Admin مدير المنتدى


عدد المساهمات : 18994 التقييم : 35488 تاريخ التسجيل : 01/07/2009 الدولة : مصر العمل : مدير منتدى هندسة الإنتاج والتصميم الميكانيكى
 | موضوع: رسالة ماجستير بعنوان Use of Composites as Alternative Materials in Ship Structures الخميس 17 ديسمبر 2020, 12:24 am | |
| 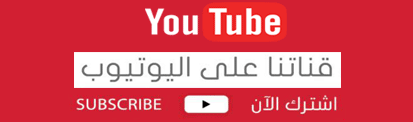
أخوانى فى الله أحضرت لكم رسالة ماجستير بعنوان Use of Composites as Alternative Materials in Ship Structures A thesis Submitted to the Naval Architecture and Marine Engineering Department Faculty of Engineering – Alexandria University in partial fulfillment of the requirements for the degree of Master of Science in Naval Architecture by Basem E. Tawfik Advisors' Committee: Prof. Heba Wael Leheta Prof. Tarek Elsayed Prof. Ahmed Elhewy استخدام المواد المركبة كمواد بديلة في المنشآت البحرية رسالة علمية مقدمة الى قسم الهندسة البحرية و عمارة السفن بكلية الهندسة – جامعة الاسكندرية استيفاء للدراسات المقررة للحصول على درجة ماجستير العلوم فى العمارة البحرية مقدمة من باسم السيد توفيق
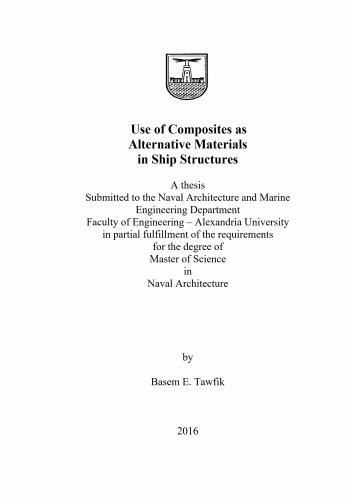 و المحتوى كما يلي :
الملخص عن طريق إستخدام المواد المركبة يتمكن المصممون من إستغلال أحسن الخواص الموجودة بمكوناتها مم يؤدي إلى تصميم منشآت ذكية و فعالة ، في الرسالة التي بين يديكم ،تم تقديم المواد المركبة كبديل للمواد المعدنية في المنشآت البحرية. و قد تم بيان المزايا التي تقدمها المواد المركبة مم يؤهلها لتحل محل المواد المعدنية في العديد من التطبيقات ، حيث أنه مع التصميم الماهر و الذكي سوف تتحول هذة المزايا إلى أداء فعال و جدوى إقتصادية عالية. تم التعريف بأنواع و تصنيفات المواد المركبة كما تم أيضا وصف المكونات المركبة لكل نوع من الأنواع ، ثم بعد ذلك تم مناقشة المزايا التي تقدمها المواد المركبة كما تم كذلك الحديث عن بعض العيوب التي يجب أخذها في الإعتبار خلال التصميم. علاوة على ذلك ، تمت مناقشة طرق التصنيع الفريدة للمواد المركبة و التي يجب على المصمم الإختيار منها.ثم تم استعراض المبادئ الأساسية لميكانيكا المواد المركبة و طرق التصميم التي تشكل الأدوات اللازمة لمباشرة تصميم المنشآت المكونة من المواد المركبة. بعد ذلك ، تمت مراجعة التطبيقات الحالية للمواد المركبة في المجالات البحرية التجارية ، الترفيهية و الحربية أيضا. و قد تمت كذلك المراجعة على المنشآت البحرية المصنوعة كليا أو جزئيا من المواد المركبة. حيث أنه تم توضيح أن المواد المركبة تلعب دورا واسعا اليوم في بناء الهياكل الكاملة للقوارب الشراعية و ذات المحركات أيضا في مجالات السباق و الترفيه و بعض السفن التجارية الصغيرة. كما أنها تستخدم في بناء العديد من المكونات الإضافية في السفن المصنوعة من المعادن مثل الرفاصات ، الدفة ، أغطية العنابر ، المداخن ، المنشآت الفوق سطحية ، أنظمة الصواري ، القواعد و العديد من التطبيقات الأخرى. كما تم أيضا الإشارة إلى أن ألياف الكاربون و الكيفلار ( )Kevlarيتم إستخدامها بكثافة في التطبيقات التي تطلب أداءا عاليا لتحل محل ألياف الزجاج الذي يستخدم بصورة تقليدية في المنشآت البحرية. تم تقديم المواد المركبة كمواد بديلة لصناعة أغطية العنابر كحالة بحثية ، حيث أن أغطية العنابر الخاصة بسفينة بضاعة صب حمولة 12228طن قد تم تصميمها بأستخدام المواد المركبة. و قد تم إستخدام منهجين منفصلين في تصميم أغطية العنبر البحرية المركبة. المنهج الأول هو "منهج التقوية" حيث تم زيادة الحمل على غطاء العنبر الأمامي بما يعادل %851من الحمل الذي يتم تصميم الغطاء لتحمله (كما هو مطلوب من هيئات التصنيف البحرية) بدون زيادة في وزن الغطاء عن طريق إستغلال خاصية "القوة العالية مقابل الوزن" التي