stations, 54 Modern ovens, 92 Mold assembly, 95 Mold close signal, 122 Mold-making process three-dimensional (3D) computer model, 76 Mold movements, 46 Movement actuation, 46 N Near-infrared (NIR), 54 Neck support ring (NSR), 59, 82, 91 Neutraceuticals, 4 NIR. See Near-infrared (NIR) NSR. See Neck support ring (NSR) O OPP. See Oriented polypropylene (OPP) Optimal preform temperature, 88–89 Oriented polypropylene (OPP) stretch blow molding, 140 applications, 142–143 hot-fill bottle in OPP, 144 OPP and PET preforms for same bottle, 143352 Index HDPE, 140 LDPE, 140 multilayer, 143 construction OPP/EVOH/OPP, 145 EVOH or nylon, as barrier layer, 143 wheel machines, use of, 144 and PET, 141 process difference, 141–142 Oven section, 46, 49 location, 46 shape, 46 P Palletizer/depalletizer systems, 330 Pancake cylinders, 46, 75 Pearlescence, 88, 89, 230, 231 Pellets, 215 PEN. See Polyethylene naphthalate Permeation rate, 190 factors, 190 Petaloid base, 2 PET bottle, 209 challenge test, 214 recycling, 210 PIA. See Purified isophthalic acid (PIA) Piston compressor air delivery capacity, impact, 320 air requirements, calculation of, 319–320 compressor cycle, 318 constant-volume/variable-pressure machines, 317–319 discrete steps, 317 function of, 317–319 relevant correction factors, 321 selection, 320 site air demand (SAD), 320 Planar stretch ratio (PSR), 304 Plant-based plastics, 145 emission of carcinogens and ecotoxicity, 145 main characteristics, overview, 147 processing PLA, 147–148 Plastic Bottle Institute, 266 PLC. See Programmable logic controller (PLC) Pneumatic cylinders, 70 Polycarbonate (PC), 220 Polyethylene (PE), 281 Polyethylene naphthalate (PEN), 268 Polyethylene terephthalate (PET), 1, 5, 76, 96, 263, 301 acetaldehyde in, 21 bottle shapes and applications, 264 crystallization, 9 drying, 12 glass transition temperature of, 299 growth rate of, 280 infrared lamps output absorbtion, 85, 86 light absorption characteristics of, 84–88 linear condensation polymer, 7 manufacture, 5 microcracks, 88 production and solid-stating, 281 property data, 21 self-leveling, 128 states, 5 stringing, 128 temperature process window, 88 time of blowing, 121 United States, production in, 281 Polymerization, 5 Polyolefins, 214 Polypropylene (PP), 281 Preblow pressure, 95–97 bubble creation, 97 Preblow setting adjustment by base weight, 189 Preferential heating, 166–170 wall thickness distribution, improvement, 169 Preform design bottle and, 307 Oriented polypropylene (OPP) (cont.)Index 353 calculations in, spread sheet, 312, 314 completed preform, 313 draw ratio, 313 internal hoop stretch ratio, 309 1 L bottle, sketch, 311, 312, 315 mechanics of, 304 3D computer-aided design programs, 305 degree of orientation, 304 length of, 305 planar stretch ratio (PSR), 304 parameters, 307 PCO 1810 neck, 309 shapes, 305 software reveals, weight of, 314 spreadsheet in, 310 thick bottle bases wide-mouth preforms, with large tapers, 308 transition area, 306 transition ratio for, 306 transition zone, 311 typical ratios for, applications, 305 wall thickness, 310 Preforms, 45, 73, 79, 108–111, 114, 120, 122, 126, 130, 132 blowing temperature, 86 blowing thick-walled, 220 bubbles in, 256 for carbonated beverages, 82 cooling, 228 design. See Preform design direct feeding into blow machine, 170–181 conveyors, 176–177 economical considerations, 179–180 general observation, 170–171 layout, 177 operation, 178 other automation, 180 temperatures, 172–175 examination, 92 gate, position of, 238 incoming, inspection criteria for, 261 inside and outside wall graph of empirical temperature data, 86, 87 inspection, 185 movement by high-pressure blow, 100 orientation, 45 O-ring, 94 air exchange inhibition, role in, 94 O-ring, sealing by, 94 production, 208 reheating, 84, 91–93, 168 scratches, location of lamps, 225, 226 seal. See Preform seal single-stage machines, temperature distribution for, 234 start-up heat profile for, 229 temperature, 126 computer simulation, 119 infrared photograph, 126 temperature, changing, 231, 232 thermo image, at oven exit, 89 transfer to mandrels, 130 wall thickness, 92 Preform seal, 47 Production costs, bottle, 282–285 compressor power consumption, 285 preform costs, 282 cost of manufacturing, widemouth containers, 284 economy of scale, 283 high-capacity injection systems, 283 high-cavitation tools, 96-cavity tool, 283 maximum mold cavitation, 284 three/four postmold cooling stations, 283 water-cooled take-out tubes, 283 typical bottle production costs, 284 typical energy costs in, 285354 Index Programmable logic controller (PLC), 58 Purified isophthalic acid (PIA), 8 Purified terephthalic acid (PTA), 280 R Reciprocating piston compressors, in PET, 322 Recommended cooling time vs. preform wall thickness, 117 Recommended hold time vs. preform wall thickness, 117 Recommended injection fill time vs. preform weight, 115 Recycled polyethylene