Admin مدير المنتدى


عدد المساهمات : 18992 التقييم : 35482 تاريخ التسجيل : 01/07/2009 الدولة : مصر العمل : مدير منتدى هندسة الإنتاج والتصميم الميكانيكى
 | موضوع: كتاب Reference Document on the Best Available Techniques for Waste Incineration السبت 29 مايو 2021, 1:46 am | |
| 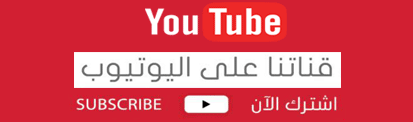
أخوانى فى الله أحضرت لكم كتاب Reference Document on the Best Available Techniques for Waste Incineration Integrated Pollution Prevention and Control EUROPEAN COMMISSION
 و المحتوى كما يلي :
Waste Incineration EXECUTIVE SUMMARY .I PREFACE .XI SCOPE .XXXIII 1 GENERAL INFORMATION ON WASTE INCINERATION . 1 1.1 Purpose of incineration and basic theory . 1 1.2 Overview of waste incineration in Europe . 2 1.3 Plant sizes . 5 1.4 Overview of legislation 6 1.5 Waste composition and process design 6 1.6 Key environmental issues 9 1.6.1 Process emissions to air and water 9 1.6.2 Installation residues production 10 1.6.3 Process noise and vibration . 11 1.6.4 Energy production and consumption 12 1.6.5 Consumption of raw materials and energy by the installation 13 1.7 Economic information 13 2 APPLIED TECHNIQUES 19 2.1 Overview and introduction . 19 2.2 Pretreatment, storage and handling techniques 20 2.2.1 Municipal solid wastes (MSW) 21 2.2.1.1 Collection and pretreatment outside the MSW incineration plant . 21 2.2.1.2 Municipal solid waste pretreatment within the incineration plant . 22 2.2.1.3 Waste delivery and storage . 22 2.2.1.3.1 Waste control . 22 2.2.1.3.2 Bunker 22 2.2.2 Hazardous wastes 23 2.2.2.1 Brief description of the sector . 23 2.2.2.2 Waste acceptance 24 2.2.2.3 Storage 25 2.2.2.3.1 Storage of solid hazardous waste . 26 2.2.2.3.2 Storage of pumpable hazardous waste . 26 2.2.2.3.3 Storage for containers and tank containers . 27 2.2.2.4 Feeding and pretreatment 27 2.2.3 Sewage sludge 28 2.2.3.1 Composition of sewage sludge 28 2.2.3.2 Pretreatment of sewage sludge 29 2.2.3.2.1 Physical dewatering . 29 2.2.3.2.2 Drying 30 2.2.3.2.3 Sludge digestion . 31 2.2.4 Clinical waste 31 2.2.4.1 Nature and composition of clinical wastes 31 2.2.4.2 Handling, pretreatment and storage of clinical waste 32 2.3 The thermal treatment stage . 32 2.3.1 Grate incinerators 35 2.3.1.1 Waste feeder 36 2.3.1.2 Incineration grate 36 2.3.1.2.1 Rocking grates 37 2.3.1.2.2 Reciprocating grates . 37 2.3.1.2.3 Travelling grates 38 2.3.1.2.4 Roller grates . 38 2.3.1.2.5 Cooled grates . 38 2.3.1.3 Bottom ash discharger . 38 2.3.1.4 Incineration chamber and boiler 39 2.3.1.5 Incineration air feeding . 41 2.3.1.6 Auxiliary burner 42 2.3.1.7 Incineration temperature, residence time, minimum oxygen content 42xvi Waste Incineration 2.3.1.8 Sewage sludge incineration in MSWI plants .42 2.3.1.9 Addition of clinical waste to a municipal waste incinerator 43 2.3.2 Rotary kilns .44 2.3.2.1 Kilns and post combustion chambers for hazardous waste incineration 45 2.3.2.2 Drum kiln with post-combustion chamber for hazardous waste incineration 45 2.3.3 Fluidised beds 47 2.3.3.1 Stationary (or bubbling) fluidised bed incineration .49 2.3.3.2 Circulating fluidised bed (CFB) for sewage sludge .51 2.3.3.3 Spreader-stoker furnace .51 2.3.3.4 Rotating fluidised bed 52 2.3.4 Pyrolysis and gasification systems 52 2.3.4.1 Introduction to gasification and pyrolysis 52 2.3.4.2 Gasification 53 2.3.4.2.1 Examples of gasification processes 55 2.3.4.3 Pyrolysis 56 2.3.4.3.1 Example of a pyrolysis process 58 2.3.4.3.2 Example of pyrolysis in combination with a power plant 59 2.3.4.4 Combination processes 61 2.3.4.4.1 Pyrolysis – incineration 61 2.3.4.4.2 Pyrolysis – gasification .64 2.3.4.4.3 Gasification – combustion 66 2.3.5 Other techniques 67 2.3.5.1 Stepped and static hearth furnaces .67 2.3.5.2 Multiple hearth furnaces 67 2.3.5.3 Multiple hearth fluidised bed furnace 70 2.3.5.4 Modular systems 70 2.3.5.5 Incineration chambers for liquid and gaseous wastes 71 2.3.5.6 Cycloid incineration chamber for sewage sludge 72 2.3.5.7 Example of process for the incineration of liquid and gaseous chlorinated wastes with HCl recovery 72 2.3.5.8 Example of a process for the incineration of highly chlorinated liquid wastes with chlorine recycling 74 2.3.5.9 Waste water incineration .75 2.3.5.10 Plasma technologies .77 2.3.5.11 Various techniques for sewage sludge incineration .79 2.4 The energy recovery stage 81 2.4.1 Introduction and general principles .81 2.4.2 External factors affecting energy efficiency 82 2.4.2.1 Waste type and nature 82 2.4.2.2 Influence of plant location on energy recovery .84 2.4.2.3 Factors taken into account when selecting the design of the energy cycle 86 2.4.3 Energy efficiency of waste incinerators 87 2.4.3.1 Energy inputs to waste incinerators .87 2.4.3.2 Energy outputs from waste incinerators 88 2.4.4 Applied techniques for improving energy recovery 88 2.4.4.1 Waste feed pretreatment 88 2.4.4.2 Boilers and heat transfer 89 2.4.4.2.1 Corrosion in boilers 91 2.4.4.3 Combustion air preheating .93 2.4.4.4 Water cooled grates .93 2.4.4.5 Flue-gas condensation .93 2.4.4.6 Heat pumps 95 2.4.4.6.1 Compressor driven heat pumps 95 2.4.4.6.2 Absorption heat pumps .96 2.4.4.6.3 Open heat pumps 96 2.4.4.6.4 Example data of different heat pumps 96 2.4.4.7 Flue-gas re-circulation .97 2.4.4.8 Reheating of flue-gases to the operation temperature FGT devices 97 2.4.4.9 Plume visibility reduction 97 2.4.4.10 Steam-water cycle improvements: effect on efficiency and other aspects .97 2.4.5 Steam generators and quench cooling for hazardous waste incinerators .98 2.4.6 Examples of energy recovery from fluidised bed incinerators 99 2.5 Applied flue-gas treatment and control systems .100Waste Incineration xvii 2.5.1 Summary of the application of FGT techniques . 100 2.5.2 Overview of overall combined FGT system options 102 2.5.3 Techniques for reducing particulate emissions . 102 2.5.3.1 Electrostatic precipitators 103 2.5.3.2 Wet electrostatic precipitators . 103 2.5.3.3 Condensation electrostatic precipitators 104 2.5.3.4 Ionisation wet scrubbers 105 2.5.3.5 Fabric filters 105 2.5.3.6 Cyclones and multi-cyclones . 106 2.5.4 Techniques for the reduction of acid gases (e.g. HCl, HF and SOX emissions) 107 2.5.4.1 Removal of sulphur dioxide and halogens 107 2.5.4.2 Direct desulphurisation . 110 2.5.5 Techniques for the reduction of emissions of oxides of nitrogen . 111 2.5.5.1 Primary techniques for NOX reduction 111 2.5.5.1.1 Air supply, gas mixing and temperature control 111 2.5.5.1.2 Flue-Gas Recirculation (FGR) . 112 2.5.5.1.3 Oxygen injection 112 2.5.5.1.4 Staged combustion . 112 2.5.5.1.5 Natural gas injection (re-burn) . 112 2.5.5.1.6 Injection of water into furnace/flame . 112 2.5.5.2 Secondary techniques for NOX reduction 112 2.5.5.2.1 Selective Non-Catalytic Reduction (SNCR) process . 113 2.5.5.2.2 Selective Catalytic Reduction (SCR) process 115 2.5.6 Techniques for the reduction of mercury emissions . 116 2.5.6.1 Primary techniques 116 2.5.6.2 Secondary techniques 116 2.5.7 Techniques for the reduction of other emissions of heavy metals 117 2.5.8 Techniques for the reduction of emissions of organic carbon compounds . 117 2.5.8.1 Adsorption on activated carbon reagents in an entrained flow system 118 2.5.8.2 SCR systems 118 2.5.8.3 Catalytic bag filters . 118 2.5.8.4 Re-burn of carbon adsorbents 119 2.5.8.5 Use of carbon impregnated plastics for PCDD/F adsorption 119 2.5.8.6 Static bed filters . 120 2.5.8.7 Rapid quenching of flue-gases 120 2.5.9 Reduction of greenhouse gases (CO2, N2O) . 121 2.5.9.1 Prevention of nitrous oxide emissions . 121 2.5.10 Overview of flue-gas treatments applied at hazardous waste incinerators 121 2.5.11 Flue-gas treatment for sludge incinerators 122 2.6 Waste water treatment and control techniques . 123 2.6.1 Potential sources of waste water . 