تتميز بها المواد المركبة ، مم يؤدي إلى زيادة معامل الأمان ضد غرق العنبر في السفن الكبيرة. المنهج الثاني هو "منهج تخفيف الوزن" حيث تم تصميم أغطية العنابر بحيث يكون وزنها %55.51من وزن الأغطية المعدنية و بالتالي تؤدي إلى تحسين إتزان السفينة و تقليل إستهلاك الوقود. علاوة على ذلك تم دراسة "تكلفة دورة حياة" أغطية العنابرالمبنية من المواد المركبة و مقارنتها بتكلفة دورة حياة أغطية العنابر المعدنية ، حيث أكدت النتائج على أن تكلفة دورة حياة الأغطية المصنوعة من المواد المركبة أقل بسبب زيادة تكاليف صيانة الأغطية المعدنية لتكرار حدوث مشاكل الصدأ و هو ما لا يحدث في المواد المركبة. و على الرغم من النجاح و الإنتشار الحالي الذي حققته المواد المركبة في المجال البحري فإن المجال ما زل مفتوحا و مليئا بالإمكانات للعديد من التطبيقات الجديدة المبتكرة في جميع الفروع البحرية. TABLE OF CONTENTS ACKNOWLEDGMENT i TABLE OF CONTENTS ii LIST OF FIGURES vi LIST OF TABLES . x LIST OF ABBREVIATIONS . xi NOMENCLATURE xiii ABSTRACT .xv CHAPTER 1 :INTRODUCTION 1 CHAPTER 2 :OVERVIEW OF COMPOSITE MATERIALS . 3 2.1.BACKGROUND .3 2.2.DEFINITION OF COMPOSITES .4 2.3.TYPES AND CLASSIFICATION OF COMPOSITE MATERIALS 5 2.3.1.Particle-Reinforced Composites .5 2.3.2.Fiber-Reinforced Composites .7 2.3.3.Structural Composites: 9 2.3.4.Hybrid Composites .12 2.3.5.Advanced Composites 13 2.4.CONSTITUENT MATERIALS 14 2.4.1.Reinforcement .14 2.4.2.Matrix 23 2.4.2.1.Thermosets .25 2.4.2.1.1.Epoxies 25 2.4.2.1.2.Bismaleimides .26 2.4.2.1.3.Polyimides .26 2.4.2.1.4.Polyesters and vinyl esters 26 2.4.2.1.5.Cyanate esters .27 2.4.2.1.6.Phenolics .27 2.4.2.2.Thermoplastics .27 2.4.3.Core Materials .28 2.4.3.1.Balsa 29 2.4.3.2.ThermosetFoams 30 2.4.3.3.SyntacticFoams 30 2.4.3.4.Cross Linked PVC Foams 31 2.4.3.5.Linear PVC Foam 31 2.4.3.6.Honeycomb 32 2.4.3.7.PMI Foam 32 2.4.3.8.FRP Planking .32 2.4.3.9.Plywood .33 2.5.ADVANTAGES AND DISADVANTAGES OF COMPOSITE MATERIALS 33 2.5.1.Strength and Stiffness Advantages .34 2.5.2.Cost Advantages .37 2.5.3.Weight Advantages .39 2.5.4.Disadvantages .40 2.6.MARKET DEMAND FOR COMPOSITE MATERIALS 41 2.7.PRODUCTION (MANUFACTURING) METHODS .42 2.7.1.Hand Lay-Up 43iii 2.7.1.1.Process description 43 2.7.1.2.Resin Systems .44 2.7.1.3.Molds .44 2.7.1.4.Major Advantages 44 2.7.2.Spray-Up .44 2.7.2.1.Process Description .44 2.7.2.2.Resin Systems .45 2.7.2.3.Molds .45 2.7.2.4.Major Advantages 45 2.7.3.Filament Winding .45 2.7.3.1.Process Description .46 2.7.3.2.Resin Systems .46 2.7.3.3.Molds .46 2.7.3.4.Major Advantages 46 2.7.4.Pultrusion 47 2.7.4.1.Process Description .47 2.7.4.2.Resin Systems .47 2.7.4.3.Molds .47 2.7.4.4.Major Advantages 47 2.7.5.Vacuum Bag Molding .48 2.7.5.1.Process Description .48 2.7.5.2.Resin Systems .48 2.7.5.3.Molds .48 2.7.5.4.Major Advantages 48 2.7.6.SCRIMP 49 2.7.6.1.Process Description .49 2.7.6.2.Resin Systems .49 2.7.6.3.Molds .49 2.7.6.4.Major Advantages 49 2.7.7.Autoclave Molding .50 2.7.7.1.Process Description .50 2.7.7.2.Resin Systems .50 2.7.7.3.Molds .50 2.7.7.4.Major Advantages 51 2.7.8.Resin Transfer Molding 51 2.7.8.1.Process Description .51 2.7.8.2.Resin System 51 2.7.8.3.Molds .52 2.7.8.4.Major Advantages 52 2.7.9.Compression Molding .52 2.7.9.1.Process Description .52 2.7.9.2.Resin Systems .53 2.7.9.3.Molds .53 2.7.9.4.Major Advantages 53 CHAPTER 3 : MECHANICS OF COMPOSITE MATERIALS .54 3.1.INTRODUCTION .54 3.1.1.Mechanical Response .56 3.1.2.Coordinate System 57iv 3.2.MACROMECHANICAL BEHAVIOR OF A LAMINA .60 3.2.1.Stress–Strain Relationships .60 3.2.2.Engineering Constants for Orthotropic Materials .63 3.2.3.Strength Criteria for an Orthotropic Lamina 65 3.2.3.1.