terephthalate (RPET), 211 Reflectors oven systems, 57 Reheat stretch blow machine types of heat transfer, 84 conduction, 84 convection, 84 radiation, 84 Reheat stretch blow machines, 27 Reheat stretch blow molding (RSBM), 18, 73, 267, 317 capital and operating costs, 293 equipment for, quality control functions, 294 laboratory equipment for, 293 quality control and manufacturing, 293 zero defect procedures, 293 Reynolds number, 327 Rotary blow machine, 169 Rotary high-speed machines, 3 Rotary machines, 1, 37, 58, 73 blow mold with locking mechanism, 75 blow wheel movement, 91 comparison, 66 crash protection, 48 by different manufacturers, 45 mandrel chain speed, 91 synchronization, 48 Rotary stretch blow molding machine cycle diagram, 93 Rotating dials, 29 RPET. See Recycled polyethylene terephthalate (RPET) RSBM. See Reheat stretch blow molding (RSBM) S Screw, 112, 114 diameter, 116 metering zone, 112 rotational speed, 112 stroke, 116, 117 transition or switchover point, 115 Semiautomatic machines, 28 Servo-driven stretch rods, 46 Servomotors, 69 Servo motor system, 46 Shelf life, 4 Shell molds, 73 Short shot, 125 Sidel blow molder with vision inspection, 182 Silos, 330–332 bottle size and, 332 storage capacity, 332 Single-stage machines, 27 blow function, trigger of by timers, 123 Single-stage molding stretch rods, role of, 80 Single stage process, 217. See also Single-stage machines; Single-stage process injection molding advantage, 131 disadvantage, 131 vs. two stage, 131–133 Single-stage process injection molding. See also Preform design beneficial feature of, 303 blow molding process, 303 conditions, 304Index 355 goals, 303 mechanics, preform design, 304 planar stretch ratio (PSR), 304 preform shapes, 305 typical ratios for, applications, 305 Solid state polycondensation (SSP), 216 Solid stating, 7, 281 Spin preform, 169 Standard process wall thickness distribution limit, 169 Steep angles, 92 Stock keeping units (SKU), 287 Storage placement, 219 Strain hardening, 20 effect, 128 Stress cracking, 209 agents, 207 testing, 209 Stress-crack resistance, 8 Stress-induced crystallinity, 10 Stretch blow molding, 1, 10 Stretch blow process, 166 Stretch ratios, 81–83 axial, 82 hoop, 82 Stretch rods, 122 adjustment, 46 preform lower part, engagement, 96 prevention of cooling effect, 79 stops, 69 Surface contaminants, 212 closures, 212 ink, 212 labels, 212 SurShield multilayer structure, 195 Synchronization, 48 T Temporization, 97, 98 Terephthalic acid (TPA), 6 Thermally gated hot runners vs. valve-gated hot runners, 129, 132 Thermocouples, 57 TPA. See Terephthalic acid (TPA) Training, of operators arithmetical operators, substituting uncommon, 338 assessments, 342 blow molding process, 337 choosing easy-to-understand drawings, 339 common-day language, translating graphs, 338, 339 comprehensive coverage, 340 computer simulations, 340 current state of, 335 english sentences, converting formulas to, 337 equilibration time, 339 in-plant, 342 language structure, 337 obstacles to, programs, 336 off-plant, 342 preform/bottle with mark, 341 presentation style, 338 rethinking abstract concepts, 337 trainees involvement, 340 Transfer ring, 44 Two-stage process, 217. See also Two-stage process injection molding advantage, 132 disadvantage, 132 preform aesthetics, 217 Two-stage process injection molding. See also Preform design carbonated soft drinks (CSD) bottles, 301 conditions, 304 goals, 303 mechanics, preform design, 304 planar stretch ratio (PSR), 304 polyethylene terephthalate (PET), 301 preform shapes, 305 typical ratios for, applications, 305356 Index U Uneven axial wall distribution, 249 United States recycling rates, 212 resin production, 281 US Food and Drug Administration (FDA), 214 V Valve engagement, stages blow phase, start of, 103 exhaust phase, 105 high-pressure blow, 104 high-pressure phase, end of, 104 mold close position, 102 preblow phase, 103 start position, 102 Valve gated hot runners vs. gate vestige of preforms, 129 Virgin resin production, 211 Viscous heating, channel walls friction, 125 Vision inspection, 181–188 applications, 183 beyond, 185–188 installed on blow molder, 184 system equipped cameras, 183 system overview, 182–183 Voltage regulators, 55 W Water bottles, 67. See also Production costs bottom layer of pallet, static load over period of time, 279 injection molding process, 266 lightweight sparkling bottle, 280 load of empty and bottles in kilogram, 278 neck finishes, 266 new designs, 277 preform design, improved, 278 twenty six millimeter caps, 276 Water-cooled system, 323 advantages and disadvantages of, 324 antifreeze, in cooling, 324 flow in, 326–327 Y Yield stage, 19, 20, 97
كلمة سر فك الضغط : books-world.net The Unzip Password : books-world.net أتمنى أن تستفيدوا من محتوى الموضوع وأن ينال إعجابكم رابط من موقع عالم الكتب لتنزيل كتاب Stretch Blow Molding رابط مباشر لتنزيل كتاب Stretch Blow Molding 
|
|