123 2.6.2 Basic design principles for waste water control 124 2.6.3 Influence of flue-gas treatment systems on waste water . 125 2.6.4 Processing of waste water from wet flue-gas treatment systems 126 2.6.4.1 Physico-chemical treatment 126 2.6.4.2 Application of sulphides 127 2.6.4.3 Application of membrane technology . 128 2.6.4.4 Stripping of ammonia 128 2.6.4.5 Separate treatment of waste water from the first and the last steps of the scrubber system 128 2.6.4.6 Anaerobic biological treatment (conversion of sulphates into elementary sulphur) . 129 2.6.4.7 Evaporation systems for process waste water . 129 2.6.4.7.1 In-line evaporation . 129 2.6.4.7.2 Separate evaporation 130 2.6.4.8 Example of process producing hydrochloric acid with downstream cleaning 131 2.6.5 Waste water treatment at hazardous waste incinerators 131 2.7 Solid residue treatment and control techniques 133 2.7.1 Types of solid residues . 133 2.7.2 Treatment and re-cycling of solid residues . 135 2.7.3 Treatments applied to Flue-gas treatment residues . 136 2.7.3.1 Solidification and chemical stabilisation of FGT residues 136 2.7.3.2 Thermal treatment of FGT residues 136 2.7.3.3 Extraction and separation of FGT residues . 137xviii Waste Incineration 2.7.3.4 Chemical stabilisation of FGT residues .138 2.7.3.5 Other methods or practices for FGT residues 138 2.8 Monitoring and control techniques .138 2.8.1 Incineration control systems 138 2.8.2 Overview of emissions monitoring carried out .139 2.8.3 Experiences with continuous sampling of dioxin emissions .140 2.8.4 Experiences with continuous measurement of mercury emissions 141 2.8.5 Overview of safety devices and measures .142 3 EMISSIONS AND CONSUMPTIONS .143 3.1 Introduction 143 3.1.1 Substance partitioning in waste incineration .144 3.1.2 Examples of the dioxin balance for MSWI .146 3.1.3 Composition of crude flue-gas in waste incineration plants 147 3.1.4 Emissions of gases relevant to climate change 149 3.2 Emissions to air 150 3.2.1 Substances emitted to air .150 3.2.2 Municipal waste incineration plants 156 3.2.2.1 Summary data for emissions to air from MSWI 156 3.2.2.2 European air emissions survey data for MSWI .157 3.2.2.3 Emissions to air from fluidised bed incinerators .162 3.2.3 Hazardous waste incineration plants .162 3.2.3.1 Summary data of the emissions to air from HWI 162 3.2.3.2 European air emissions survey data for HWI 163 3.3 Emissions to water 174 3.3.1 Volumes of waste water arising from flue-gas treatment 174 3.3.2 Other potential sources of waste water from waste incineration plants .175 3.3.3 Installations free of process water releases 175 3.3.4 Plants with physico–chemical waste water treatment 175 3.3.5 Hazardous waste incineration plants - European survey data 179 3.3.5.1 General overview of emissions to water from European HWI 179 3.3.5.2 Overview by parameter of emissions to water from European HWI .180 3.4 Solid residues 186 3.4.1 Mass streams of solid residues in MSWI 186 3.4.2 Bottom ash composition and leachability 187 3.5 Energy consumption and production 192 3.5.1 Energy efficiency calculation for waste incineration installations 193 3.5.2 Waste net calorific value calculation .193 3.5.3 Equivalence factors .194 3.5.4 Data on the recovery of energy from waste .194 3.5.4.1 Electricity recovery data 195 3.5.4.2 Heat recovery data .196 3.5.4.3 Combined heat and power data 197 3.5.4.4 Boiler conversion efficiency data 197 3.5.5 Data on the consumption of energy by the process .198 3.5.6 Data comparing energy required by, and output from, the installation .199 3.6 Noise .201 3.7 Other operating resources .202 3.7.1 Water .202 3.7.2 Other operating resources 203 3.7.2.1 Neutralisers 203 3.7.2.2 NOX removal agents 203 3.7.2.3 Fuel oil and natural gas 204 3.7.2.4 Merchant hazardous waste incinerator plant survey data .204 4 TECHNIQUES TO CONSIDER IN THE DETERMINATION OF BAT 205 4.1 General practices applied before the thermal treatment stage 207 4.1.1 Suitability of process design for the waste(s) received 207 4.1.2 General housekeeping measures 208 4.1.3 Quality control of incoming wastes .208 4.1.3.1 Establishing installation input limitations and identifying key risks .208 4.1.3.2 Communication with waste suppliers to improve incoming waste quality control 210 4.1.3.3 Controlling waste feed quality on the incinerator site .211 4.1.3.4 Checking, sampling and testing incoming wastes 212Waste Incineration xix 4.1.3.5 Detectors for radioactive materials 214 4.1.4 Waste storage 215 4.1.4.1 Sealed surfaces, controlled drainage and weatherproofing . 215 4.1.4.2 Management of storage times 217 4.1.4.3 Baling or other containment of solid waste . 218 4.1.4.4 Extraction of incineration air from storage areas for odour, dust and fugitive release control . 219 4.1.4.5 Segregation of waste types for safe processing . 221 4.1.4.6 Individual labelling of contained waste loads . 222 4.1.4.7 The use of fire detection and control systems . 223 4.1.5 Pretreatment of incoming waste 224 4.1.5.1 Pretreatment and mixing of wastes . 224 4.1.5.2 Shredding of mixed municipal wastes . 227 4.1.5.3 Shredding of drummed and packaged hazardous wastes 228 4.1.5.4 Feed equalising control system for solid hazardous wastes 229 4.1.5.5 Pre-combustion removal of recyclable metals . 231 4.1.5.6 Pretreatment and targeted preparation of solid waste for combustion . 232 4.1.6 Waste transfer and loading 233 4.1.6.1 Positioning and view of operator . 233 4.1.6.2 Provision of storage space for items removed from the waste 233 4.1.6.3 Direct injection of liquid and gaseous hazardous wastes in rotary kilns . 233 4.1.6.4 Reduction of air ingress into the combustion chamber during loading . 234 4.2 Thermal processing 235 4.2.1 Combustion technology selection . 235 4.2.2 Use of flow modelling 240 4.2.3 Combustion chamber design features . 241 4.2.4 Design to increase turbulence in the secondary combustion chamber 243 4.2.5 Use of continuous rather than batch operation 244 4.2.6 Selection and use of suitable combustion control systems and parameters 245 4.2.7 Use of infrared cameras for combustion monitoring and control . 247 4.2.8 Optimisation of air supply stoichiometry 249 4.2.9 Primary air supply optimisation and distribution 250 4.2.10 Preheating of primary and secondary air 252 4.2.11 Secondary air injection, optimisation and distribution 253 4.2.12 Replacement of part of the secondary air with re-circulated flue-gas . 254 4.2.13 Application of oxygen enriched air . 256 4.2.14 Cooling of grates . 258 4.2.15 Water cooling of rotary kilns 260 4.2.16 Higher temperature incineration (slagging) 261 4.2.17 Increased agitation and residence time of the waste in the furnace 263 4.2.18 Adjustment of throughput to maintain good burnout and combustion conditions 265 4.2.19 Optimisation of time, temperature, turbulence of gases in the combustion zone, and oxygen concentrations 266 4.2.20 Use of automatically operated auxiliary burners 269 4.2.21 Reduction of grate riddling rate and/or return of cooled riddlings to the combustion chamber . 270 4.2.22 Protection of furnace membrane walls and boiler first pass with refractory or other materials 272 4.2.23 Use of low gas velocities in the furnace and the inclusion of empty passes before the boiler convection section 274 4.2.24 Determination of calorific value of the waste and its use as a combustion control parameter 275 4.2.25 Low-NOX burners for liquid wastes 276 4.2.26 Fluidised bed gasification . 276 4.2.27 High temperature combustion of gasification syngas with ash melting 279 4.3 Energy recovery . 281 4.3.1 Optimisation of overall energy efficiency and energy recovery . 