“Maximum Stress” Failure Criterion 66 3.2.3.2.“Maximum Strain” Failure Criterion .67 3.2.3.3.Quadratic Failure Criterion 67 3.3.MICROMECHANICAL BEHAVIOR OF A LAMINA .68 3.3.1.Elastic Properties 69 3.3.2.Lamina Strength 70 3.4.MECHANICAL BEHAVIOR OF A LAMINATE .71 3.4.1.Classical Lamination Theory 72 3.4.1.1.Lamina Stress-Strain Behavior 72 3.4.1.2.Strain and Stress Variation in a Laminate .73 3.4.1.3.Resultant Laminate Forces and Moments .75 3.4.2.Strength of Laminates .78 3.4.3.Computer Laminate Analysis .80 3.4.4.Carpet Plots .81 CHAPTER 4 : COMPOSITES APPLICATIONS IN SHIP STRUCTURES 84 4.1.INTRODUCTION .84 4.2.MATERIALS AND PRODUCTION METHODS 86 4.3.COMPLETE COMPOSITE HULLS .90 4.3.1.Recreational Industry 90 4.3.1.1.Power racing boats 90 4.3.1.2.Sail racing boats 93 4.3.1.2.1.The Volvo Ocean Race 93 4.3.1.2.2.Volvo Ocean 65 Race Boat .94 4.3.1.3.Pleasure yachts 97 4.3.1.3.1.Evviva 97 4.3.1.3.2.SuperSport 98 4.3.1.3.3.(M5) Mirabella V 100 4.3.1.3.4.Tûranor Solar Yacht Hull .101 4.3.2.Commercial Industry 103 4.3.2.1.SSC study .104 4.3.2.2.Passenger ferries .104 4.3.2.2.1.Composite Ferries for USA Market 105 4.3.2.2.2.Composite Ferry vs. Aluminum Ferry 106 4.3.2.3.Wave star Energy system .107 4.3.2.4.FRP lifeboat .109 4.3.3.Naval Vessels 109 4.3.3.1.Patrol boats 111 4.3.3.2.Mine counter measure vessels (MCMV) 112 4.3.3.2.1.Landsort / Koster Class MCMV 113 4.3.3.3.Corvettes 115 4.3.3.3.1.Visby class Corvettes 115 4.3.3.3.1.1.Materials 116 4.3.3.3.1.2.Construction technique 117 4.4.COMPOSITE PARTS .118v 4.4.1.Superstructures 119 4.4.1.1.DDG-1000 Zumwalt class .119 4.4.1.2.Passenger ship’s Superstructure .123 4.4.1.3.Superstructure of a RoRo vessel 127 4.4.2.Hatch Covers .129 4.4.2.1.Oshima ECO-Ship 2020 .129 4.4.2.2.M/V Nordic Oshima .130 4.4.3.Propellers 130 4.4.3.1.Alkmaar-class mine hunter 131 4.4.3.2.QinetiQ propeller .133 4.4.3.3.Nakashima Propeller .134 4.4.4.Rudders .136 4.4.4.1.Composite twisted Rudders 136 4.4.5.Propulsion Shafts 138 4.4.5.1.Early trials .139 4.4.5.2.JIME Research .139 4.4.5.3.Expeditionary Fighting Vehicle power systems .140 4.4.6.Advanced Enclosed Mast System .141 4.5.MARINE COMPOSITES ROADBLOCKS 144 CHAPTER 5 : CASE STUDY (MARINE HATCH COVERS FOR LARGE VESSELS) 145 5.1.INTRODUCTION .145 5.2.DESIGN KEYS 145 5.3.PARTICULARS OF SELECTED VESSEL .146 5.4.CALCULATION OF DESIGN LOADS .148 5.5.DESIGN OF STEEL HATCH COVERS 149 5.6.DESIGN OF COMPOSITE HATCH COVERS .151 5.6.1.Selection of Composite Material 151 5.6.2.Laminate Orientation 152 5.6.3.Failure Criteria 154 5.6.4.Calculation of Member’s Thickness .154 5.6.4.1.Strengthening Approach 155 5.6.4.1.1.Composite cover design 155 5.6.4.1.2.Analysis results and discussion .157 5.6.4.2.Weight Reduction Approach 159 5.6.4.2.1.Composite cover design 159 5.6.4.2.2.Analysis of results and discussion 161 5.7.COST ANALYSIS 163 5.7.1.Manufacturing Cost 163 5.7.1.1.Steel Hatch cover .163 5.7.1.2.Composite hatch cover .164 5.7.2.Life Cycle Cost Analysis (LCCA) 164 5.8.SUMMARY 165 CHAPTER 6 :CONCLUSIONS AND SUGGESTIONS FOR FUTURE WORK 167 REFERENCES .169 ARABIC SUMMARY .178vi LIST OF FIGURES Figure 2-1 Relationships between Classes of Engineering Materials Showing the Evolution of Composites [Harris Bryan 1999] . 5 Figure 2-2 Principal Composite Materials [Vinson et al. 2004] 6 Figure 2-3 A Classification Scheme for the Various Composite Types [Callister 2001] 6 Figure 2-4 Various Types and Orientation of Fibrous Composites [Mallick 2008] 8 Figure 2-5 A Laminate Made-up of Laminae with Different Fiber Orientations [Reddy 2004] 10 Figure 2-6 Schematic Diagram Showing the Construction of a Honeycomb Core Sandwich Panel [Callister 2001] 11 Figure 2-7 Efficiency of the Sandwich Structure [Campbell 2010] 11 Figure 2-8 A Cross Section of a High-Performance Snow Ski [Callister 2001] . 12 Figure 2-9 Some Fiber Construction Forms [Campbell 2010] 15 Figure 2-10 Unidirectional and Woven Cloth Prepreg [Campbell 2010] 16 Figure 2-11 Tensile Stress–Strain Diagrams for Various Reinforcing Fibers [Mallick 2008] . 20 Figure 2-12 Specific Strength and Modulus of Some Commercially Important Fibers [Campbell 2010] 23 Figure 2-13 Comparison of Thermoset and Thermoplastic Polymer Structures [Campbell 2010] 24 Figure 2-14 Cost Versus Performance for Core Materials [Campbell 2010] 28 Figure 2-15 Balsa Cell Geometry [Greene 1999] 29 Figure 2-16 Syntactic Core Construction [Campbell 2010] 31 Figure 2-17 Translation from Constituent Properties to Lamina to Laminate Properties [Jones 1999] . 35 Figure 2-18 Strength and Stiffness of Composite Materials and Metals [Jones 1999] . 36 Figure 2-19 Life-Cycle Cost Elements [Jones 1999] . 38 Figure 2-20 The Relative Importance of Metals, Polymers, Composites, and Ceramics asa Function of Time. The Diagram is Schematic and Describes neither Tonnage nor Value. The Time Scale is Nonlinear [Gibson 1994] . 42 Figure 2-21 Comparison of Composite Manufacturing Techniques [Potter 1996] . 43 Figure 2-22 Schematic of the Hand Lay-up Process [Gurit 2013] 43 Figure 2-23 Schematic of the SPRAY-UP Process [Gurit 2013] 45 Figure 2-24 Schematic of the Filament Winding Process [Gurit 2013] 46 Figure 2-25 Schematic of the Pultrusion Process [Callister 2001] 47 Figure 2-26 Schematic of the Vacuum Bag Molding Process [Gurit 2013] 48 Figure 2-27 Schematic of SCRIMP [Gurit 2013] 49 Figure 2-28 A schematic of Autoclave molding process [Gurit 2013] 50 Figure 2-29 A Schematic of Resin Transfer Molding Process [Gurit 2013] . 51 Figure 2-30 Schematic of the Compression Molding Process [Mazumdar 2002] . 52 Figure 3-1 Material with Three Planes of Symmetry [Kollar eta al. 2003] . 54vii Figure 3-2 The Levels of Analysis for a Structure Made of Laminated Composite [Kollar eta al. 2003] 55 Figure 3-3 Mechanical Behavior of Various Materials [Jones 1999] 57 Figure 3-4 The Global x, y, z and Local x1, x2, x3 Coordinate Systems [Kollar eta al. 2003] . 57 Figure 3-5 The x, y, z and x1, x2, x3 Coordinate Systems and the Corresponding Displacements [Kollar eta al. 2003] 58 Figure 3-6 The Stresses in the Global x, y, z and the Local x1, x2, x3 Coordinate Systems [Kollar eta al. 2003] . 