281 4.3.2 Energy loss reduction: flue-gas losses 288 4.3.3 Increasing burnout of the waste 290 4.3.4 Reducing excess air volumes 290 4.3.5 Other energy loss reduction measures 291 4.3.6 Reduction of overall process energy consumption . 292 4.3.7 Selection of turbine . 294xx Waste Incineration 4.3.8 Increased steam parameters and application of special materials to decrease corrosion in boilers 296 4.3.9 Reduction of condenser pressure (i.e. improve vacuum) .299 4.3.10 Selection of cooling system .301 4.3.11 Optimisation of boiler architecture 302 4.3.12 Use of an integral furnace - boiler .304 4.3.13 Use of water walls in the first (empty) pass 305 4.3.14 Use of a platten type superheater .305 4.3.15 Reduction of flue-gas temperatures after the boiler .306 4.3.16 Use of flue-gas condensation scrubbers 308 4.3.17 Use of heat pumps to increase heat recovery .309 4.3.18 Special configurations of the water/steam cycle with external power plants 311 4.3.19 Efficient cleaning of the convection bundles .313 4.4 Flue-gas treatment 315 4.4.1 Factors to consider when selecting flue-gas treatment systems .315 4.4.1.1 General factors .315 4.4.1.2 Energy optimisation .316 4.4.1.3 Overall optimisation and the “whole system” approach 316 4.4.1.4 Technique selection for existing or new installations 316 4.4.2 Reduction of dust emissions 317 4.4.2.1 Application of a pre-dedusting stage before other flue-gas treatments 317 4.4.2.2 Application of an additional flue-gas polishing system .321 4.4.2.3 Application of double bag filtration .324 4.4.2.4 Selection of bag filter materials .326 4.4.3 Reduction of acid gas emissions 328 4.4.3.1 Wet scrubbing systems 328 4.4.3.2 Semi-wet scrubbing systems 332 4.4.3.3 Intermediate systems with some water addition and residue recirculation (flash dry systems) .336 4.4.3.4 Dry FGT systems .339 4.4.3.5 Selection of alkaline reagent 342 4.4.3.6 Addition of wet scrubbing as a flue-gas polishing system after other FGT processes .344 4.4.3.7 Recirculation of FGT residues in the FGT system .345 4.4.3.8 Direct addition of alkaline reagents to the waste (direct desulphurisation) .347 4.4.3.9 Use of acid gas monitoring for FGT process optimisation 348 4.4.4 Reduction in the emissions of nitrogen oxides 349 4.4.4.1 Selective catalytic reduction (SCR) .349 4.4.4.2 Selective non-catalytic reduction (SNCR) .355 4.4.4.3 Optimisation of reagent selection for SNCR NOX reduction .359 4.4.4.4 Replacement of secondary air with re-circulated flue-gas .360 4.4.5 Reduction of PCDD/F emissions .360 4.4.5.1 Primary techniques for prevention of PCDD/F 361 4.4.5.2 Prevention of reformation of PCDD/F in the FGT system 361 4.4.5.3 Destruction of PCDD/F using Selective Catalytic Reduction (SCR) .363 4.4.5.4 Destruction of PCDD/F using catalytic filter bags 365 4.4.5.5 Destruction of PCDD/F by re-burn of adsorbents 367 4.4.5.6 Adsorption of PCDD/F by activated carbon injection or other reagents .368 4.4.5.7 Adsorption of PCDD/F in static beds 369 4.4.5.8 Use of carbon impregnated materials for PCDD/F adsorption in wet scrubbers .372 4.4.5.9 Use of carbon slurries in wet scrubbers .373 4.4.6 Reduction of mercury emissions .374 4.4.6.1 Low pH wet scrubbing and additive addition 374 4.4.6.2 Activated carbon injection for Hg adsorption 376 4.4.6.3 Use of condensing scrubbers for flue-gas polishing 378 4.4.6.4 Separation of mercury using a resin filter 380 4.4.6.5 Chlorite injection for elemental Hg control .380 4.4.6.6 Addition of hydrogen peroxide to wet scrubbers .381 4.4.6.7 Use of static activated carbon or coke filters .382 4.4.7 Other techniques and substances .382 4.4.7.1 Use of specific reagents for iodine and bromine reduction 382 4.5 Waste water treatment and control .384 4.5.1 General 384Waste Incineration xxi 4.5.2 Application of optimal incineration technology . 384 4.5.3 Application of waste water free gas cleaning technology . 384 4.5.4 Re-circulation of polluted waste water in wet gas cleaning systems 386 4.5.5 Additional cooling of feed water of wet gas cleaning systems . 386 4.5.6 Use of boiler drain water as a water supply for scrubbers 387 4.5.7 Treatment of laboratory waste water in the scrubber 387 4.5.8 Re-circulation of effluents to the process in place of their discharge . 388 4.5.9 Separate discharge of rainwater from roofs and other clean surfaces . 389 4.5.10 Provision of storage/buffering capacity for waste water . 390 4.5.11 Application of physico-chemical treatment to wet scrubber effluents and other contaminated waste water from the plant 391 4.5.12 Ammonia removal from effluents . 392 4.5.13 Separate treatment of effluents arising from different wet scrubbing stages 393 4.5.14 Evaporation of wet scrubber effluent in the incineration process . 394 4.5.15 Separate evaporation of wet scrubber effluent 394 4.5.16 Recovery of hydrochloric acid from wet scrubber effluents . 394 4.5.17 Recovery of gypsum from wet scrubber effluent 395 4.6 Treatment techniques for solid residues . 397 4.6.1 Improving the burnout of bottom ash . 397 4.6.2 Segregation of the bottom ash from flue-gas treatment residues 399 4.6.3 Separation of the dust removal stage from other flue-gas treatments . 400 4.6.4 Bottom ash - separation of metals . 401 4.6.5 Bottom ash screening and crushing 402 4.6.6 Bottom ash treatment using ageing . 403 4.6.7 Bottom ash treatment using dry treatment systems . 405 4.6.8 Bottom ash treatment using wet treatment systems 408 4.6.9 Bottom ash treatment using thermal systems 410 4.6.10 High temperature (slagging) rotary kiln 412 4.6.11 FGT residue treatments . 412 4.6.11.1 Cement solidification of FGT residues 412 4.6.11.2 Vitrification and melting of FGT residues 414 4.6.11.3 Acid extraction of boiler and fly ash . 417 4.6.11.4 Treatment of FGT residues arising from dry sodium bicarbonate FGT process for use in the soda ash industry . 418 4.6.11.5 Treatment of FGT residues arising from dry sodium bicarbonate FGT process using hydraulic binders . 420 4.7 Noise 421 4.8 Environmental management tools 422 4.9 Good practice for public awareness and communication . 429 5 BEST AVAILABLE TECHNIQUES . 431 5.1 Generic BAT for all waste incineration . 434 5.2 Specific BAT for municipal waste incineration . 450 5.3 Specific BAT for pretreated or selected municipal waste incineration 451 5.4 Specific BAT for hazardous waste incineration . 452 5.5 Specific BAT for sewage sludge incineration 453 5.6 Specific BAT for clinical waste incineration . 453 6 EMERGING TECHNIQUES . 455 6.1 Use of steam as a spraying agent in post combustion chamber burners instead of air . 455 6.2 Application involving the reheating of turbine steam 455 6.3 Other measures in the crude flue-gas area for reducing dioxin emissions . 456 6.4 Oil scrubber for the reduction of polyhalogenated aromatics and polyaromatic hydrocarbons (PAHs) in the flue-gases from incineration plants . 456 6.5 Use of CO2 in flue-gases for the production of sodium carbonate . 457 6.6 Increased bed temperature, combustion control and oxygen addition in a grate incinerator 458 6.7 The PECK combination process for MSW treatment 459 6.8 FeSO4 stabilisation of FGT residues 463 6.9 CO2 stabilisation of FGT residues 464 6.10 Overview of some other emerging FGT residue treatment techniques 465 6.11 Application of membrane technology for use in waste water treatment plants for wet scrubber effluents 466 6.12 Combined dry sodium bicarbonate + SCR + scrubber FGT systems . 