58 Figure 3-7 Stresses on an Element [Jones 1999] . 60 Figure 3-8 Typical Failure Modes of Composites [Kollar 2003] 65 Figure 3-9 Load-Displacement Curve of a Composite Part [Kollar 2003] 66 Figure 3-10 Representative Volume Element Loaded in the 1-Direction [Jones 1999] 69 Figure 3-11 The Basic Questions of Laminate Analysis . 71 Figure 3-12 Geometry of Deformation in the x-z Plane [Jones 1999] 74 Figure 3-13 Hypothetical Variation of Strain and Stress through the Laminate Thickness [Jones 1999] . 75 Figure 3-14 In-Plane Forces on a Flat Laminate [Jones 1999] 76 Figure 3-15 Moments on a Flat Laminate . 76 Figure 3-16 Geometry of an N-Layered Laminate [Jones 1999] . 77 Figure 3-17 Laminate Strength-Analysis Elements [Jones 1999] . 78 Figure 3-18 Analysis of Laminate Strength and Load-Deformation Behavior [Jones 1999] . 79 Figure 3-19 Carpet Plots for [0°, ±45°, 90°] Kevlar Epoxy Laminates [Gibson 1994] 82 Figure 4-1 Marine Industry Reinforcement Material Use [Greene 1999] . 87 Figure 4-2 Marine Industry Reinforcement Style Use . 88 Figure 4-3 Marine Industry Resin System Use 88 Figure 4-4 Marine Industry Core Material Use . 89 Figure 4-5 Building Processes within the Marine Industry . 89 Figure 4-6 Dubai Grand Prix in 2012 [Class-1 2012] . 91 Figure 4-7 Earthrace Power Boat [Greene 2013b] 92 Figure 4-8 The Route of the 2014-15 Volvo Ocean Race [Volvo Ocean Race 2016d] 93 Figure 4-9 Volvo Ocean 65 Race Boat During Manufacture by Vacuum Bagging Infusion in Italy [Farr Yacht Design 2012] 94 Figure 4-10 A 3D Model of Volvo Ocean 65 Boat [Volvo Ocean Race 2016a] . 96 Figure 4-11 Volvo Ocean 65 Boat in Real Operation [Scuttlebutt 2013] . 97 Figure 4-12 M/Y Evviva [Super yachts 2016b] . 98 Figure 4-13 MY Supersport 48M [Morpheus London 2015] 99 Figure 4-14 MY Supersport 72M [Palmer johnson 2016b] . 100 Figure 4-15 M5, Ex Mirabella V [Super yachts 2016c] 101 Figure 4-16 MY Turanor PlanetSolar [Greene 2013b] 102 Figure 4-17 Design Characteristics of Turanor Solar Yacht [Black 2011b] . 103viii Figure 4-18 LCC Comparison on High Speed Ferry [Petersson 2004] . 105 Figure 4-19 Comparison between Aluminum and CFRP Ferries [Arcadia-alliance 2016] . 106 Figure 4-20 A Comparison of Carbon Footprint Reduction of the 2 Ferries [Arcadia-alliance 2016] 107 Figure 4-21 Wave Star Energy System [Wavestar 2016] 108 Figure 4-22 Example Photos Showing the Production Process from Danish Yachts [Danish composites 2015] . 108 Figure 4-23 A Totally Enclosed GRP Lifeboat [Norsafe 2016] 109 Figure 4-24 Plot of Vessel Length against Year of Construction for All-Composite Patrol Boats, MCMV and Corvettes [Mouritz 2001] . 110 Figure 4-25 The Skjold Class Patrol Boat [Greene 2013b] . 111 Figure 4-26 Landsort Class MCMV [Naval-technology 2016a] . 114 Figure 4-27 One of the Landsort Class MCMV during Construction [Naval-technology 2016a] 114 Figure 4-28 HMS Nykoping K34, Visby Class Corvette of Swedish Navy during a Visit to Gothenburg [Ships and harbours 2013] . 116 Figure 4-29 USS Zumwalt [Naval-technology 2016c] 120 Figure 4-30 The Deckhouse of USS Zumwalt [LeGault 2010] . 121 Figure 4-31 The Composite Deckhouse during Construction [Composites World 2013] . 