466xxii Waste Incineration 7 CONCLUDING REMARKS .471 7.1 Timing of the work .471 7.2 Sources of information and information gaps .471 7.3 Degree of Consensus reached .474 7.4 Other specific notes and issues .474 7.4.1 Existence of installations with operational emission levels below those concluded as BAT .474 7.4.2 Comprehensiveness of Table 5.3 on selection criteria for FGT systems (BAT 37) 474 7.4.3 Use of dry FGT systems at certain hazardous waste incinerators (BAT75) 475 7.4.4 Impacts of energy pricing and policies on energy efficiency 475 7.4.5 Competition and regulatory impacts across waste treating industrial sectors .475 7.4.6 Development and implementation of waste strategies 476 7.4.7 Markets and standards for bottom ash and other residues .476 7.4.8 Co-ordinated education and demonstration of health/environmental impacts .477 7.5 Suggested topics for future R&D projects 477 8 REFERENCES .479 9 GLOSSARY 483 10 ANNEXES .489 10.1 Economic overview of MSWI - Member State information .489 10.2 Economic overview – some technological aspects of MSWI .503 10.2.1 Discharge and storage costs for MSWI .505 10.2.2 Firing system and boiler costs for MSWI 506 10.2.3 Water-steam cycle costs for MSWI .507 10.2.4 Costs for some flue-gas treatment combinations used in MSWI .513 10.2.4.1 Dry flue-gas cleaning .514 10.2.4.2 Absorption and adsorption plants for the separation of HCl, HF and SO2 516 10.2.4.3 NaOH scrubber 518 10.2.4.4 Secondary NOX reduction using SCR or SNCR 519 10.2.4.5 Post treatment flue-gas polishing systems .520 10.2.5 Cost estimations for some complete MSWI plants 521 10.2.6 Costs of fluidised bed combustion for MSW 526 10.2.7 Gasification and pyrolysis system costs for MSW 528 10.3 Example installation descriptions .530 10.3.1 Examples of municipal waste incineration 531 10.3.1.1 Grate incinerator with SCR and steam distribution .531 10.3.1.2 Grate incinerator with SCR and CHP 536 10.3.1.3 Grate incinerator with SCR, CHP and bottom ash treatment .542 10.3.1.4 Grate incinerator with SNCR de-NOX, combined double filtration and wet scrubbing .546 10.3.1.5 Grate incinerator with semi-wet FGT, active carbon injection, ash recirculation, bottom ash treatment and (mainly) electricity generation 549 10.3.1.6 Grate incinerator with SNCR de-NOX, semi-wet FGT, active carbon injection and high steam parameters (60 bar/380 °C) electricity generation .550 10.3.1.7 Grate incinerator with SNCR (NH3), semi-wet lime, active carbon and electricity generation 551 10.3.1.8 Grate incinerator with SNCR (NH3), semi-wet lime, active carbon and electricity generation 552 10.3.2 Examples of the hazardous wastes installations 554 10.3.2.1 Rotary kiln with heat recovery, SNCR, EP, wet scrubber and static coke filter 554 10.3.2.2 Rotary kiln with SCR, EP, wet scrubber and static carbon filter .559 10.3.2.3 Rotary kiln with SNCR (urea), dry lime FGT, double bag filtration and dioxin absorption 561 10.3.3 Examples of sewage sludge installations .562 10.3.3.1 Bubbling fluidised bed with heat recovery, SNCR, EP, wet scrubbing and static coke filter .562 10.3.3.2 Bubbling FB with CHP, SNCR, flue-gas re-circulation, EP, wet scrubbing and bag filters with coke/calcium carbonate injection 565 10.3.3.3 Bubbling FB Plant with CHP, EP and wet scrubbing 567 10.3.4 Examples of combined incineration of various wastes 568 10.3.4.1 Circulating FB for selected/pretreated wastes with heat recovery, dry and wet FGT, SCR and ash treatment .568Waste Incineration xxiii 10.3.4.2 Fluidized bed plant for selected hazardous and non-hazardous wastes with heat recovery, EP, fabric filter, wet scrubber and SCR . 573 10.3.4.3 Water cooled grate furnace with CHP, cyclone de-dusting, SNCR and high dust SCR de-NOX, and dry fabric filter . 577 10.3.4.4 Grate incinerator treating MSW, SS & CW with SNCR (urea), dry Na bicarbonate FGT, activated C injection and electricity generation . 580 10.3.4.5 Grate incinerator treating MSW and industrial waste with EP, wet scrubbing, effluent evaporation, SCR and high pressure steam electricity generation . 582 10.3.4.6 Grate incinerator treating MW, IW, SS and waste sorting refuse with SNCR, EP, wet scrubbing (on-line evaporation of effluent), bag filters and CHP . 583 10.3.4.7 Grate incinerator treating MSW, industrial and commercial waste with SNCR and semi-wet FGT and 20 bar 260 °C to district heating network . 585 10.3.4.8 Grate incinerator treating MSW, IW and clinical waste with SNCR, dry FGT and electricity generation . 587 10.3.4.9 Grate incinerator treating MSW, waste sorting residues and sludges with SNCR, dry FGT and heat supply to DH and local electricity plant . 588 10.4 Energy calculation methodology and example calculation 590 10.4.1 General explanations of terms and system boundary of the energy calculation . 590 10.4.2 Example of NCV calculation used by energy sub-group 591 10.4.3 Basic operational data for three examples of the energy calculation 592 10.4.4 Energy calculation formulas with basic operational data for three examples of the energy calculation . 595 10.4.5 Equations to calculate the plant efficiency (Pl ef) 599 10.5 Example of a multi-criteria assessment used for the selection of FGT systems . 601xxiv Waste Incineration List of figures Figure 1.1: Municipal waste incineration capacity per capita .5 Figure 1.2: Bottom ash recycled and deposited from MSWI in 1999 .11 Figure 1.3: Energy production by municipal waste incinerators in Europe (1999) 12 Figure 2.1: Example layout of a municipal solid waste incineration plant .19 Figure 2.2: Example of some hazardous waste pretreatment systems used at some merchant HWI 28 Figure 2.3: Grate, furnace and heat recovery stages of an example municipal waste incineration plant 35 Figure 2.4: Different grate types .37 Figure 2.5: Example of a type of ash remover used at a grate incinerator 39 Figure 2.6: Example of an incineration chamber 40 Figure 2.7: Various furnace designs with differing direction of the flue-gas and waste flow 41 Figure 2.8: Examples of the stages of a clinical waste loading systems used at a municipal waste incinerator .43 Figure 2.9: Schematic of a rotary kiln incineration system 44 Figure 2.10: Drum-type kiln with post-combustion chamber .45 Figure 2.11: Example of a drum-type kiln plant for hazardous waste incineration 47 Figure 2.12: Schematic diagram showing pretreatment of MSW prior to fluidised bed combustion .48 Figure 2.13: Main components of a stationary/bubbling fluidised bed .49 Figure 2.14: Main components of a circulating fluidised bed .51 Figure 2.15: Representation of a packed bed and current flow gasifier 54 Figure 2.16: Slag bath gasifier 55 Figure 2.17: Fluidised bed gasifier with high temperature slagging furnace 56 Figure 2.18: Structure of a pyrolysis plant for municipal waste treatment .57 Figure 2.19: Process scheme of ATM’s ‘pyrolysis’-unit 59 Figure 2.20: Energy balance and weight assessment of the ConTherm plant .60 Figure 2.21: Pyrolysis on a grate with directly connected high-temperature incineration 62 Figure 2.22: The RCP process 62 Figure 2.23: Example of a clinical waste pyrolysis-incineration plant, ZAVIN, Netherlands 64 Figure 2.24: Schematic diagram of a push pyrolyser (example shown operated by Thermoselect) .65 Figure 2.25:Combined fluidised bed gasification and high temperature combustion process 66 Figure 2.26: Principle function of a multiple hearth furnace 68 Figure 2.27: Example of a sewage sludge incineration plant with a multiple hearth furnace .69 Figure 2.28: Principle function of a multiple hearth fluidised bed furnace 70 Figure 2.29: Principle of an incineration chamber for liquid and gaseous wastes 71 Figure 2.30: Illustration of a cycloid furnace 72 Figure 2.31: Diagram of a plant for HCl-extraction from residual gases and liquid halogenated wastes .73 Figure 2.32: Process scheme of a chlorine recycling unit operated by Akzo Nobel .75 Figure 2.33:Example of a waste water incinerator with a waste water evaporation (concentration) unit. .76 Figure 2.34: Process scheme of a caustic water treatment plant operated by AVR 77 Figure 2.35: Graph showing recorded variation in waste NCV at a MSWI over 4 years .83 Figure 2.36: Illustration of individual heat surface areas in a steam generator .89 Figure 2.37: Basic boiler flow systems .90 Figure 2.38: Overview of various boiler systems: horizontal, combination, and, vertical 91 Figure 2.39: Pollution control and additional heat recovery by condensation of flue-gas water vapour at the Stockholm/Hogdalen waste-fired CHP plant 95 Figure 2.40: Overview of potential combinations of FGT systems 102 Figure 2.41: Operating principle of an electrostatic precipitator 103 Figure 2.42: Condensation electrostatic precipitator 104 Figure 2.43: An example of a fabric filter 106 Figure 2.44: Schematic diagram of a dry FGT system with reagent injection to the FG pipe and downstream bag filtration .108 Figure 2.45: Operating principle of a spray absorber .108 Figure 2.46: Diagram of a 2 stage wet scrubber with upstream de-dusting 110 Figure 2.47: Temperature dependence of various NOX formation mechanisms in waste incineration .111 Figure 2.48: SNCR operating principle 113 Figure 2.49: Relationship between NOX reduction, production, ammonia slip and reaction temperature for the SNCR process .114 Figure 2.50: SCR operating principle .115 Figure 2.51: Relationship between Hg emissions and the raw gas chloride content at a hazardous waste incineration plant .117 Figure 2.52: Process scheme for physico-chemical treatment of waste water from a wet flue-gas treatment system .126Waste Incineration xxv Figure 2.53: In-line evaporation of waste water from wet scrubbing . 129 Figure 2.54: Separate evaporation of scrubber effluent from wet scrubbing . 130 Figure 2.55: Overview of applied waste water treatment systems at merchant HWIs . 132 Figure 2.56: Example of a waste water treatment facility in the merchant HWI sector . 133 Figure 3.1: Graph of NOX annual average emissions to air and applied abatement technique at European HWIs 165 Figure 3.2: Graph of annual average dust emissions to air and applied abatement technique at European HWIs 166 Figure 3.3: Graph of HCl annual average emissions to air and applied abatement technique at European HWIs 167 Figure 3.4: Graph of annual average sulphur dioxide emissions to air and applied abatement technique at European HWIs 168 Figure 3.5: Graph of Hg annual average emissions to air and applied abatement technique at European HWIs 170 Figure 3.6: Annual average emissions to air of other metals and applied abatement technique at European HWIs 171 Figure 3.7: Graph of Cd and Tl annual average emissions to air and applied abatement technique at European HWIs 172 Figure 3.8: Graph of PCDD/F annual average emissions to air and applied abatement technique at European HWIs 173 Figure 3.9: CO emission reductions achieved following introduction of pretreatment techniques at a hazardous waste incinerator 174 Figure 3.10: Graph of annual average suspended solid discharges to water and applied abatement technique at European HWIs 181 Figure 3.11: Graph of annual average mercury discharges to water and applied abatement technique at European HWIs 182 Figure 3.12: Graph of annual average discharges of various metals to water at European HWIs 183 Figure 3.13: Graph of annual average Arsenic discharges to water at European HWIs . 183 Figure 3.14: Graph of annual average lead discharges to water at European HWIs 184 Figure 3.15: Graph of annual average Cadmium discharges to water at European HWIs . 184 Figure 3.16: Graph of annual average Chromium discharges to water at European HWIs 184 Figure 3.17: Graph of annual average Copper discharges to water European HWIs . 185 Figure 3.18: Graph of annual average Nickel discharges to water at European HWIs 185 Figure 3.19: Graph of annual average Zinc discharges to water at European HWIs 185 Figure 3.20: Graph showing increase in installation electrical consumption with increasing waste NCV 199 Figure 4.1: An example of the components of furnace control system 247 Figure 4.2: Basic components of a cyclonic high temperature syngas ash melting furnace . 279 Figure 4.3: Schematic diagram of a “platen” type superheater 305 Figure 4.4: Combination of a waste incineration plant with a gas turbine power plant . 312 Figure 4.5: Municipal waste incineration plant in combination with a coal power plant . 312 Figure 4.6: Diagram showing typical design of a semi-wet FGT system . 332 Figure 4.7: Diagram of an SCR system downstream of non-wet FGT showing typical heat exchange and temperature profiles 351 Figure 4.8: Diagram of an SCR system downstream of a wet FGT system showing additional heat exchange and temperature profiles . 351 Figure 4.9: Effect of ageing on the leachability of selected metals: (left) effect on pH; (right) leaching as a function of pH 405 Figure 6.1: Example of the reheating of steam . 455 Figure 6.2: Schematic of a waste incineration plant with a downstream oil scrubber for dioxin deposition 457 Figure 6.3: Basic components of the PECK process 459 Figure 6.4: Fly ash treatment in the PECK process 460 Figure 6.5: Bottom ash treatment in the PECK process . 460 Figure 6.6: Comparison of metals partitioning between a conventional grate MSWI and the PECK process 461 Figure 6.7: Material flow mass balance for the PECK process 462 Figure 10.1: Water-steam cycle, option 1 508 Figure 10.2: Water-steam cycle, option 2 and 6 . 509 Figure 10.3: Water-steam cycle, option 3 510 Figure 10.4: Water-steam cycle, options 4, 5, 7 and 8 . 510 Figure 10.5: The impact of plant size and energy utilisation on the specific waste treatment costs of new MSWI installations . 522xxvi Waste Incineration Figure 10.6: The impact of varying FGT systems and plant sizes on the treatment costs of new MSWI installations using the same energy utilisation techniques 522 Figure 10.7: Process flow scheme of the waste incineration plant Flötzersteig 531 Figure 10.8: Process flow scheme of the waste incineration plant Spittelau 537 Figure 10.9: Process flow scheme of the waste incineration plant Wels – line 1 .543 Figure 10.10: Process flow scheme of the rotary kilns of the Plant Simmeringer Haide 555 Figure 10.11: Process flow scheme of the fluidised bed reactors of the Plant Simmeringer Haide 562 Figure 10.12: Process flow scheme of AVE-Reststoffverwertung Lenzing .570 Figure 10.13: Process flow scheme of the Fluidised bed reactors at Arnoldstein .574 Figure 10.14: Summary of the energy system inputs and outputs used by BREF ESG 590Waste Incineration xxvii List of tables Table 1.1: Purpose of various components of a waste incinerator . 2 Table 1.2: Amounts of municipal waste (MSW), hazardous waste (HW) and sewage sludge (SS) in EU-15 MSs, and their treatment . 3 Table 1.3: Annual quantities of municipal and hazardous waste arising and the number of incineration plants in some Accession Countries . 4 Table 1.4: Geographical distribution of incineration plants for municipal, hazardous and sewage sludge waste . 4 Table 1.5: Average MSW incineration plant capacity by country . 5 Table 1.6: Typical throughput ranges of thermal treatment technologies 6 Table 1.7: Typical composition of waste in Germany 8 Table 1.8: Gate fees in European MSW and HW incineration plants 14 Table 1.9: Comparative costs of MSW incineration in different MSs . 15 Table 1.10: Specific investment costs for a new MSWI installation related to the annual capacity and some types of FGT in Germany . 15 Table 1.11: Example of the comparative individual cost elements for MSW and HW incineration plants16 Table 2.1: Typical reaction conditions and products from pyrolysis, gasification and incineration processes . 20 Table 2.2: Prime impact of waste selection and pretreatment on residual waste . 21 Table 2.3: Summary of the differences between operators in the HWI market . 