122 Figure 4-32 Completed Composite Deckhouse [Greene 2013b] 123 Figure 4-33 M/S Norwegian Gem [Evegren et al. 2011] 124 Figure 4-34 Illustration of the Design Changes Made to the Norwegian Gem to Form the Novel Design of the Norwegian Future [Evegren et al. 2011] 125 Figure 4-35 The Cruise Ship Norwegian Gem and the Structure (Marked) Intended for Reconstruction in FRP Composite from Deck 11 and up [Evegren et al. 2011] . 125 Figure 4-36 The Maximum Modelled Hogging for the Existing Norwegian Gem (top), the Norwegian Future (mid) and the Norwegian Future with Increased Deck Plating (bottom) [Evegren et al. 2011] 126 Figure 4-37 Characteristics of Vessel under Study [Petersson 2004] . 128 Figure 4-38 A Demonstration of the Reduction in VCG after Implementing Composite Superstructure [Petersson 2004] 128 Figure 4-39 An Illustration Showing the Proposed Solution for Oshima ECO-Ship 2020 [Mori 2011] 129 Figure 4-40 Nordic's M/V Nordic Oshima Panamax Vessel [Ship Technology 2015] . 130 Figure 4-41 The Composite Propeller Blade, Attached to the Bronze Blade Foot that Forms the Interface with the Existing Metallic Propeller Hub [Black 2011a] . 131 Figure 4-42 Airborne Composites' Composite Blades for Controllable-Pitch Ship Propeller Illustration [Black 2011a] 132 Figure 4-43 The Completed Prototype Blades Are Shown Installed on a Minehunter’s Propeller Hub [Black 2011a] . 133ix Figure 4-44 CFRP after Installation on MV “Taiko Maru” [Marex 2016] . 135 Figure 4-45 Twisted Rudder on the USS Bulkeley [Griffiths 2006] . 136 Figure 4-46 Internal Design of the Hybrid Steel/Composite Twisted Rudder 137 Figure 4-47 Carbon Fiber Propulsion Shaft [Greene 2013a] . 138 Figure 4-48 Lamination of the Hybrid Composite Shaft [Sunahara et al. 1992] . 140 Figure 4-49 Composite Driveshafts on the Expeditionary Fighting Vehicle [Mason 2004] . 140 Figure 4-50 An Insight View of the AEMS [Greene 2013c] . 142 Figure 4-51 AEMS on San Antonio Class LPD-17 [Greene 2013c] . 142 Figure 4-52 AEMS During Installation, the Enclosed Radar System Still Visible [Greene 2013c] 143 Figure 4-53 Applications of composite structures to naval ships [Mouritz et al. 2001] 143 Figure 5-1 An Overview of the Case Study Vessel . 146 Figure 5-2 Arrangement of ship’s Cargo Holds and Covers . 147 Figure 5-3 Hatch Cover Design According to IACS UR S21 and ILLC 66 . 148 Figure 5-4 Construction of Steel Hatch Cover Number 1 . 151 Figure 5-5 Properties of a Lamina . 152 Figure 5-6 Properties of a Laminate 153 Figure 5-7 Laminate Orientation . 153 Figure 5-8 Scantling Criteria for the Composite Hatch Cover. . 155 Figure 5-9 Thickness of Composite Hatch Cover. 156 Figure 5-10 Thickness of Reinforcements at the Connections between Sides and Stiffeners . 157 Figure 5-11 IRF of Tsai Wu and Pucks Failure Theories on Composite Hatch Cover 158 Figure 5-12 Deformation of Composite Hatch Cover . 158 Figure 5-13 Thickness of Composite Hatch Cover Number 1 160 Figure 5-14 Thickness of Reinforcements at the Connections between Sides and Stiffeners . 160 Figure 5-15 IRF of Tsai Wu and Pucks Failure Theories on Composite Hatch Cover Number 1 . 