24 Table 2.4: Average composition of dewatered communal sewage sludge after dewatering 29 Table 2.5: Summary of the current successful application of thermal treatment techniques to the main waste types at dedicated installations . 34 Table 2.6: Properties of various RDF (Refuse Derived Fuel) fractions treated in fluidised beds. . 48 Table 2.7: Main operational criteria for stationary fluidised beds 50 Table 2.8: Operational criteria for a multiple hearth furnace . 69 Table 2.9: Comparison of furnace systems for sewage sludge incineration . 80 Table 2.10: Ranges and typical net calorific values for some incinerator input wastes . 82 Table 2.11: Calculated NCV values for waste treated at 50 European MSWI plants 83 Table 2.12: Energy potential conversion efficiencies for different types of waste incineration plants 84 Table 2.13: Factors taken into account when selecting the design of the energy cycle for waste incineration plants 86 Table 2.14: Example data showing the variation in heat and electricity output when using various different types of heat pumps . 96 Table 2.15: Steam-water cycle improvements: effect on efficiency and other aspects. . 98 Table 2.16: Summary of the main differences between quench cooling and heat recovery . 99 Table 2.17: Summary of the main applied FGT systems for MSWIs in Europe in 2000/2001 . 101 Table 2.18: Tested continuous working measuring devices for emission measurements of mercury 141 Table 3.1: Distribution of various substances in an example MSWI installation (in mass %) . 145 Table 3.2: Percentage (%) distribution of heavy metals in a hazardous waste incineration process 145 Table 3.3: Average operational conditions during partitioning tests on a HWI installation 146 Table 3.4: PCDD/PCDF balance for a municipal waste incineration plant in Germany 146 Table 3.5: Example PCDD/F load data for an MSWI in France 147 Table 3.6: Flue-gas concentrations after the boiler (crude flue-gas) at various waste incineration plants (O2 reference value 11 %) 148 Table 3.7: Total emissions relevant to climate change in Germany in the year 1999 compared with those arising form waste incineration 150 Table 3.8: Range of clean gas operation emissions levels reported from some European MSWI plants. 156 Table 3.9: Operational emission levels to air from MSWI expressed per tonne of MSW incinerated . 157 Table 3.10: HCl emissions survey of European MSWIs 157 Table 3.11: HF emissions survey of European MSWIs . 158 Table 3.12: Sulphur dioxide emissions survey of European MSWIs . 158 Table 3.13: Dust emissions survey of European MSWIs . 159 Table 3.14 Nitrogen oxides emissions survey of European MSWIs 159 Table 3.15: Total organic carbon emissions survey of European MSWIs . 159 Table 3.16: PCDD/F (TEQ) emissions survey of European MSWIs . 160 Table 3.17: Mercury emissions survey of European MSWIs . 160 Table 3.18: Combined Cd and Hg emissions of selected MSWIs in France 161 Table 3.19: Emission results and techniques applied for Hg control at European MSWIs 161 Table 3.20: Typical range of clean gas emissions to air from hazardous waste incineration plants 162xxviii Waste Incineration Table 3.21: Survey data of the annual average emissions to air from hazardous waste incinerators in Europe .163 Table 3.22: Survey data of mass flow and annual sector emissions to air from merchant hazardous waste incinerators in Europe .164 Table 3.23: Typical values of the amount of scrubbing water arising from FGT at waste incineration plants treating low chlorine content wastes .174 Table 3.24: Other possible waste water sources, and their approximate quantities, from waste incineration plants .175 Table 3.25: Typical contamination of waste water from wet FGT facilities of waste incineration plants before treatment 176 Table 3.26: Releases to surface water and sewers from Dutch waste incinerators in 1999 177 Table 3.27: Waste water quality (after treatment with Trimercaptotriazine) - Comparison between raw and treated waste water and various standards 178 Table 3.28: Annual average range of concentrations of the emissions to water after treatment from merchant hazardous waste installations that discharge waste water .179 Table 3.29: Mass flows of the emissions to water from surveyed merchant HWIs in Europe .180 Table 3.30: Typical data on the quantities of residues arising from municipal waste incineration plants. 186 Table 3.31: Mass streams of solid residues from MSWI expressed per tonne of MSW incinerated 187 Table 3.32: Concentration ranges of organic compounds in bottom, boiler and filter ashes 187 Table 3.33: PCDD/F concentrations in various MSWI incineration residues in NL (data 2000 – 2004).187 Table 3.34: Range of PCDD/F concentrations in MSWI residues (excluding peak high and low values) 188 Table 3.35: Leaching properties of mechanically treated bottom ash, measured using NEN7343 .189 Table 3.36: Quantities of the main waste streams produced by HWI (European survey data) .190 Table 3.37: Typical leaching values of bottom ash from hazardous waste incineration plants, measured using DIN-S4 190 Table 3.38: Some factors and their influence on energy recovery options .192 Table 3.39: Energy equivalence conversion factors .194 Table 3.40: Electricity production and export rates per tonne of MSW .196 Table 3.41: Electricity production and export data per tonne of MSW for MSWI in France .196 Table 3.42: Heat production and export rates per tonne of MSW 196 Table 3.43: Heat production and export rates per tonnes of MSW for MSWI in France 196 Table 3.44: Average CHP percentage efficiency (calculated as energy equivalents) for 50 MSWI plants 197 Table 3.45: Average CHP recovery values per tonne of MSW in MSWI in France 197 Table 3.46: Survey data of MSWI boiler efficiencies .197 Table 3.47: Electricity, heat and total energy demand data for 50 surveyed European MSWI per tonne of waste treated 198 Table 3.48: Ratio of exported and consumed energy for various waste incinerators 200 Table 3.49: Sources of noise at waste incineration plants 201 Table 3.50: Stoichiometric calculation of amounts of lime used for absorption during flue-gas cleaning (reactants expressed at 100 % concentration and purity) 203 Table 3.51: Amount of additives used by merchant hazardous waste incineration processes 204 Table 4.1: Organisation chart for the information in Chapter 4 205 Table 4.2: Information breakdown for each technique described in this Chapter 4 206 Table 4.3: Some checking and sampling techniques applied to various waste types 213 Table 4.4: Some examples of applied storage techniques for various waste types .216 Table 4.5: Main techniques for reducing fugitive releases of odour, and GHG emissions .220 Table 4.6: Some segregation techniques applied for various waste types 221 Table 4.7: A comparison of combustion and thermal treatment technologies and factors affecting their applicability and operational suitability (table 1/3) .236 Table 4.8: A comparison of combustion and thermal treatment technologies and factors affecting their applicability and operational suitability (table 2/3) .237 Table 4.9: A comparison of combustion and thermal treatment technologies and factors affecting their applicability and operational suitability (table 3/3) .239 Table 4.10: A comparison of the features of some different furnace geometries .242 Table 4.11: Crude flue-gas measurements at a test plant under normal operation, with IR camera and O2 conditioning 249 Table 4.12: Some combustion specifications applied to incineration .266 Table 4.13: Relationship between nitrous oxide emissions and process temperatures for a bubbling fluidised bed plant burning sewage sludge .267 Table 4.14: Estimated cost impacts of some alterations to combustion parameters .269Waste Incineration xxix Table 4.15: TWG energy sub-group survey data for specific energy flows at some European MSWIs per tonne of waste treated . 285 Table 4.16: Techniques for the reduction of various energy losses at WI plants . 291 Table 4.17: Plant throughput and total process energy demand for MSWI in Germany 293 Table 4.18: Example energy outputs and income at various steam pressures for a CHP MSWI using elevated steam pressures . 298 Table 4.19: Relationship between the additional energy efficiency and the cooling medium (district heating) return temperature 308 Table 4.20: Cross-media effects associated with the use of various pre-dedusters 318 Table 4.21: Operational data associated with the use of pre-dedusting systems 319 Table 4.22: A comparison of dust removal systems . 320 Table 4.23: Assessment of the applicability of pre-dedusting 320 Table 4.24: Emission levels associated with the use of BF flue-gas polishing systems . 322 Table 4.25: Cross-media effects associated with the use of additional flue-gas polishing . 322 Table 4.26: Operational data associated with the use of flue-gas polishing . 323 Table 4.27: Assessment of the applicability of flue-gas polishing . 323 Table 4.28: Cross-media effects associated with the use of double filtration 325 Table 4.29: Operational data associated with the use of double filtration 325 Table 4.30: Assessment of the applicability of double filtration 326 Table 4.31: Operational information for different bag filter materials . 327 Table 4.32: Emission levels associated with the use of wet scrubbers . 328 Table 4.33: Cross-media effects associated with the use of wet scrubber FGT . 329 Table 4.34: Operational data associated with the use of wet FGT . 330 Table 4.35: Assessment of the applicability of wet FGT . 331 Table 4.36: Estimated investment costs of selected components of wet FGT systems 331 Table 4.37: Emission levels associated with the use of wet scrubbers . 332 Table 4.38: Cross-media effects associated with the use of semi-wet acid gas treatment 333 Table 4.39: Operational data associated with the use of semi-wet FGT 334 Table 4.40: Assessment of the applicability of semi-wet FGT 335 Table 4.41: Estimated investment costs of selected components of typical semi-wet FGT systems . 335 Table 4.42: Emission levels associated with the use of flash dry FGT 336 Table 4.43: Cross-media effects associated with the use of flash dry systems 337 Table 4.44: Operational data associated with the use of flash dry FGT 338 Table 4.45: Assessment of the applicability of flash dry FGT 338 Table 4.46: Emission levels associated with the use of dry lime FGT 339 Table 4.47: Emission levels associated with the use of dry sodium bicarbonate FGT 339 Table 4.48: Cross-media effects associated with the use of dry FGT 340 Table 4.49: Operational data associated with the use of dry FGT 340 Table 4.50: Assessment of the applicability of dry FGT . 341 Table 4.51: Comparison of features of various alkaline reagents 342 Table 4.52: Assessment of the applicability of various alkaline reagents 343 Table 4.53: Operational data associated with the use of residue re-circulation . 345 Table 4.54: Assessment of the applicability of residue re-circulation . 346 Table 4.55: Assessment of the applicability of raw gas monitoring for optimisation of FGT . 348 Table 4.56: Emission levels associated with the use of SCR . 350 Table 4.57: Cross-media effects associated with the use of SCR 352 Table 4.58: Operational data associated with the use of SCR 352 Table 4.59: Assessment of the applicability of SCR 354 Table 4.60: Estimated investment costs of selected components of typical semi-wet FGT systems using SCR and SNCR 354 Table 4.61: Emission levels associated with the use of SNCR 356 Table 4.62: Cross-media effects associated with the use of SNCR 356 Table 4.63: Operational data associated with the use of SNCR 357 Table 4.64: Assessment of the applicability of SNCR . 358 Table 4.65: Advantages and disadvantages of urea and ammonia use for SNCR 359 Table 4.66: Assessment of the applicability of PCDD/F reformation prevention techniques 362 Table 4.67: Assessment of the applicability of SCR for PCDD/F removal . 364 Table 4.68: Destruction efficiency data for catalytic filter bags over 21 months of operation 366 Table 4.69: Assessment of the applicability of catalytic bag filters . 366 Table 4.70: Assessment of the applicability of re-burn of absorbers . 367 Table 4.71: Assessment of the applicability of carbon injection for PCDD/F removal . 369 Table 4.72: Cross-media effects associated with the use of static filters . 369 Table 4.73: Operational data associated with the use of static coke filters 370xxx Waste Incineration Table 4.74: Assessment of the applicability of static coke filters 371 Table 4.75: Operational data associated with the use of carbon impregnated materials in wet scrubbers372 Table 4.76: Assessment of the applicability of the use of carbon impregnated materials in wet scrubbers. 373 Table 4.77: Assessment of the applicability of wet scrubbing for Hg control 376 Table 4.78: Assessment of the applicability of carbon injection for Hg removal .377 Table 4.79: Assessment of the applicability of Na2S2O3 for halogen removal 383 Table 4.80: Quantity of HCl (30 %) recovered per tonne of waste 395 Table 4.81: Quantities of Gypsum recovered per tonne of waste treated .396 Table 4.82: Slag output concentration (mg/kg) data reported for an example slag treatment facility 406 Table 4.83: Slag output eluate (ug/l) data reported for an example slag treatment .407 Table 4.84: Relative yield of various output fractions of wet bottom ash treatment 408 Table 4.85: Example of leaching results of the produced granulates 409 Table 4.86: Slag output concentration (mg/kg) data reported for an example slag treatment facility 409 Table 4.87: Slag output eluate (ug/l) data reported for an example slag treatment .409 Table 4.88: Relative costs of some ash treatment techniques .411 Table 4.89: Variations in solidification treatments for FGT residues between some countries 414 Table 4.90: FGT vitrification processes used in the US and Japan 416 Table 4.91: Examples of plants using the acid extraction process for FGT residue treatment .418 Table 4.92: Characteristics of some acid extraction processes used for FGT residue treatment 418 Table 5.1: How to combine the BAT described for a specific case 434 Table 5.2 Operational emission level ranges associated with the use of BAT for releases to air from waste incinerators 441 Table 5.3: An example assessment of some IPPC relevant criteria that may be taken into account when selecting between wet/semi-wet/dry FGT options 443 Table 5.4: BAT associated operational emission levels for discharges of waste water from effluent treatment plant receiving FGT scrubber effluent 446 Table 6.1: Residue quality using SYNCOM system .458 Table 6.2: Emission levels associated with the use of combined dry sodium bicarbonate and SCR FGT system .467 Table 6.3: Cross-media effects associated with the use of combined dry sodium bicarbonate and SCR FGT system .467 Table 6.4: Operational data associated with the use of combined dry sodium bicarbonate and SCR FGT system .468 Table 6.5: Assessment of the applicability of the combined dry sodium bicarbonate and SCR FGT system 468 Table 9.1: Country codes and currencies .488 Table 10.1: Treatment costs for a MSW Grate Incinerator with varying capacity .491 Table 10.2: Grate MSW incinerator costs 200000 t/yr Germany .492 Table 10.3: Estimated cost to build and operate a mass-burn MSW incineration plant of 200000 tonne capacity in Ireland .493 Table 10.4: Incinerator costs in Italy based on model calculations 495 Table 10.5: Fees and expected amount of waste to be incinerated at SIDOR facility, Luxembourg in 