161 Figure 5-16 Deformation of Composite Hatch Cover Number 1 162 Figure 5-17 Comparison of Steel and Composite Hatch Cover Weights 163 Figure 5-18 Distribution of Hand Layup Costs for HLU Process [Haffner 2002] 164 Figure 5-19 An Illustration of the Concept of Break-Even Analysis (alternative A: Composite, Alternative B: Steel) . 166x LIST OF TABLES Table Page Table 2-1 Structural performance ranking of conventional materials [Daniel et al. 1994] . 3 Table 2-2 Fiber and wire properties [Jones 1999] . 7 Table 2-3 Description of various forms of reinforcements [Greene 1999] . 15 Table 2-4 Properties of Selected Commercial Reinforcing Fibers [Mallick 2008] . 21 Table 2-5 Relative characteristics of thermoset resin matrices [Campbell 2010] . 25 Table 2-6 Comparative data for some sandwich core materials [Greene 1999] 29 Table 2-7 Characteristics of some foam sandwich materials [Campbell 2010] 32 Table 3-1 Stress notations [Kollar eta al. 2003] 59 Table 3-2 Strain notations [Kollar eta al. 2003] 59 Table 3-3 Typical input and output variables for laminate analysis programs [Greene 1999] . 81 Table 4-1 Specifications of the Earthrace boat [Earthrace 2008] 92 Table 4-2 Specifications of the Volvo Ocean 65 boat [Volvo Ocean Race 2016b] 95 Table 4-3 Principal particulars of MY Evviva [Super yachts 2016b] . 98 Table 4-4 Particulars of MY Supersport 48M [Palmer johnson 2016a] 99 Table 4-5 Particulars of MY Supersport 72M [Palmer johnson 2016b] 100 Table 4-6 Particulars of M5 [Super yachts 2016c] 101 Table 4-7 Perceived limitations of FRP in ships [Horsmon 1993] 104 Table 4-8 Survey of GRP mine counter measure vessels in-service or under construction as at 3/12/1999 [Mouritz 2001] 113 Table 4-9 Principal particulars of USS Zumwalt [Naval-technology 2016c] . 119 Table 4-10 The modelled ability to manage global forces in different design solutions [Evegren et al. 2011] 127 Table 5-1 Principal particulars of selected vessel 147 Table 5-2 Principal particulars of selected vessel 149 Table 5-3 Hatch Covers Dimensions . 150 Table 5-4 Weights of steel hatch covers 150 Table 5-5 Composite material properties . 151 Table 5-6 Design thickness of hatch cover components 156 Table 5-7 Design thickness of the components of hatch cover number 1. 159 Table 5-8 Steel and composite covers weights and weight reduction value . 162 Table 5-9 Summary of basic life cycle cost analysis . 165xi LIST OF ABBREVIATIONS AAAV Advanced Amphibious Assault Vehicle ACP ANSYS Composite Preppost AEM/S Advanced Enclosed Mast/Sensor System ASROC Anti-Submarine Rocket ASTM American Society For Testing And Materials B/E Break-Even BMIS Bismaleimides CC Carbon-Carbon CCA Cellular Cellulose Acetate CFRP Carbon Fibre Reinforced Plastics CLT Classical Lamination Theory CMC Ceramic Matrix Composites CNC Computer Numerical Control CSMS Chopped Strand Mats DMAC Dimethylactamide DMF Dimethylformamide DMSO Dimethylsufoxide DNV Det Norske Veritas DWT Dead Weight EFV Expeditionary Fighting Vehicle EMI Electromagnetic Interference EMS Electro-Magnetic Signature FEA Finite Element Analysis FEM Finite Element Model FRP Fiber-Reinforced Plastics GRP Glass Reinforced Plastics HLU Hand Lay-Up HMS Her Majesty's Ship HSC High Speed Craft IACS International Association Of Classification Societies ILLC 66 International Load Line 1966 IMO International Maritime Organization IR Infrared IRF Inverse Reserve Factorxii JIME Japan Institute of Marine Engineering LCC Life Cycle Cost LCCA Life Cycle Cost Analysis MCA Maritime And Coastguard Agency MCMV Mine Counter Measure Vessels MLU Mid-Life Upgrades MMC Metal Matrix Composites MODU Mobile Offshore Drilling Unit MY Motor Yacht NAB Nickel-Aluminum-Bronze NMP N-Methylpyrrolidone NVH Noise, Vibration, And Harshness PJ Palmer Johnson PMC Polymer Matrix Composites PMI Polymrthacrylimide PVA Polyvinyl Acetate PVC Polyvinyl Chloride RNLN Royal Netherlands Navy RORO Roll-On Roll-Off ROV Remotely Operated Vehicle RTM Resin Transfer Molding SCRIMP Seemann Composites Resin Infusion Molding Process SOLAS Safety Of Life At Sea SSC Ship Structures Committee UK United Kingdom US United States USS United States Ship VARTM Vacuum-Assisted Resin Transfer Moldingxiii NOMENCLATURE Aij Laminate Extensional Stiffness Bij Laminate Bending-Extension Coupling Stiffness Cij Stiffness Matrix Dij Laminate Bending Stiffness Ei Young's (Extension) Moduli in i Direction (Pa) F Strength Parameter of Quadratic Failure Criterion Gij Shear Moduli in the i j (i, j = 1, 2, 3) Plane (Pa) Kf Volume Fraction of the Fibers Km Volume Fraction of the Matrix L Freeboard Length, as defined in Regulation 3 of Annex I to the 1966 Load Line Convention (m) ℓ The Greatest Span of Primary Supporting Members Mi Moment per Unit Width of the Cross Section of the Laminate in the i Direction Ni Force per Unit Width of the Cross Section of the Laminate in the i Direction P Pressure Load on Ship’s Hatch Cover (kN/m2) PFP Pressure at the Forward Perpendicular (kN/m2) PHi Pressure Load on Hatch cover Number i (kN/m2) Qij Transformed Reduced Stiffnesses S+i Tensile Strength in the i Direction (MPa) S+i j Shear Strength in the i j (i, j = 1, 2, 3) Plane (MPa) S−i Compressive Strength in the i Direction (MPa) Sij Compliance Matrix V Volume of the Composite (m3) V m Volume of the Matrix (m3) Vf Volume of the Fiber (m3) x Distance of the mid length of the hatch cover under examination from the forward end of L (m) αf Thermal Expansion Coefficient of the fibers (°C−1) αi Thermal Expansion Coefficient of the Composite in the i Direction (°C−1) αm Thermal Expansion Coefficient of the Matrix (°C−1) γij Engineering Shear Strain in the i j (i, j = 1, 2, 3) Plane εi Normal Strain in i Direction η+i Allowable Tensile Strain in the i Direction η+ij Allowable Shear Strain in the i j (i, j = 1, 2, 3) Planexiv η−i Allowable Compressive Strain in the i Direction νij Poisson's Ratio (Extension-Extension Coupling Coefficient) ρ Density of the Composite (t/m3) ρf Density of the Fiber (t/m3) ρm Density of the Matrix (t/m3) σi Normal Stress in i Direction (pa) τij Shear Stress in the i j (i, j = 1, 2, 3) Plane (pa) Ө Fiber Orientation Angle (Degree)
كلمة سر فك الضغط : books-world.net The Unzip Password : books-world.net أتمنى أن تستفيدوا من محتوى الموضوع وأن ينال إعجابكم رابط من موقع عالم الكتب لتنزيل رسالة ماجستير بعنوان Use of Composites as Alternative Materials in Ship Structures رابط مباشر لتنزيل رسالة ماجستير بعنوان Use of Composites as Alternative Materials in Ship Structures 
|
|