1999 496 Table 10.6: Specific operational costs of the SIDOR MSWI in Luxembourg 1998 and 1999 .497 Table 10.7: Extract from the budget Of SIDOR for the years 1998 and 1999 498 Table 10.8: Capital investment and treatment costs for MSWI in NL 499 Table 10.9: Cost breakdown for various incinerators in Sweden .500 Table 10.10: UK gate fees for different incinerator capacities and energy outputs 500 Table 10.11: Breakdown of estimated United Kingdom incinerator costs .502 Table 10.12: Specific costs for discharge and storage facilities as a function of throughput when waste is delivered by refuse collection vehicles .505 Table 10.13: Specific costs for discharge and storage facilities as a function of throughput when waste is delivered by train 505 Table 10.14: Specific costs for a grate firing system and the boiler of waste incineration plants as a function of throughput 506 Table 10.15: Specific costs of a water-steam cycle with pure heat decoupling and feeding into district heating systems as a function of waste throughput .508 Table 10.16: Specific costs of a water-steam cycle comprising a steam extraction turbine as a function of waste throughput .509 Table 10.17: Specific costs of a water-steam cycle comprising a steam extraction turbine in combination with the steam system of an adjacent power plant as a function of waste throughput 510Waste Incineration xxxi Table 10.18: Specific costs of a water-steam cycle comprising cogeneration (CHP) and low steam parameters as a function of waste throughput 511 Table 10.19: Specific costs of a water-steam cycle comprising cogeneration (CHP) and high steam parameters as a function of waste throughput 511 Table 10.20: Specific costs of a water-steam cycle comprising a steam extraction turbine (normal steam parameters) as a function of waste throughput when energy can be substituted 511 Table 10.21: Specific costs of a water-steam cycle comprising cogeneration (CHP - normal steam parameters) as a function of waste throughput when energy can be substituted 512 Table 10.22: Specific costs of a water-steam cycle comprising cogeneration (CHP - high steam parameters) as a function of waste throughput when energy can be substituted 512 Table 10.23: Survey of specific income from different options of the water-steam cycle as a function of waste throughput 513 Table 10.24: Specific costs for dedusting with an electrostatic precipitator as a function of waste throughput 515 Table 10.25: Specific costs for wet dedusting as a function of waste throughput 515 Table 10.26: Specific costs of a dry flue-gas cleaning system with fabric filters as a function of waste throughput 516 Table 10.27: Specific costs of a dry flue-gas cleaning system with adsorption as a function of waste throughput 517 Table 10.28: Specific costs of a gypsum scrubber as a function of waste throughput . 517 Table 10.29: Specific costs of a scrubber with precipitation as a function of waste throughput 518 Table 10.30: Specific costs of a NaOH scrubber as a function of waste throughput . 518 Table 10.31: Specific costs of SCR as a function of waste throughput 519 Table 10.32: Specific costs of SNCR as a function of waste throughput . 520 Table 10.33: Specific costs of a flow injection absorber as a function of waste throughput 520 Table 10.34: Specific costs of an activated coke plant as a function of waste throughput . 521 Table 10.35: Option 1: Costs of a grate firing system incorporating delivery by train, dry, wet and catalytic flue-gas treatment and with the steam cycle connected to that of an adjacent power plant as a function of throughput 523 Table 10.36: Option 2: Costs of a grate firing system incorporating delivery by train, dry, wet and catalytic flue-gas treatment with power generation as a function of throughput 524 Table 10.37: Option 3: Costs of a grate firing system incorporating delivery by train, dry, wet and catalytic flue-gas treatment with cogeneration (CHP) as a function of throughput 524 Table 10.38: Option 4: Costs of a grate firing system incorporating delivery by train, electrostatic precipitator, NaOH scrubber, flow injection absorber and catalytic plant with power generation as a function of throughput . 525 Table 10.39: Option 5: Costs of a grate firing system incorporating delivery by train, electrostatic precipitator, precipitation, activated coke absorber and catalytic plant with power generation as a function of throughput . 525 Table 10.40: Option 6: Costs of a grate firing system incorporating delivery by train, dry adsorption, activated coke absorber and catalytic plant with power generation as a function of throughput 526 Table 10.41: Costs for the firing system and the boiler of waste incineration plants with fluidised bed combustion as a function of throughput (not including waste pretreatment costs) . 527 Table 10.42: Specific costs of a water-steam cycle comprising a steam extraction turbine (normal steam parameters) as a function of waste throughput . 528 Table 10.43: Specific costs and income of waste treatment, firing, boiler and energy utilisation . 528 Table 10.44: Capital and operating costs of the Lahti RDF gasification plant, Finland . 529 Table 10.45: Hypothetical cost calculations for a pyrolysis plant in the Flanders Region of Belgium 530 Table 10.46: General data of the waste incineration plant Flötzersteig (reference year: 2000) . 531 Table 10.47: Input and output flows of the waste incineration plant Flötzersteig (reference year: 2000)532 Table 10.48: Emissions to air from the waste incineration plant Flötzersteig (reference year: 2000) . 533 Table 10.49: Waste water parameters of the waste incineration plant Flötzersteig after the waste water treatment (reference year: 2000) . 534 Table 10.50: Chemical data of wastes from the waste incineration plant Flötzersteig (reference year: 2000) . 535 Table 10.51: Leaching tests; waste incineration plant Flötzersteig (reference year: 2000) 536 Table 10.52: General data of the waste incineration plant Spittelau (reference year: 2000) 536 Table 10.53: Input-output flows of the waste incineration plant Spittelau (reference year: 2000) 537 Table 10.54: Emissions to air from the waste incineration plant Spittelau (reference year: 2000) 539 Table 10.55: Waste water parameters of the waste incineration plant Spittelau after treatment (reference year: 2000) 540xxxii Waste Incineration Table 10.56: Chemical data of waste fractions from the waste incineration plant Spittelau (reference year: 2000) .541 Table 10.57: Leaching tests; waste incineration plant Spittelau (reference year: 2000) .542 Table 10.58: General data of the waste incineration plant Wels (reference year: 2000) 542 Table 10.59: Input and output of the waste incineration plant Wels (reference year: 2000) 543 Table 10.60: Emissions to air from the waste incineration plant Wels (reference year: 2000) .545 Table 10.61: Waste water parameters of the waste incineration plant Wels after waste water treatment (reference year: 2000) .546 Table 10.62: Average values measured in clean gas (operating values) 547 Table 10.63: Slag quality 548 Table 10.64: Energy efficiency ratio (assumed average calorific value 9500 kJ/kg) 548 Table 10.65: Types of waste and waste quantities incinerated in the rotary kilns of Plant Simmeringer Haide (reference year: 2000) .554 Table 10.66: General data of the rotary kilns of the Plant Simmeringer Haide (reference year: 2000)
كلمة سر فك الضغط : books-world.net The Unzip Password : books-world.net أتمنى أن تستفيدوا من محتوى الموضوع وأن ينال إعجابكم رابط من موقع عالم الكتب لتنزيل كتاب Reference Document on the Best Available Techniques for Waste Incineration رابط مباشر لتنزيل كتاب Reference Document on the Best Available Techniques for Waste Incineration 
|
|